The speed of rotation of a ball mill cylinder is a critical factor that directly influences the efficiency and effectiveness of the grinding process. It determines the motion of the grinding balls and the impact they have on the material being ground. Operating at the correct speed ensures that the balls cascade and tumble, maximizing size reduction. If the speed is too low, the balls slide or roll without effective grinding, while excessively high speeds cause the balls to stick to the cylinder walls due to centrifugal force, preventing grinding. The optimal speed, typically slightly below the critical speed, ensures a balance between impact and cascading motion, leading to efficient grinding and desired particle size reduction.
Key Points Explained:
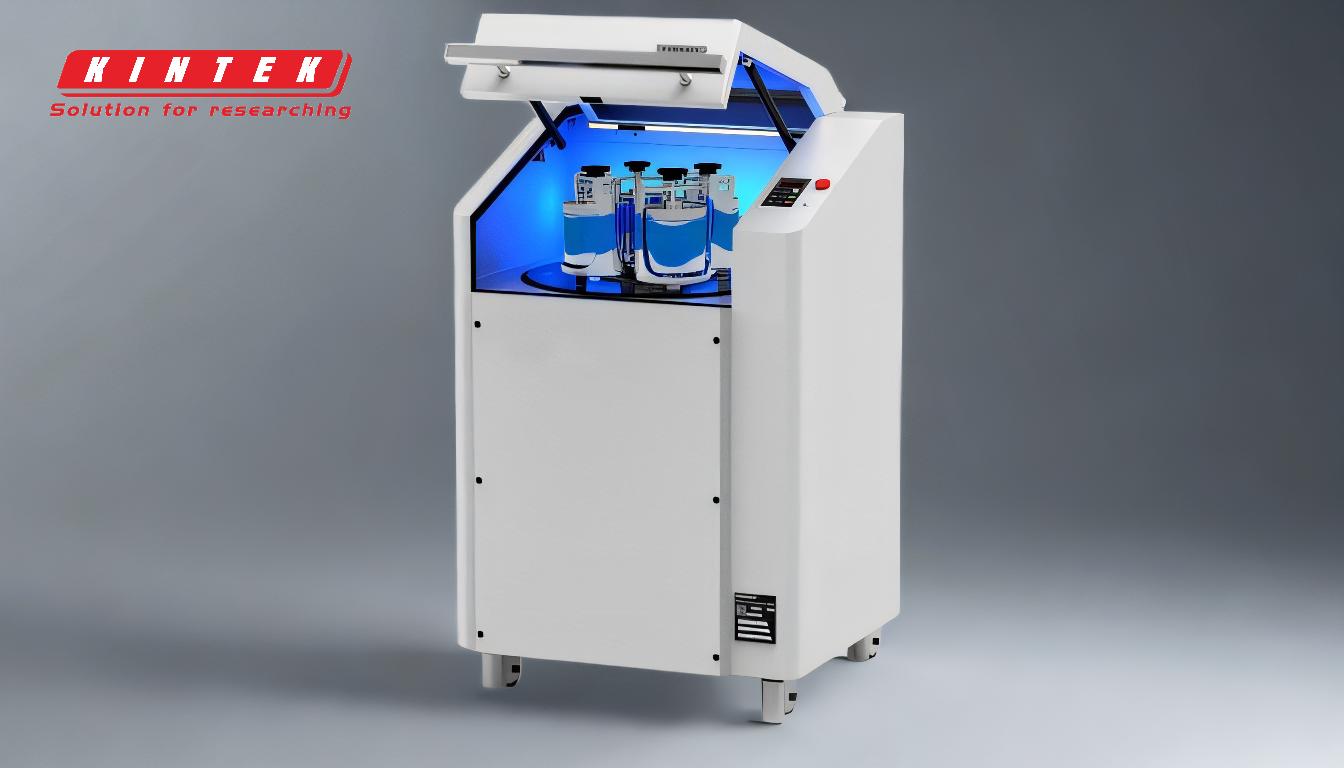
-
Critical Speed and Its Significance:
- Critical speed is the rotational speed at which the grinding balls begin to adhere to the inner walls of the mill due to centrifugal force.
- At this speed, the balls rotate with the mill shell, and no grinding action occurs because the balls are not cascading or impacting the material.
- To achieve effective grinding, the mill must operate slightly below the critical speed, allowing the balls to lift and cascade, creating impact and abrasion on the material.
-
Impact of Low Speed:
- When the rotation speed is too low, the balls slide or roll over one another without sufficient impact or cascading motion.
- This results in minimal size reduction and inefficient grinding, as the energy transfer from the balls to the material is insufficient.
- Low speed is unsuitable for achieving the desired fineness of the ground product.
-
Impact of High Speed:
- At excessively high speeds, centrifugal force causes the balls to stick to the cylinder walls, preventing them from falling and impacting the material.
- This eliminates the grinding action entirely, as the balls no longer cascade or tumble.
- High speed can also lead to increased wear on the mill lining and grinding balls, reducing the lifespan of the equipment.
-
Optimal Speed for Efficient Grinding:
- The optimal speed is typically 65-75% of the critical speed, ensuring that the balls are lifted to a sufficient height before cascading down.
- This creates a balance between impact (due to the falling balls) and abrasion (due to the rolling motion), maximizing size reduction.
- Operating at this speed ensures efficient energy transfer and consistent grinding performance.
-
Factors Influencing the Importance of Rotation Speed:
- Grinding Medium: The size, density, and number of balls affect how they interact with the material at different speeds.
- Material Properties: The hardness and feed size of the material influence the required grinding intensity and, consequently, the optimal speed.
- Mill Design: The diameter and length of the mill, as well as the shape of the armor surface, determine the critical speed and optimal operating range.
- Filling Ratio: The percentage of the mill volume filled with grinding balls affects the motion and impact of the balls, influencing the required speed.
-
Practical Implications for Equipment Purchasers:
- When selecting a ball mill, it is essential to consider the critical speed and ensure the mill can operate within the optimal speed range for the intended application.
- The mill should be designed to allow adjustments in rotation speed to accommodate different materials and grinding requirements.
- Proper maintenance and monitoring of the rotation speed are necessary to ensure consistent grinding performance and prevent equipment damage.
-
Conclusion:
- The speed of rotation of a ball mill cylinder is a fundamental parameter that directly affects the grinding efficiency, particle size reduction, and overall productivity of the mill.
- Understanding the relationship between rotation speed, critical speed, and grinding performance is crucial for optimizing the operation of a ball mill and achieving the desired results.
Summary Table:
Aspect | Details |
---|---|
Critical Speed | Speed at which balls adhere to mill walls due to centrifugal force. |
Low Speed Impact | Balls slide or roll, leading to inefficient grinding and minimal size reduction. |
High Speed Impact | Balls stick to walls, preventing grinding and increasing equipment wear. |
Optimal Speed | 65-75% of critical speed for balanced impact and cascading motion. |
Key Influencing Factors | Grinding medium, material properties, mill design, and filling ratio. |
Ready to optimize your ball mill's performance? Contact our experts today for tailored solutions!