Media milling is a mechanical process used to reduce particle size and achieve uniform dispersion of particles in a liquid medium. It is widely used in industries such as pharmaceuticals, paints, coatings, and cosmetics to produce fine and stable suspensions. The process involves grinding or milling solid particles in a liquid medium using specialized equipment like bead mills, ball mills, or attritors. Key components include the milling chamber, grinding media (e.g., beads), and a rotating agitator. The process is highly customizable, with parameters such as media size, milling time, and agitator speed influencing the final product's particle size and distribution. Media milling is essential for achieving desired product characteristics like stability, texture, and performance.
Key Points Explained:
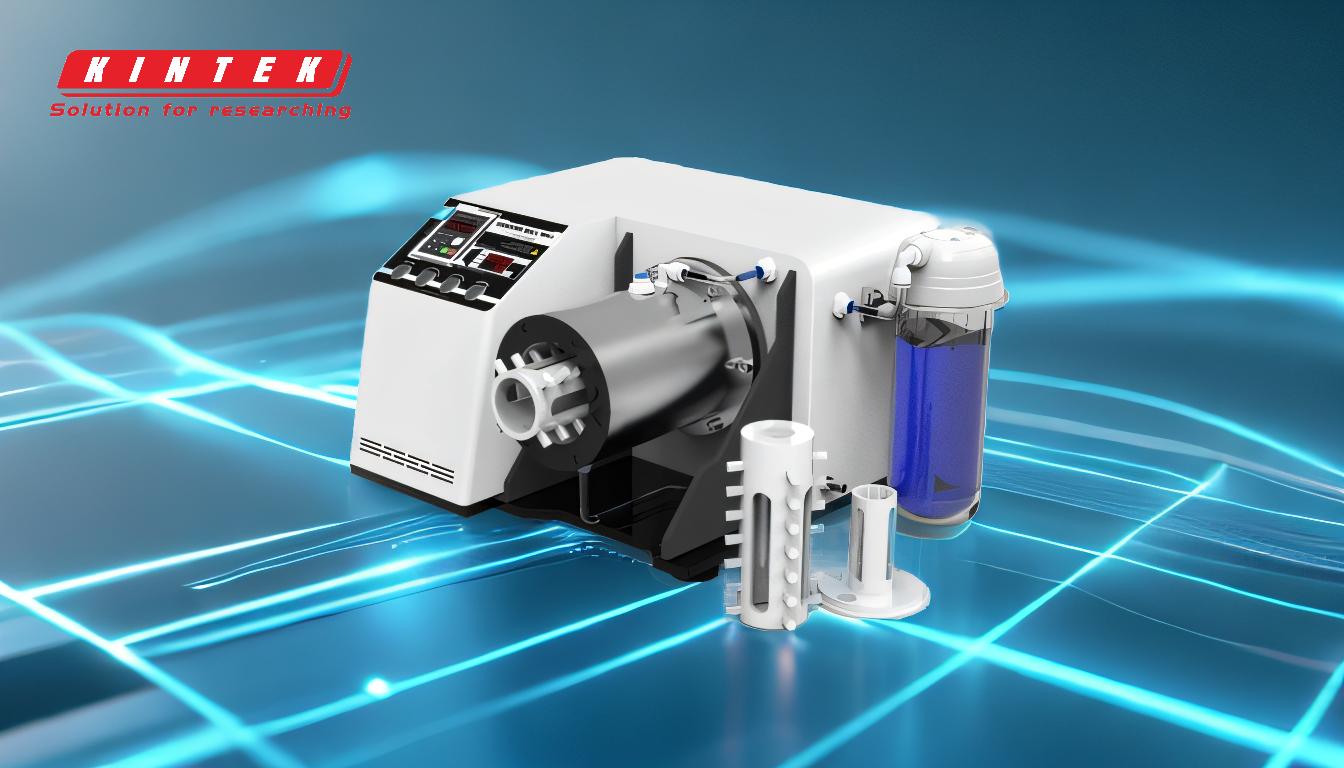
-
Definition and Purpose of Media Milling:
- Media milling is a mechanical process designed to reduce particle size and disperse particles uniformly in a liquid medium.
