The wiped film molecular still operates on the principle of thermal separation, utilizing a mechanically generated thin film of liquid to enhance heat transfer and separation efficiency. The process involves feeding the feedstock into a heated vertical cylinder, where rotating wipers or rollers create a thin, turbulent film on the heated surface. This thin film allows volatile components to evaporate quickly under vacuum conditions, while the vapors are condensed in a centrally located condenser. The condensed distillate and high-temperature residue are collected separately, ensuring efficient separation of components with minimal thermal degradation. The process is highly adaptable, operating in both batch and continuous modes, and is optimized by controlling parameters such as temperature, vacuum, and feed rate.
Key Points Explained:
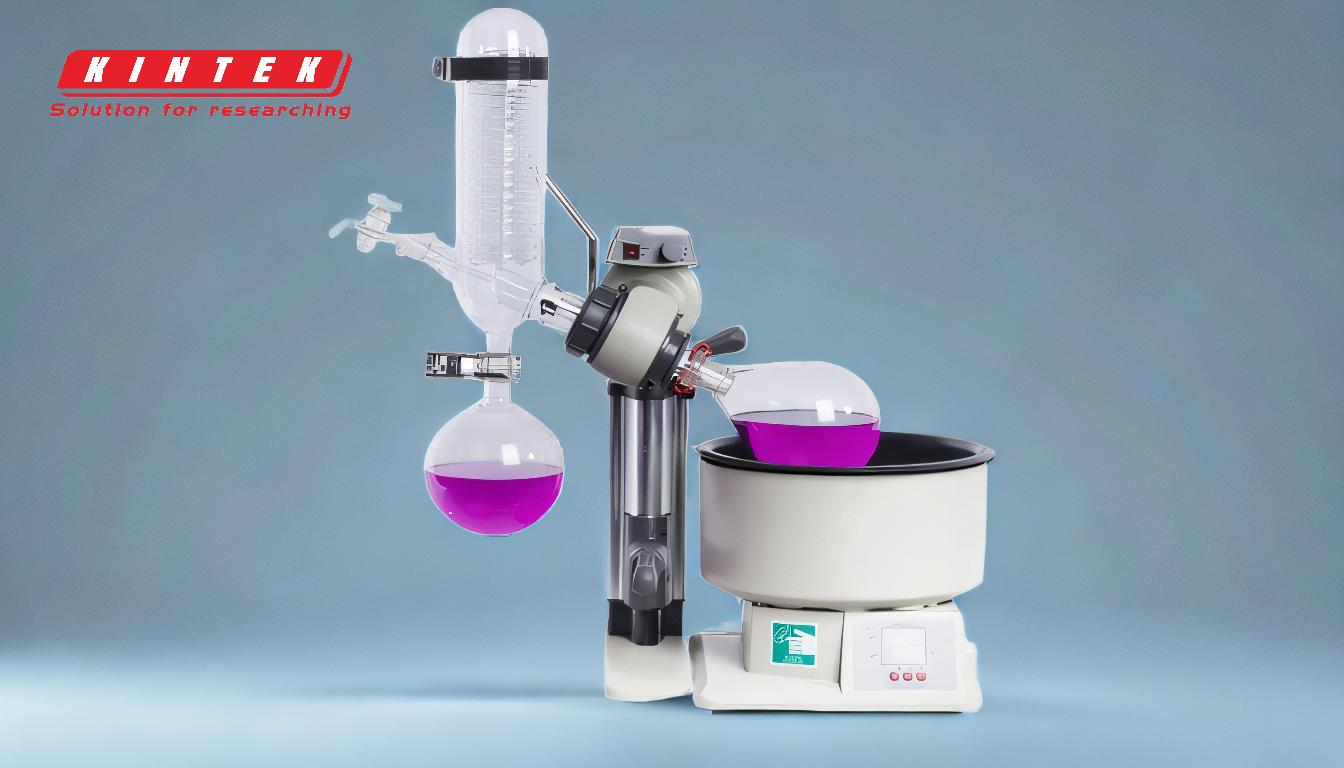
-
Thin Film Formation:
- The wiped film molecular still creates a thin, uniform film of the feedstock on the heated surface of the evaporator. This is achieved using rotating wipers or rollers that spread the liquid evenly. The thin film maximizes the surface area for heat transfer, allowing for rapid evaporation of volatile components.
