Roller mixers are laboratory instruments designed to mix samples in tubes or bottles by gently rolling them between motor-driven rollers. These rollers rotate at a fixed speed, ensuring consistent mixing. The unique feature of roller mixers is the combination of rolling and tilting actions, where the rollers are gently raised and lowered at one end. This motion ensures thorough mixing of the samples without causing excessive shear forces, making them ideal for sensitive biological or chemical samples. The principle revolves around gentle agitation, which prevents sample degradation while promoting uniform mixing.
Key Points Explained:
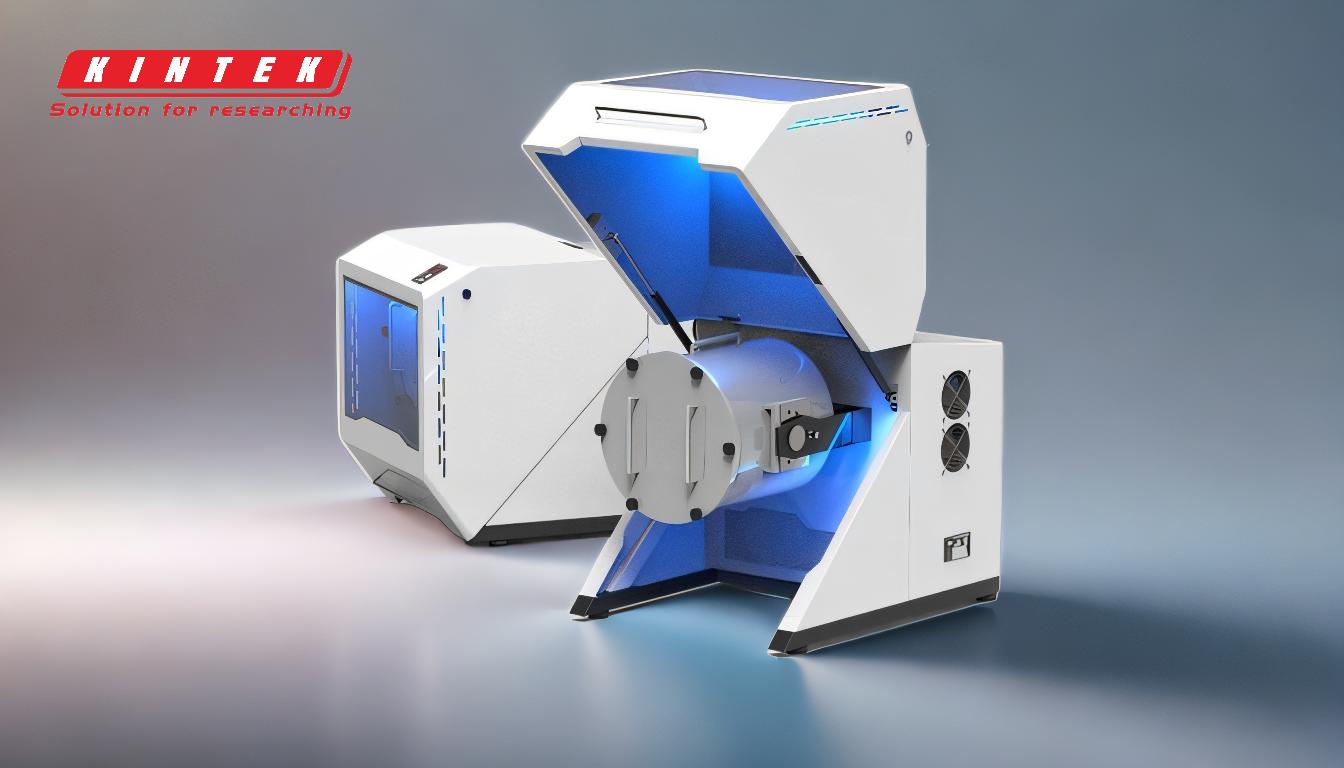
-
Motor-Driven Rollers:
- Roller mixers are equipped with motor-driven rollers that rotate at a fixed speed. This ensures consistent and controlled movement of the samples.
- The motor provides the necessary power to rotate the rollers, allowing for continuous operation over extended periods.
-
Sample Placement:
- Samples are placed in tubes or bottles, which are then positioned between the rollers. This setup allows the containers to be gently rolled, ensuring even mixing.
- The design accommodates various tube sizes, making roller mixers versatile for different laboratory applications.
-
Rolling Action:
- The primary mixing action is achieved through the rolling motion of the tubes or bottles between the rollers. This motion ensures that the contents are continuously agitated, promoting uniform mixing.
- The rolling action is gentle, which is particularly important for sensitive samples that may be damaged by more aggressive mixing methods.
-
Tilting Action:
- In addition to the rolling motion, roller mixers apply a tilting action. This is achieved by gently raising and lowering one end of the rollers.
- The tilting action enhances the mixing process by ensuring that the sample is agitated in multiple directions, preventing sedimentation and promoting homogeneity.
-
Gentle Agitation:
- The combination of rolling and tilting actions provides gentle agitation, which is crucial for samples that are sensitive to shear forces.
- This gentle mixing method is ideal for applications such as cell culture, protein purification, and other biological processes where maintaining sample integrity is critical.
-
Applications:
- Roller mixers are widely used in laboratories for mixing biological samples, such as cell cultures, blood samples, and reagents.
- They are also used in chemical laboratories for mixing solutions, suspensions, and other liquid samples.
-
Advantages:
- Consistency: The fixed speed of the rollers ensures consistent mixing results.
- Versatility: Accommodates various tube sizes and types, making it suitable for a wide range of applications.
- Gentle Mixing: Protects sensitive samples from damage due to excessive shear forces.
- Ease of Use: Simple operation with minimal setup required.
-
Considerations for Purchasers:
- Speed Control: Ensure the roller mixer has adjustable speed settings to accommodate different types of samples.
- Roller Capacity: Consider the number and size of rollers to match the volume and type of samples you typically handle.
- Tilting Mechanism: Verify that the tilting action is smooth and adjustable to optimize mixing for your specific needs.
- Durability: Look for robust construction materials to ensure long-term reliability and performance.
In summary, the principle of roller mixers revolves around the gentle and consistent mixing of samples through a combination of rolling and tilting actions. This method is particularly beneficial for sensitive biological and chemical samples, ensuring thorough mixing without compromising sample integrity. When selecting a roller mixer, consider factors such as speed control, roller capacity, and the quality of the tilting mechanism to ensure it meets your laboratory's specific requirements.
Summary Table:
Feature | Description |
---|---|
Motor-Driven Rollers | Rotate at a fixed speed for consistent and controlled sample movement. |
Sample Placement | Tubes or bottles are placed between rollers, accommodating various sizes. |
Rolling Action | Gentle rolling ensures uniform mixing without excessive shear forces. |
Tilting Action | Raises and lowers one end of rollers to enhance mixing in multiple directions. |
Gentle Agitation | Protects sensitive samples from degradation while promoting homogeneity. |
Applications | Ideal for cell cultures, blood samples, reagents, and chemical solutions. |
Advantages | Consistency, versatility, gentle mixing, and ease of use. |
Purchasing Tips | Consider speed control, roller capacity, tilting mechanism, and durability. |
Ready to enhance your lab's mixing process? Contact us today to find the perfect laboratory vortex mixer for your needs!