The main difference between a ball mill and a rod mill lies in the type of grinding medium used: ball mills use steel balls, while rod mills use steel rods. This fundamental difference in grinding media leads to variations in their working principles, grinding efficiency, and applications. Ball mills are typically used for finer grinding, while rod mills are better suited for coarser grinding. The choice between the two depends on the desired particle size and the material being processed.
Key Points Explained:
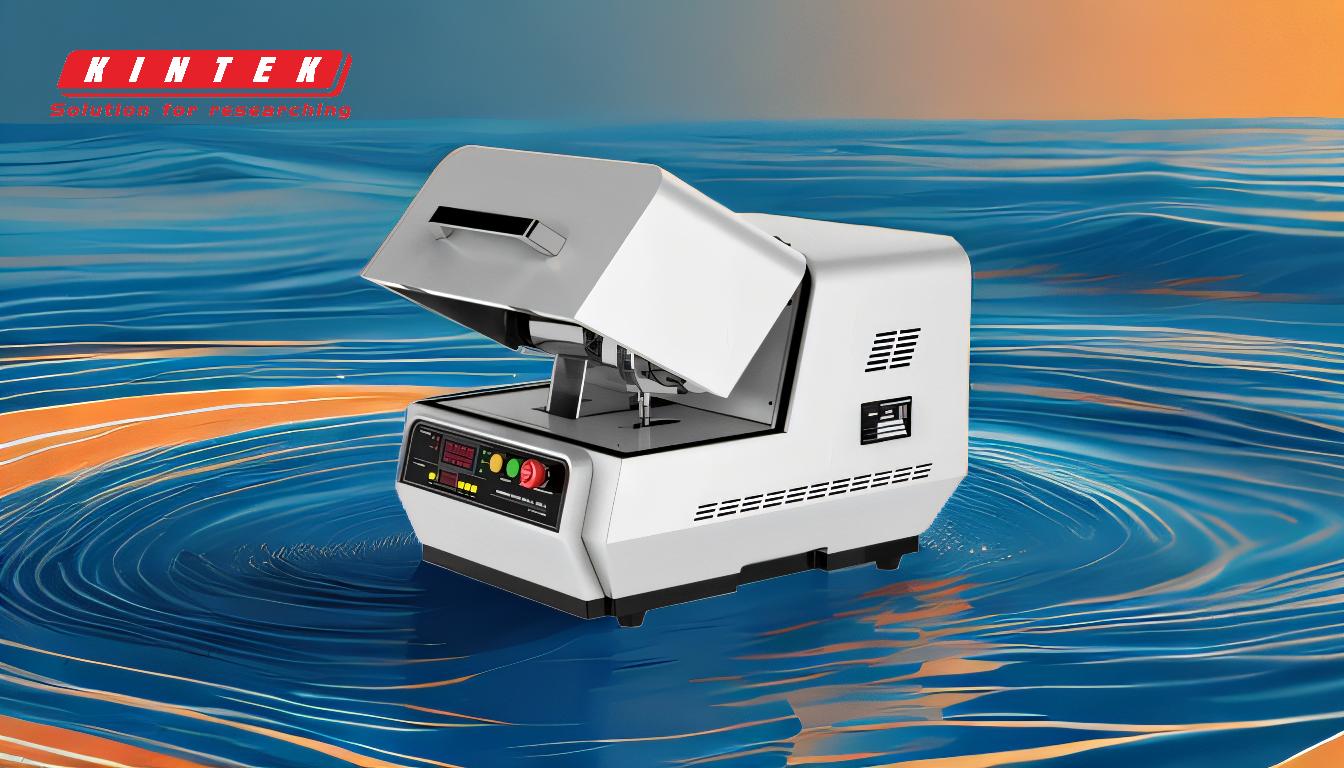
-
Grinding Medium:
- Ball Mill: Uses steel balls as the grinding medium. The balls are typically made of hardened steel and vary in size depending on the application.
- Rod Mill: Uses steel rods as the grinding medium. The rods are usually longer and have a smaller diameter compared to the balls used in ball mills.
-
Working Principle:
- Ball Mill: The steel balls in a ball mill impact and grind the material by tumbling within the mill. The grinding action is primarily due to the impact and attrition between the balls and the material.
- Rod Mill: The steel rods in a rod mill grind the material by rolling and sliding within the mill. The grinding action is more of a line contact, which results in a more uniform particle size distribution.
-
Grinding Efficiency:
- Ball Mill: Generally more efficient for fine grinding. The impact and attrition between the balls and the material result in a finer grind, making ball mills suitable for materials that require a high degree of fineness.
- Rod Mill: More efficient for coarse grinding. The line contact between the rods and the material results in a coarser grind, making rod mills suitable for materials that do not require a high degree of fineness.
-
Applications:
- Ball Mill: Commonly used in the mining industry for grinding ores, as well as in the chemical, pharmaceutical, and cement industries for fine grinding of materials.
- Rod Mill: Often used in the mining industry for grinding ores, particularly in the preparation of feed for ball mills or for grinding materials that do not require a high degree of fineness.
-
Particle Size Distribution:
- Ball Mill: Produces a finer and more uniform particle size distribution due to the impact and attrition grinding action.
- Rod Mill: Produces a coarser and less uniform particle size distribution due to the line contact grinding action.
-
Maintenance and Wear:
- Ball Mill: The steel balls are subject to wear and need to be replaced periodically. The wear rate depends on the hardness of the material being ground and the size of the balls.
- Rod Mill: The steel rods are also subject to wear, but the wear rate is generally lower compared to balls. The rods need to be replaced less frequently, which can result in lower maintenance costs.
-
Energy Consumption:
- Ball Mill: Typically consumes more energy due to the higher impact forces and the need to achieve finer grinding.
- Rod Mill: Generally consumes less energy, especially for coarse grinding applications, due to the more efficient line contact grinding action.
In summary, the choice between a ball mill and a rod mill depends on the specific requirements of the grinding process, including the desired particle size, the type of material being ground, and the energy efficiency considerations. Ball mills are preferred for fine grinding, while rod mills are more suitable for coarse grinding.
Summary Table:
Feature | Ball Mill | Rod Mill |
---|---|---|
Grinding Medium | Steel balls | Steel rods |
Working Principle | Impact and attrition grinding | Line contact grinding |
Grinding Efficiency | More efficient for fine grinding | More efficient for coarse grinding |
Applications | Mining, chemical, pharmaceutical, cement industries (fine grinding) | Mining (coarse grinding, feed preparation) |
Particle Size | Finer and more uniform | Coarser and less uniform |
Maintenance | Higher wear rate; balls need frequent replacement | Lower wear rate; rods need less frequent replacement |
Energy Consumption | Higher energy consumption | Lower energy consumption |
Need help choosing the right mill for your application? Contact our experts today for personalized advice!