DC sputtering is a widely used physical vapor deposition (PVD) technique for creating thin films on substrates. It involves creating a vacuum in a chamber, introducing an inert gas (usually argon), and applying a voltage to generate plasma. The plasma ionizes the gas, and the resulting ions bombard a target material, ejecting atoms from the target. These ejected atoms then travel through the chamber and deposit onto a substrate, forming a thin film. The process is highly controlled, ensuring uniform deposition, and is commonly used in industries like semiconductors, jewelry, and optics due to its simplicity and cost-effectiveness.
Key Points Explained:
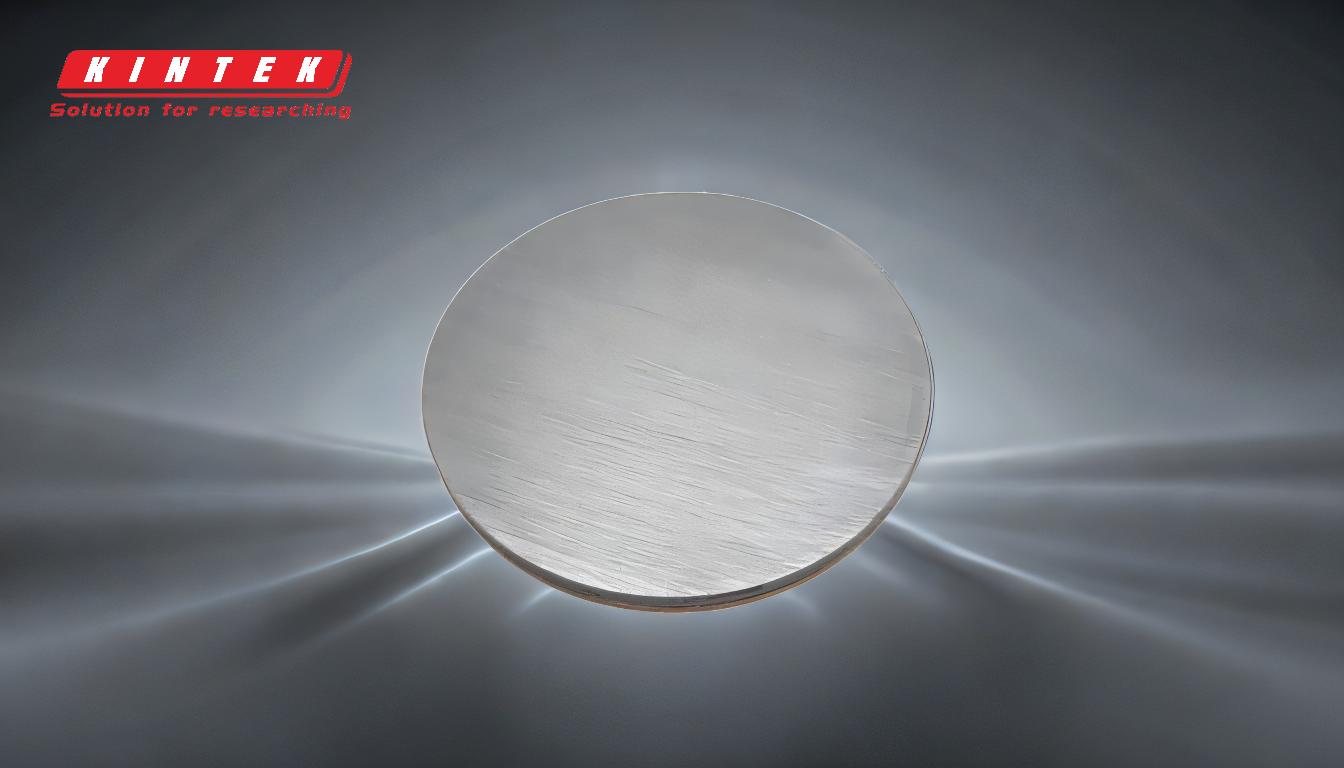
-
Vacuum Creation in the Chamber
- The process begins by evacuating the chamber to create a vacuum. This step is crucial because it removes contaminants and ensures a controlled environment for the deposition process.
- A vacuum minimizes unwanted reactions and allows for precise control over the deposition conditions, which is essential for achieving uniform thin films.
-
Introduction of Inert Gas
- After achieving a vacuum, an inert gas, typically argon, is introduced into the chamber at low pressure. Argon is preferred because it is chemically inert, reducing the risk of unwanted reactions during the process.
- The low-pressure environment ensures that the gas atoms can be easily ionized in the next step.
-
Plasma Generation and Gas Ionization
- A voltage is applied across the chamber, creating an electric field that ionizes the argon gas atoms. This ionization generates plasma, a state of matter consisting of free electrons and ions.
- The plasma contains positively charged argon ions, which are accelerated toward the negatively charged target material due to the electric field.
-
Sputtering of the Target Material
- The accelerated argon ions collide with the target material, transferring their kinetic energy to the target atoms. This energy transfer causes atoms to be ejected (or sputtered) from the target surface.
- The sputtered atoms are neutral and carry kinetic energy as they travel through the chamber.
-
Transport and Deposition of Sputtered Atoms
- The ejected atoms travel through the low-pressure environment and deposit onto the substrate. The substrate is typically positioned opposite the target to ensure uniform coating.
- As the atoms condense on the substrate, they form a thin film. The thickness and quality of the film depend on factors such as the sputtering rate, substrate temperature, and chamber conditions.
-
Applications of DC Sputtering
- DC sputtering is widely used in industries requiring precise and uniform thin-film coatings. Common applications include:
- Semiconductors: For depositing conductive and insulating layers.
- Optical Components: For creating anti-reflective or reflective coatings.
- Jewelry: For applying decorative or protective coatings.
- Its simplicity and cost-effectiveness make it a popular choice for metal deposition in various fields.
- DC sputtering is widely used in industries requiring precise and uniform thin-film coatings. Common applications include:
-
Advantages of DC Sputtering
- Simplicity: The process is straightforward and easy to control, making it suitable for a wide range of applications.
- Cost-Effectiveness: It is one of the most economical PVD techniques, especially for metal deposition.
- Uniformity: The process ensures uniform thin-film deposition, which is critical for applications requiring precise coatings.
-
Limitations of DC Sputtering
- Material Limitations: DC sputtering is primarily suitable for conductive materials. Insulating materials require alternative techniques like RF sputtering.
- Deposition Rate: The deposition rate can be slower compared to other PVD methods, depending on the target material and process conditions.
- Heat Generation: The process can generate heat, which may affect temperature-sensitive substrates.
By following these steps, DC sputtering provides a reliable and efficient method for depositing thin films, making it a cornerstone of modern thin-film technology.
Summary Table:
Aspect | Details |
---|---|
Process | Creates thin films by bombarding a target material with ionized gas atoms. |
Key Steps | Vacuum creation, inert gas introduction, plasma generation, sputtering. |
Applications | Semiconductors, optical components, jewelry coatings. |
Advantages | Simplicity, cost-effectiveness, uniform deposition. |
Limitations | Limited to conductive materials, slower deposition rate, heat generation. |
Discover how DC sputtering can enhance your thin-film processes—contact our experts today!