Ion beam sputtering (IBS) is a highly precise and controlled thin-film deposition technique used to create dense, high-quality films on substrates. The process involves generating a focused, monoenergetic ion beam that bombards a target material, causing atoms to be ejected and deposited onto a substrate. This method is performed in a vacuum chamber filled with inert gas atoms, where the ions are directed at the target with high energy and directionality. The sputtered atoms are transported through a reduced-pressure region and condense on the substrate, forming a thin film. IBS is known for its ability to produce films with exceptional uniformity, density, and adhesion, making it a preferred method for applications requiring high precision and performance.
Key Points Explained:
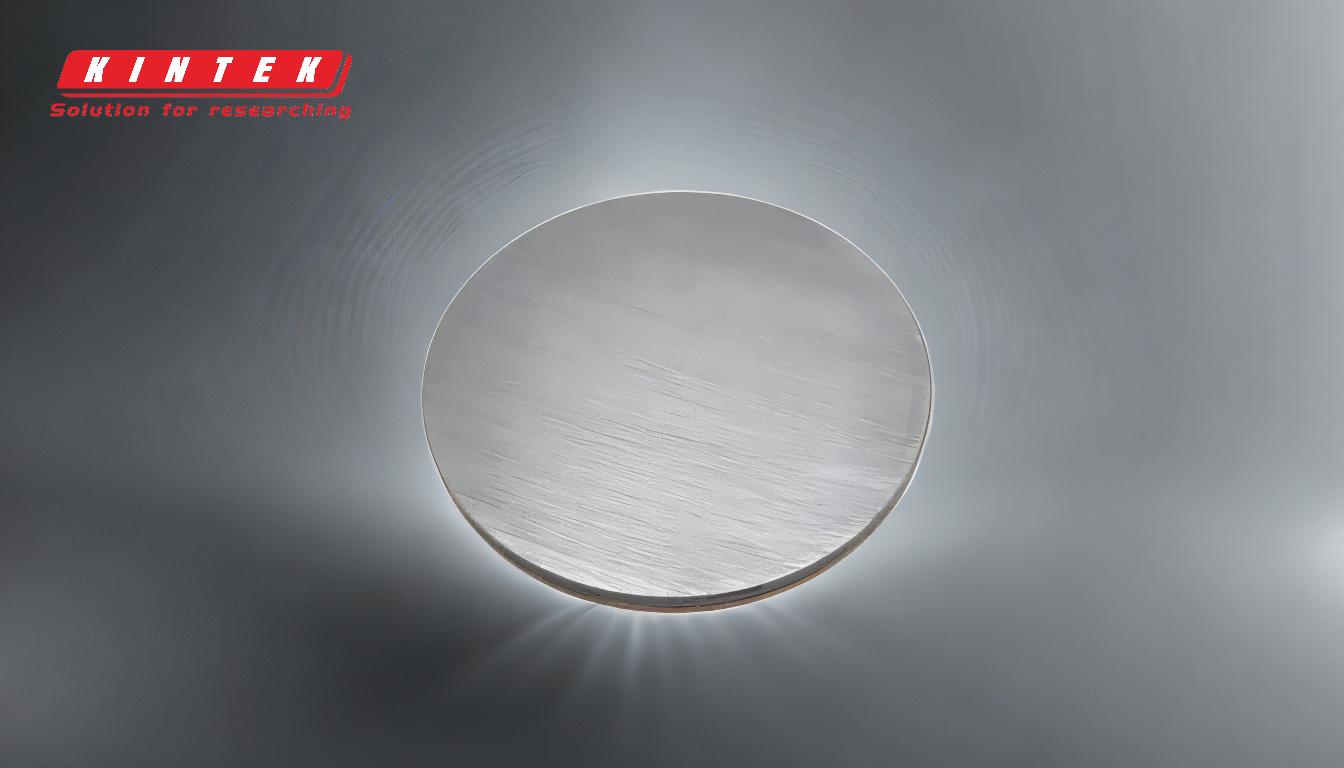
-
Generation of Ions:
- The process begins in a vacuum chamber filled with inert gas atoms, such as argon.
- A high electric field is applied to ionize the gas atoms, creating positively charged ions.
- These ions are then accelerated toward the target material due to the electric field.
-
Focusing and Collimation of the Ion Beam:
- The ion beam is highly focused and collimated, meaning the ions have equal energy and directionality.
- This ensures that the ions strike the target material with precision, leading to uniform sputtering.
-
Sputtering of the Target Material:
- The accelerated ions collide with the target material, transferring their energy to the target atoms.
- This energy transfer causes the target atoms to be ejected from the surface in a process known as sputtering.
- The sputtered atoms are typically ejected in the form of atomic-sized particles.
-
Transport of Sputtered Atoms:
- The sputtered atoms are transported through a region of reduced pressure (the vacuum chamber) toward the substrate.
- The vacuum environment minimizes collisions between the sputtered atoms and other particles, ensuring a clean and controlled deposition process.
-
Deposition on the Substrate:
- The sputtered atoms condense on the substrate, forming a thin film.
- The high energy and directionality of the ion beam result in a dense, uniform film with excellent adhesion to the substrate.
-
Advantages of Ion Beam Sputtering:
- High-Quality Films: The monoenergetic and highly collimated ion beam produces films with exceptional density and uniformity.
- Precision Control: The process allows for precise control over film thickness and composition, making it ideal for applications requiring high accuracy.
- Versatility: IBS can be used to deposit a wide range of materials, including metals, oxides, and nitrides, on various substrates.
- Low Defect Density: The vacuum environment and controlled ion beam reduce the likelihood of defects, resulting in high-performance films.
-
Applications of Ion Beam Sputtering:
- Optical Coatings: IBS is widely used in the production of high-quality optical coatings, such as anti-reflective and mirror coatings.
- Semiconductor Industry: The technique is employed in the fabrication of thin films for semiconductor devices, where precision and film quality are critical.
- Magnetic Storage: IBS is used to deposit thin films for magnetic storage media, such as hard drives, due to its ability to produce dense, uniform films.
- Research and Development: The process is also used in R&D for developing new materials and coatings with specific properties.
In summary, ion beam sputtering is a sophisticated thin-film deposition technique that leverages a highly controlled ion beam to produce dense, high-quality films with exceptional precision. Its applications span various industries, including optics, semiconductors, and magnetic storage, where the demand for high-performance materials is paramount. The process's ability to deliver uniform, defect-free films makes it a valuable tool in both industrial and research settings.
Summary Table:
Key Aspect | Description |
---|---|
Process | Generates a focused, monoenergetic ion beam to sputter target material. |
Environment | Conducted in a vacuum chamber filled with inert gas (e.g., argon). |
Film Quality | Produces dense, uniform films with excellent adhesion and low defect density. |
Applications | Optical coatings, semiconductors, magnetic storage, and R&D. |
Advantages | High precision, versatility, and superior film performance. |
Interested in leveraging ion beam sputtering for your projects? Contact our experts today to learn more!