The sputtering process primarily uses inert gases, with argon being the most common due to its availability, cost-effectiveness, and suitable atomic weight for efficient momentum transfer. For specific applications, other inert gases like neon, krypton, or xenon are used depending on the atomic weight of the target material. Reactive gases such as oxygen, nitrogen, or acetylene are also employed in reactive sputtering to deposit thin films of compounds like oxides, nitrides, or carbides. The choice of gas depends on the desired film properties and the target material's characteristics.
Key Points Explained:
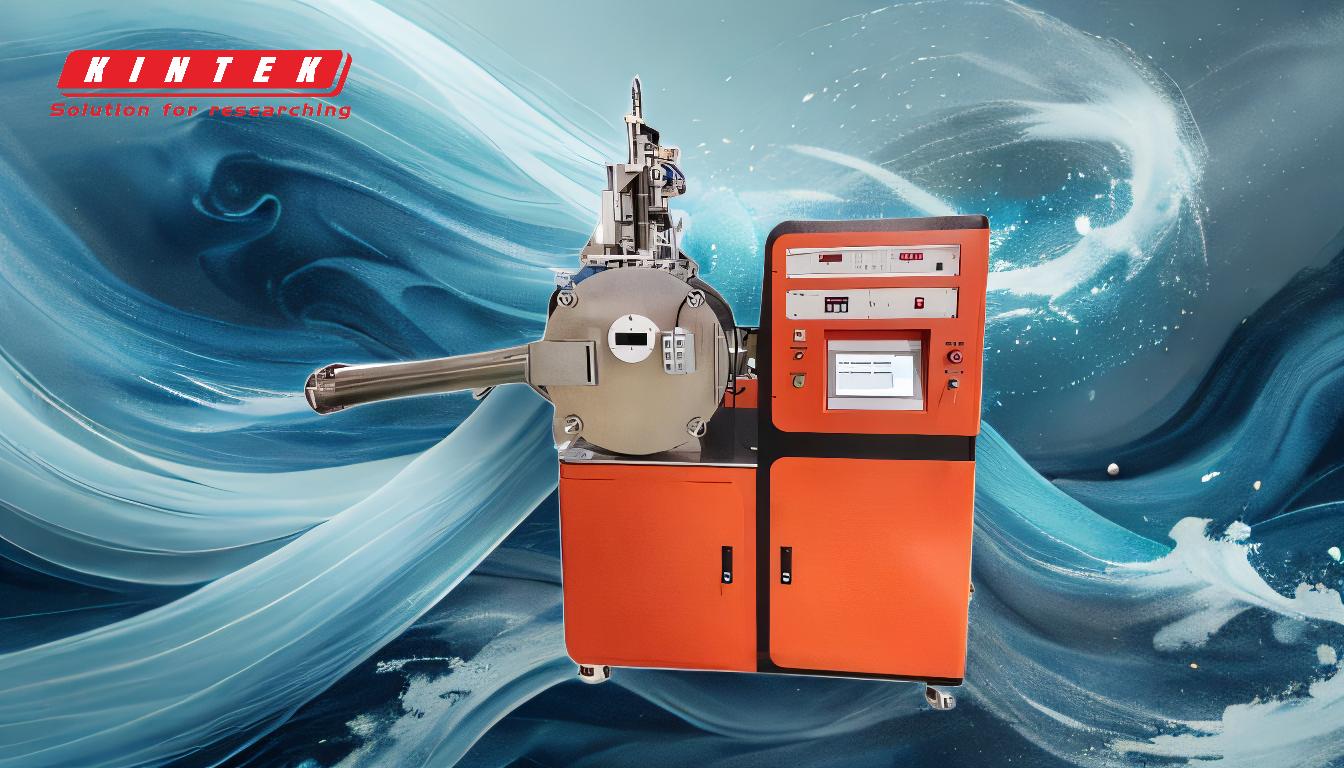
-
Primary Use of Inert Gases:
- Argon (Ar): The most commonly used gas in sputtering due to its inert nature, availability, and cost-effectiveness. Its atomic weight (40) is suitable for efficient momentum transfer with many target materials.
- Neon (Ne): Used for sputtering light elements due to its low atomic weight (20), which matches well with lighter target materials.
- Krypton (Kr) and Xenon (Xe): Employed for sputtering heavy elements because their higher atomic weights (84 and 131, respectively) provide better momentum transfer for heavier target materials.
-
Reactive Gases in Sputtering:
- Oxygen (O₂): Used in reactive sputtering to deposit oxide films. The oxygen reacts with the sputtered material to form oxides on the substrate.
- Nitrogen (N₂): Utilized to create nitride films. Nitrogen reacts with the target material to form nitrides during the deposition process.
- Acetylene (C₂H₂): Employed to deposit carbide films. The carbon from acetylene reacts with the target material to form carbides.
-
Factors Influencing Gas Selection:
- Atomic Weight Matching: The atomic weight of the sputtering gas should be close to that of the target material for efficient momentum transfer. This ensures effective sputtering of the target atoms.
- Chemical Reactivity: Inert gases like argon are chosen for their non-reactive nature, which prevents unwanted chemical reactions with the target material. Reactive gases, on the other hand, are selected to facilitate the formation of specific compounds (e.g., oxides, nitrides) on the substrate.
- Process Parameters: The choice of gas can also depend on process parameters such as pressure, temperature, and the desired film properties.
-
Applications of Reactive Sputtering:
- Oxide Films: Reactive sputtering with oxygen is used to deposit thin films of oxides, which are essential in applications like transparent conductive coatings, dielectric layers, and optical coatings.
- Nitride Films: Nitrogen is used to deposit nitride films, which are important for hard coatings, wear-resistant layers, and semiconductor applications.
- Carbide Films: Acetylene is used to deposit carbide films, which are valued for their hardness and wear resistance in tool coatings and protective layers.
-
Advantages of Using Inert Gases:
- Chemical Stability: Inert gases do not react with the target material, ensuring a pure deposition process.
- Controlled Deposition: The use of inert gases allows for precise control over the deposition process, leading to consistent film quality.
- Versatility: Inert gases can be used with a wide range of target materials, making them suitable for various applications.
-
Advantages of Reactive Sputtering:
- Compound Formation: Reactive sputtering enables the deposition of compound films (e.g., oxides, nitrides) directly, which can be challenging to achieve with pure inert gases.
- Tailored Film Properties: By selecting the appropriate reactive gas, the properties of the deposited film (e.g., electrical, optical, mechanical) can be tailored to specific application requirements.
- Enhanced Adhesion: Reactive sputtering can improve the adhesion of the deposited film to the substrate, which is crucial for durable coatings.
In summary, the choice of process gas in sputtering depends on the target material, the desired film properties, and the specific application. Inert gases like argon are the standard choice due to their stability and efficiency, while reactive gases are used when compound films are required. Understanding the role of these gases helps in optimizing the sputtering process for various industrial and research applications.
Summary Table:
Gas Type | Common Gases | Key Applications |
---|---|---|
Inert Gases | Argon (Ar), Neon (Ne), Krypton (Kr), Xenon (Xe) | Efficient momentum transfer, stable deposition, versatile for various target materials. |
Reactive Gases | Oxygen (O₂), Nitrogen (N₂), Acetylene (C₂H₂) | Deposits oxide, nitride, and carbide films for tailored film properties. |
Need help selecting the right gas for your sputtering process? Contact our experts today for tailored solutions!