- It is used to create fine, stable suspensions or dispersions, which are critical in industries like pharmaceuticals, paints, and cosmetics.
-
Equipment Used in Media Milling:
- Bead Mills: Utilize small beads as grinding media to break down particles.
- Ball Mills: Use larger balls to grind materials in a rotating chamber.
- Attritors: Employ a vertical tank with agitators to mill materials.
- These machines are chosen based on the desired particle size and the properties of the material being processed.
-
Components of a Media Milling System:
- Milling Chamber: The container where the grinding process occurs.
- Grinding Media: Small beads or balls made of materials like glass, ceramics, or steel, which physically break down particles.
- Agitator: A rotating component that moves the grinding media and ensures uniform particle size reduction.
- Pump and Cooling System: To circulate the slurry and control temperature during milling.
-
Process Steps in Media Milling:
- Loading: The raw material (solid particles) and liquid medium are loaded into the milling chamber.
- Grinding: The agitator rotates, causing the grinding media to collide with the particles, reducing their size.
- Dispersion: The particles are uniformly dispersed in the liquid medium.
- Separation: The grinding media is separated from the final product using screens or filters.
- Collection: The finely milled product is collected for further processing or packaging.
-
Key Parameters Influencing Media Milling:
- Media Size: Smaller beads are used for finer particle sizes, while larger beads are suitable for coarser grinding.
- Milling Time: Longer milling times generally result in smaller particle sizes.
- Agitator Speed: Higher speeds increase the energy input, leading to faster particle size reduction.
- Slurry Concentration: The ratio of solid particles to liquid medium affects the efficiency of the milling process.
-
Applications of Media Milling:
- Pharmaceuticals: Used to create nanosuspensions for improved drug delivery.
- Paints and Coatings: Ensures uniform pigment dispersion for consistent color and texture.
- Cosmetics: Produces fine particles for smooth textures in creams and lotions.
- Food Industry: Used to create stable emulsions and suspensions in products like sauces and beverages.
-
Advantages of Media Milling:
- Precision: Allows for precise control over particle size and distribution.
- Scalability: Can be scaled from laboratory to industrial production.
- Versatility: Suitable for a wide range of materials and applications.
- Efficiency: Achieves fine particle sizes with relatively low energy consumption compared to other methods.
-
Challenges and Considerations:
- Media Wear: Grinding media can wear over time, contaminating the product.
- Heat Generation: The milling process generates heat, which can affect temperature-sensitive materials.
- Clogging: Fine particles can clog screens or filters, requiring regular maintenance.
- Cost: High initial investment and maintenance costs for equipment.
-
Future Trends in Media Milling:
- Nanomilling: Increasing focus on producing nanoparticles for advanced applications.
- Automation: Integration of automated systems for better process control and efficiency.
- Sustainable Practices: Development of eco-friendly grinding media and energy-efficient milling processes.
By understanding the process of media milling, its components, and key parameters, manufacturers can optimize the process to achieve desired product characteristics and improve efficiency.
Summary Table:
Aspect | Details |
---|---|
Purpose | Reduce particle size and achieve uniform dispersion in a liquid medium. |
Equipment | Bead mills, ball mills, attritors. |
Key Components | Milling chamber, grinding media, agitator, pump, and cooling system. |
Key Parameters | Media size, milling time, agitator speed, slurry concentration. |
Applications | Pharmaceuticals, paints, cosmetics, food industry. |
Advantages | Precision, scalability, versatility, efficiency. |
Challenges | Media wear, heat generation, clogging, cost. |
Future Trends | Nanomilling, automation, sustainable practices. |
Optimize your media milling process for superior results—contact our experts today!