Ion sputtering is a precise and controlled process used to deposit thin films of materials onto substrates. It involves creating a vacuum environment, introducing an inert gas like argon, and ionizing the gas to form a plasma. The ions in the plasma are accelerated toward a target material, causing atoms to be ejected from the target's surface. These ejected atoms then travel through the vacuum chamber and deposit onto a substrate, forming a thin film. The process is highly accurate, repeatable, and capable of producing high-purity coatings, making it essential in industries such as semiconductors, optics, and precision manufacturing.
Key Points Explained:
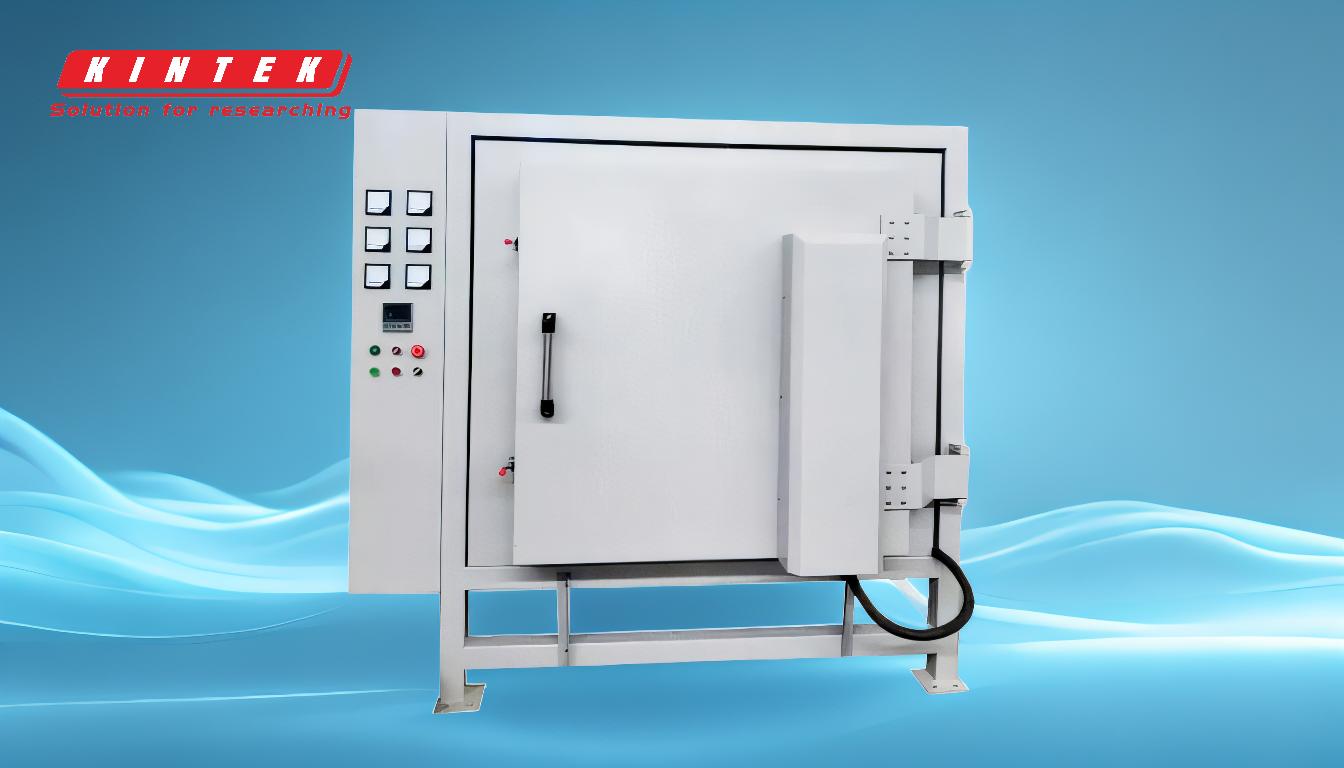
-
Vacuum Chamber Setup
- The process begins by placing the substrate and target material inside a vacuum chamber.
- Air is removed to create a vacuum, typically around 1 Pa (0.0000145 psi), to eliminate moisture and impurities that could contaminate the coating.
- This step ensures a clean environment for the deposition process, which is critical for achieving high-purity thin films.
-
Introduction of Inert Gas
- An inert gas, usually argon, is introduced into the chamber at low pressure (10^-1 to 10^-3 mbar).
- Argon is preferred because it is chemically inert and does not react with the target material or substrate.
- The low-pressure environment is necessary to maintain a stable plasma and prevent unwanted chemical reactions.
-
Plasma Generation
- A high voltage (3-5 kV) is applied to the target material, making it the cathode, while the substrate acts as the anode.
- This voltage ionizes the argon gas, creating a plasma composed of positively charged argon ions (Ar+) and free electrons.
- A magnetic field is often used to confine and accelerate the plasma, increasing the efficiency of the sputtering process.
-
Ion Bombardment of the Target
- The positively charged argon ions are attracted to the negatively charged target material.
- When these ions strike the target at high velocity, they transfer their kinetic energy, causing atoms to be ejected from the target's surface.
- This process is known as sputtering and is the core mechanism of the thin film deposition.
-
Transport of Sputtered Atoms
- The ejected atoms travel through the vacuum chamber in a straight line (line-of-sight) or are ionized and accelerated toward the substrate.
- The vacuum environment ensures minimal collisions with gas molecules, allowing the atoms to reach the substrate with high energy and precision.
-
Deposition on the Substrate
- The sputtered atoms condense on the substrate, forming a thin film.
- The substrate may be heated (150–750°C) to improve adhesion and film quality, depending on the material being deposited.
- The result is a uniform, high-purity coating with precise thickness and composition.
-
Advantages of Ion Sputtering
- High accuracy and repeatability, making it ideal for precision applications.
- Ability to deposit a wide range of materials, including metals, oxides, and alloys.
- Produces thin films with excellent adhesion, uniformity, and purity.
-
Applications of Ion Sputtering
- Semiconductor manufacturing: Deposition of conductive and insulating layers.
- Optics: Coating lenses and mirrors with reflective or anti-reflective layers.
- Precision engineering: Producing wear-resistant coatings for tools and components.
By following these steps, ion sputtering provides a reliable and versatile method for creating high-quality thin films, essential for advanced manufacturing and technology development.
Summary Table:
Key Step | Description |
---|---|
Vacuum Chamber Setup | Creates a clean environment by removing air and impurities (1 Pa pressure). |
Introduction of Inert Gas | Argon is introduced at low pressure (10^-1 to 10^-3 mbar) to form plasma. |
Plasma Generation | High voltage (3-5 kV) ionizes argon, creating plasma with Ar+ ions and electrons. |
Ion Bombardment of Target | Ar+ ions strike the target, ejecting atoms for deposition. |
Transport of Sputtered Atoms | Ejected atoms travel through the vacuum to the substrate with minimal collisions. |
Deposition on Substrate | Atoms condense on the substrate, forming a uniform, high-purity thin film. |
Advantages | High accuracy, repeatability, and ability to deposit various materials. |
Applications | Semiconductors, optics, and precision engineering. |
Discover how ion sputtering can enhance your manufacturing process—contact us today!