Sputter coating is a process used to deposit thin films of material onto a substrate, typically for applications in microscopy, electronics, or optics. The principle revolves around using a plasma to eject atoms from a solid target material, which then deposit onto a substrate to form a thin, uniform layer. This process occurs in a vacuum environment and involves the ionization of argon gas to create a plasma. The positively charged argon ions are accelerated toward the negatively charged target material, causing atoms from the target to be ejected and deposited onto the substrate. The process is highly controlled, often automated, and requires precise management of heat and energy to ensure uniform and high-quality coatings.
Key Points Explained:
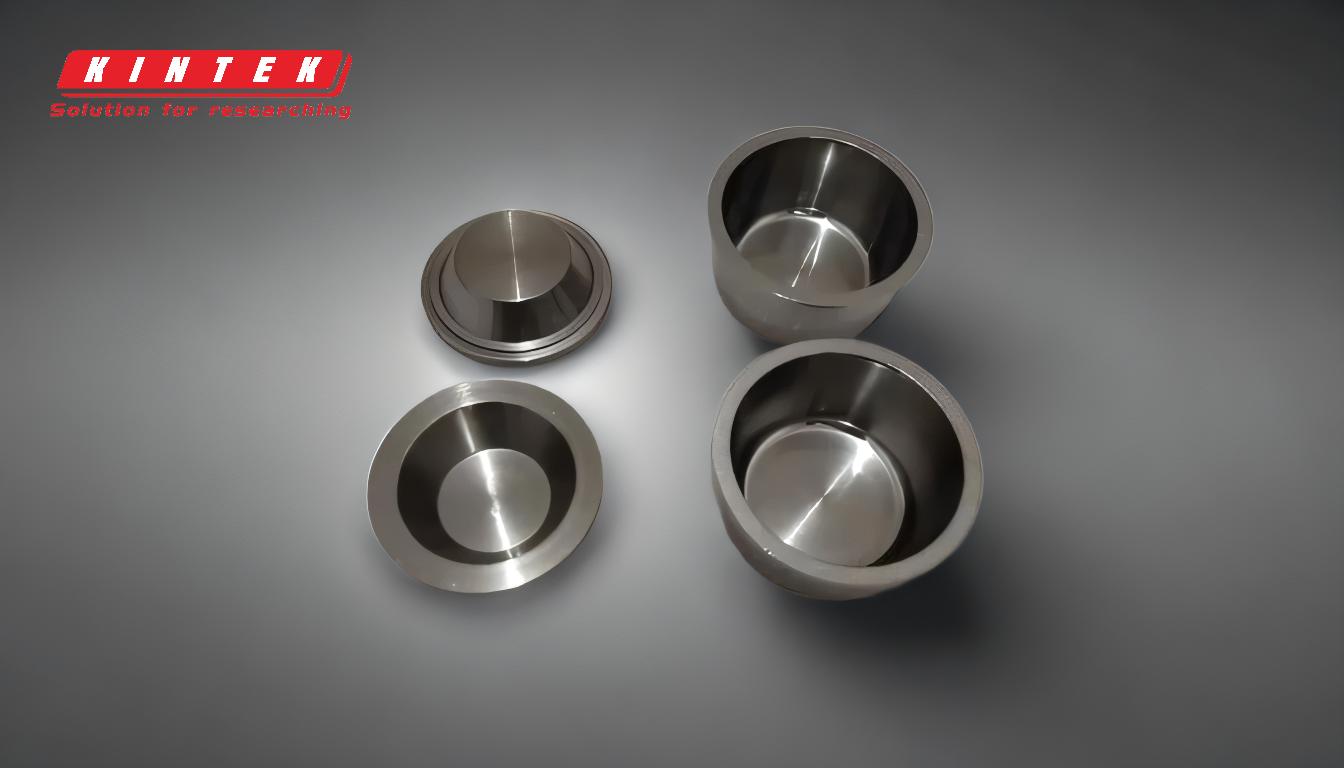
-
Vacuum Environment and Plasma Generation:
- Sputter coating takes place in a vacuum chamber to eliminate contaminants and ensure a controlled environment.
- Argon gas is introduced into the chamber and ionized using a high-voltage electric field, creating a plasma. This plasma consists of positively charged argon ions and free electrons.
-
Target Material and Cathode Setup:
- The target material, which is the substance to be deposited, is bonded or clamped to a negatively charged electrode called the cathode.
- Magnets are often used to stabilize the plasma and ensure uniform erosion of the target material, enhancing the consistency of the coating.
-
Momentum Transfer and Ejection of Target Atoms:
- The positively charged argon ions in the plasma are accelerated toward the negatively charged target material due to the electric field.
- When these high-energy ions strike the target surface, they transfer their momentum to the target atoms, causing them to be ejected from the surface in a process called sputtering.
-
Deposition onto the Substrate:
- The ejected target atoms travel through the vacuum and deposit onto the substrate, forming a thin film.
- The substrate is typically positioned opposite the target material to ensure even deposition.
-
Heat Management:
- Sputter coating generates significant heat due to the high-energy collisions and plasma activity.
- Specialized chilling systems are used to manage this heat, preventing damage to the target material, substrate, and equipment.
-
Automation and Precision:
- The process is often automated to ensure consistent and accurate coatings, reducing variability that can arise from manual operation.
- Precise control of parameters such as voltage, gas pressure, and target-substrate distance is critical for achieving high-quality coatings.
-
Applications and Advantages:
- Sputter coating is widely used in industries requiring thin, uniform films, such as semiconductor manufacturing, optical coatings, and microscopy sample preparation.
- The process produces strong atomic-level bonds between the deposited material and the substrate, ensuring durability and adhesion.
By understanding these key principles, one can appreciate the complexity and precision involved in sputter coating, making it a valuable technique for creating high-performance thin films in various applications.
Summary Table:
Key Aspect | Details |
---|---|
Vacuum Environment | Eliminates contaminants; ensures controlled conditions for uniform coatings. |
Plasma Generation | Argon gas ionized to create plasma; accelerates ions toward the target. |
Target Material | Bonded to a cathode; magnets stabilize plasma for consistent erosion. |
Momentum Transfer | High-energy ions eject target atoms, which deposit onto the substrate. |
Heat Management | Chilling systems prevent damage from high-energy collisions. |
Automation & Precision | Automated systems ensure consistent coatings with precise parameter control. |
Applications | Used in microscopy, semiconductors, and optics for durable, uniform films. |
Discover how sputter coating can enhance your applications—contact our experts today!