-
Thermal Separation:
- The process relies on thermal separation, where the thin film of liquid is exposed to heat, causing the more volatile components to evaporate. The non-volatile components remain in the liquid phase and are collected as residue. The use of vacuum conditions lowers the boiling points of the components, reducing the risk of thermal degradation.
-
Vacuum Operation:
- Operating under vacuum is crucial for the wiped film molecular still. It reduces the boiling points of the components, allowing for separation at lower temperatures. This minimizes thermal stress on the compounds, preserving their integrity and preventing decomposition.
-
Condensation:
- The vapors generated from the evaporation process are condensed in a centrally located condenser. The condenser is cooled using a recirculating fluid, which ensures efficient condensation of the vapors into a liquid distillate. The distillate is then collected in separate receiving vessels.
-
Batch and Continuous Modes:
- The wiped film molecular still can operate in both batch and continuous modes. In batch mode, a specific quantity of feedstock is processed at a time, while in continuous mode, the feedstock is continuously fed into the system. This flexibility allows for scalability and adaptability to different production needs.
-
Optimization of Parameters:
- The efficiency of the wiped film molecular still depends on the optimization of several parameters, including temperature, vacuum level, and feed rate. Careful control of these parameters ensures optimal separation of components and maximizes the yield of the desired product.
-
Reduced Thermal Degradation:
- The short exposure time of the feedstock to heat, combined with the low operating temperatures under vacuum, significantly reduces the risk of thermal degradation. This is particularly important for heat-sensitive compounds, such as cannabinoids and terpenes, which can degrade at high temperatures.
-
High Separation Efficiency:
- The combination of a thin film, vacuum operation, and efficient condensation results in high separation efficiency. The process effectively separates components based on their volatility, producing a high-purity distillate with minimal contamination from non-volatile residues.
-
Mechanical Agitation:
- The rotating wipers or rollers not only create the thin film but also provide mechanical agitation. This agitation enhances mass transfer and prevents the formation of hot spots, ensuring uniform heating and evaporation of the feedstock.
-
Scalability and Versatility:
- The wiped film molecular still is highly scalable and versatile, making it suitable for a wide range of applications, from small-scale laboratory research to large-scale industrial production. Its ability to handle various feedstocks and produce high-quality distillates makes it a valuable tool in industries such as pharmaceuticals, food, and cannabis extraction.
In summary, the wiped film molecular still is a sophisticated distillation system that leverages the principles of thin film formation, thermal separation, and vacuum operation to achieve efficient and high-quality separation of volatile components. Its design and operational flexibility make it an essential tool for industries requiring precise and gentle separation processes.
Summary Table:
Key Feature | Description |
---|---|
Thin Film Formation | Rotating wipers create a uniform thin film for rapid evaporation. |
Thermal Separation | Volatile components evaporate under heat, while non-volatiles remain as residue. |
Vacuum Operation | Lowers boiling points, reducing thermal degradation. |
Condensation | Vapors are condensed into high-purity distillate. |
Batch & Continuous Modes | Flexible operation for scalability and adaptability. |
Parameter Optimization | Temperature, vacuum, and feed rate are controlled for efficiency. |
Reduced Thermal Degradation | Short heat exposure and low temperatures preserve heat-sensitive compounds. |
High Separation Efficiency | Produces pure distillate with minimal contamination. |
Mechanical Agitation | Enhances mass transfer and prevents hot spots. |
Scalability & Versatility | Suitable for lab research to industrial production. |
Discover how a wiped film molecular still can revolutionize your separation process—contact our experts today!