Cathode sputtering is a thin film deposition process where a solid target material is bombarded by high-energy ions, typically argon ions, in a vacuum chamber. The ions are generated by a plasma discharge, and the target acts as the cathode (negatively charged), while the substrate serves as the anode (positively charged). The ions collide with the target, ejecting atoms that then deposit onto the substrate, forming a thin film. This process is widely used for metallic targets but faces challenges with non-conductive materials due to charge buildup. Key steps include creating a vacuum, introducing inert gas, ionizing the gas, and applying a high voltage to accelerate ions toward the target.
Key Points Explained:
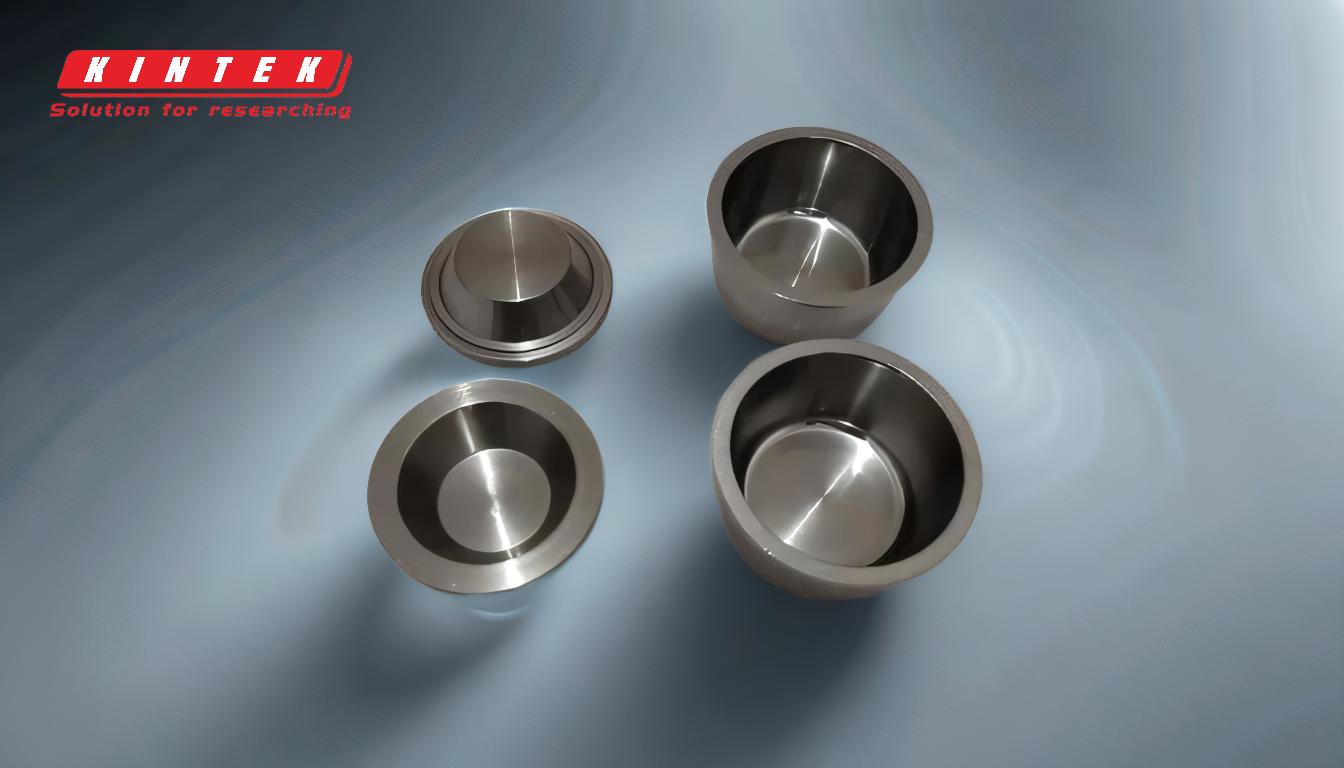
-
Creation of a Vacuum Environment
- The process begins by evacuating the reaction chamber to a low pressure of around 1 Pa (0.0000145 psi).
