Sputtering silicon involves a vacuum-based process where silicon atoms are ejected from a target material and deposited onto a substrate to form a thin film. The process begins by creating a vacuum in a chamber to remove impurities, followed by introducing an inert gas like argon. A high voltage is applied to ionize the gas, generating a plasma. The positively charged ions bombard the silicon target, causing silicon atoms to be ejected and deposited onto the substrate. This method ensures high precision and purity, making it ideal for applications in semiconductor manufacturing and thin-film coatings.
Key Points Explained:
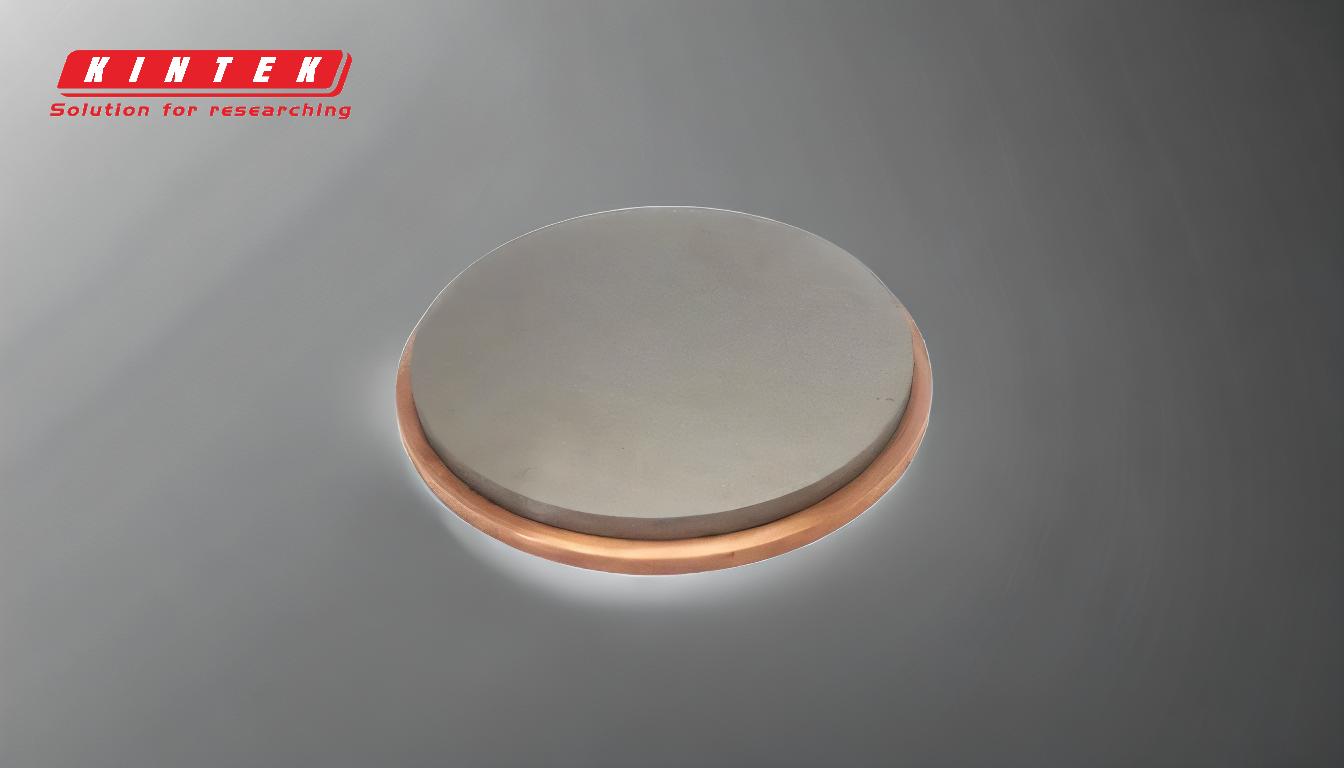
-
Vacuum Creation:
- The first step involves evacuating the reaction chamber to create a vacuum, typically around 1 Pa (0.0000145 psi). This removes moisture and impurities, ensuring a clean environment for the sputtering process.
- A vacuum is essential because it minimizes contamination and allows for precise control over the deposition process.
-
Introduction of Inert Gas:
- After achieving the desired vacuum, an inert gas such as argon is introduced into the chamber. This gas is chosen because it is chemically inert and does not react with the target material or the substrate.
- The inert gas creates a low-pressure atmosphere necessary for plasma generation.
-
Plasma Generation:
- A high voltage (3-5 kV) is applied to ionize the inert gas atoms, creating a plasma. This plasma consists of positively charged ions and free electrons.
- The plasma is crucial as it provides the energy needed to bombard the target material and eject silicon atoms.
-
Target Bombardment:
- The silicon target is negatively charged, attracting the positively charged ions from the plasma. When these ions collide with the silicon target, they transfer their energy, causing silicon atoms to be ejected from the target surface.
- This process is known as sputtering, and it is highly controlled to ensure uniform deposition.
-
Deposition on Substrate:
- The ejected silicon atoms travel through the vacuum chamber and deposit onto the substrate. The substrate is typically placed opposite the target, and the deposition occurs as a thin film.
- The substrate can be heated to temperatures ranging from 150 – 750°C (302 – 1382°F) to improve adhesion and film quality.
-
Magnetic Field Application (Optional):
- In some setups, an electromagnet is used to create a magnetic field around the tools. This magnetic field helps to confine the plasma and increase the efficiency of the sputtering process.
- The magnetic field enhances the ionization of the inert gas and improves the uniformity of the deposited film.
-
Film Formation:
- The deposited silicon atoms condense on the substrate, forming a thin film. The thickness and properties of the film can be precisely controlled by adjusting parameters such as voltage, gas pressure, and deposition time.
- This method allows for the creation of ultra-high purity silicon films, which are essential for applications in electronics and optics.
By following these steps, the sputtering process ensures the deposition of high-quality silicon films with excellent uniformity and purity, making it a preferred method for various industrial applications.
Summary Table:
Step | Key Details |
---|---|
Vacuum Creation | Chamber evacuated to 1 Pa (0.0000145 psi) to remove impurities. |
Inert Gas Intro | Argon introduced to create a low-pressure atmosphere for plasma generation. |
Plasma Generation | High voltage (3-5 kV) ionizes argon, creating plasma for target bombardment. |
Target Bombardment | Positively charged ions eject silicon atoms from the target. |
Deposition | Silicon atoms deposit onto a substrate, forming a thin film. |
Magnetic Field | Optional magnetic field enhances plasma confinement and film uniformity. |
Film Formation | Ultra-high purity silicon films with precise thickness and properties. |
Need high-quality silicon thin films for your applications? Contact our experts today to learn more!