- This step removes moisture and impurities, ensuring a clean environment for deposition.
- A vacuum is essential to minimize contamination and allow the inert gas to ionize effectively.
-
Introduction of Inert Gas
- An inert gas, typically argon, is pumped into the chamber to create a low-pressure atmosphere.
- Argon is chosen because it is chemically inert and readily ionizes under the applied electric field.
- The gas density is controlled to optimize the plasma formation and ion generation.
-
Ionization and Plasma Formation
- A high voltage (3-5 kV) is applied to ionize the argon gas, creating a plasma.
- The plasma consists of argon atoms, argon ions (Ar+), and free electrons.
- Electrons collide with argon atoms, continuously generating positively charged ions.
-
Acceleration of Ions Toward the Target
- The target material, acting as the cathode, is negatively charged (several hundred volts).
- Positively charged argon ions are accelerated toward the target due to the electric field.
- The high-energy ions bombard the target, transferring kinetic energy to the target atoms.
-
Sputtering of Target Material
- The energy from the ion collisions ejects atoms from the target material.
- These ejected atoms are in a gaseous or plasma state and carry kinetic energy.
- The process is called "sputtering" because the target material is physically removed atom by atom.
-
Transport and Deposition of Sputtered Atoms
- The ejected atoms travel through the low-pressure environment toward the substrate.
- The substrate, acting as the anode, is positioned to receive the sputtered material.
- The atoms condense on the substrate, forming a thin, uniform film.
-
Magnetic Field Enhancement (Magnetron Sputtering)
- In magnetron sputtering, magnet arrays are used to create a magnetic field near the target.
- The magnetic field traps electrons, increasing the ionization efficiency of the argon gas.
- This enhances the sputtering rate and improves the uniformity of the deposited film.
-
Challenges with Non-Conductive Materials
- Non-conductive targets can accumulate positive charge during sputtering.
- This charge buildup repels incoming ions, reducing the sputtering efficiency.
- Techniques like RF (radio frequency) sputtering are often used for non-conductive materials to mitigate this issue.
-
Applications and Advantages
- Cathode sputtering is widely used in industries such as semiconductors, optics, and coatings.
- It allows for the deposition of ultra-high-purity films with precise control over thickness and composition.
- The process is suitable for a wide range of materials, including metals, alloys, and some ceramics.
-
Process Parameters and Optimization
- Key parameters include gas pressure, voltage, target material, and substrate temperature.
- Substrate heating (150–750°C) is often used to improve film adhesion and quality.
- Optimization of these parameters is critical to achieving the desired film properties.
By understanding these steps and principles, one can effectively utilize cathode sputtering for various thin film deposition applications, ensuring high-quality and consistent results.
Summary Table:
Step | Description |
---|---|
1. Creation of Vacuum | Evacuate chamber to ~1 Pa to remove impurities and ensure a clean environment. |
2. Introduction of Inert Gas | Pump argon gas into the chamber to create a low-pressure atmosphere. |
3. Ionization & Plasma | Apply high voltage (3-5 kV) to ionize argon gas and form a plasma. |
4. Ion Acceleration | Accelerate ions toward the negatively charged target. |
5. Sputtering of Target | Eject target atoms through ion collisions. |
6. Transport & Deposition | Sputtered atoms condense on the substrate, forming a thin film. |
7. Magnetic Field Enhancement | Use magnet arrays to improve ionization and sputtering rates (magnetron). |
8. Non-Conductive Challenges | Address charge buildup in non-conductive materials using RF sputtering. |
9. Applications | Used in semiconductors, optics, and coatings for precise thin film deposition. |
10. Process Optimization | Optimize gas pressure, voltage, and substrate temperature for best results. |
Ready to optimize your thin film deposition process? Contact our experts today for tailored solutions!