Ball milling is a versatile and widely used technique in material science and engineering, primarily aimed at reducing particle size, mixing, and homogenizing materials. It involves the use of a rotating cylinder filled with grinding media (balls) to crush, grind, or mix materials into fine powders or nanoparticles. The process is critical in various applications, including the synthesis of metallic nanoparticles, the production of ultrafine and nano-sized materials, and the development of innovative products. By balancing cold welding and fracturing, ball milling can control particle size and morphology, making it a key tool in material synthesis and processing.
Key Points Explained:
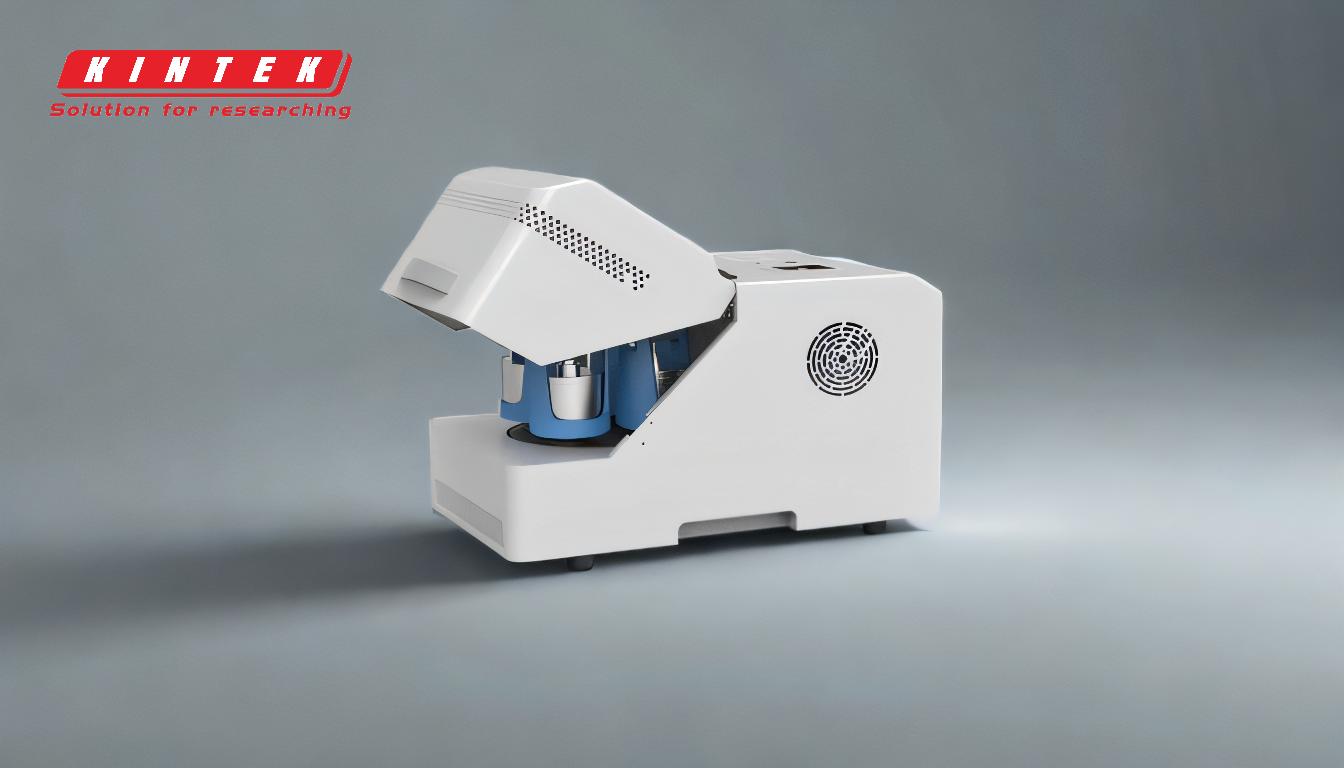
-
Purpose of Ball Milling:
- Particle Size Reduction: Ball milling is primarily used to reduce the size of particles, achieving ultrafine or nano-sized materials. This is essential for applications requiring high surface area or specific material properties.
- Mixing and Homogenization: It is also used to mix and homogenize materials, ensuring uniform distribution of components in composite materials or alloys.
- Synthesis of Nanoparticles: Ball milling is a key method for synthesizing metallic nanoparticles in large quantities, which are crucial for advanced materials and technologies.
-
Mechanism of Ball Milling:
- Cold Welding and Fracturing: During ball milling, particles are subjected to repeated impacts and collisions with grinding media. This process balances cold welding (particles sticking together) and fracturing (particles breaking apart), which helps control particle size and morphology.
- Energy Transfer: The kinetic energy from the rotating balls is transferred to the material, causing it to deform, fracture, or undergo mechanical alloying.
-
Applications of Ball Milling:
- Material Synthesis: Ball milling is used to synthesize a wide range of materials, including metals, ceramics, polymers, and composites. It is particularly useful for producing nano-sized materials with unique properties.
- Innovative Product Development: By enabling the production of ultrafine and nano-sized materials, ball milling contributes to the development of innovative products in fields such as electronics, energy storage, and catalysis.
- Cryogenic Ball Milling: At cryogenic temperatures, ball milling is used to synthesize metallic nanoparticles in large quantities. The low temperature helps control particle size by minimizing cold welding and enhancing fracturing.
-
Advantages of Ball Milling:
- Scalability: Ball milling can be scaled up for large-scale production, making it suitable for industrial applications.
- Versatility: It can be used for a wide range of materials and applications, from grinding to mechanical alloying.
- Control Over Particle Size: By adjusting milling parameters (e.g., speed, time, and ball size), particle size and morphology can be precisely controlled.
-
Challenges and Considerations:
- Contamination: Prolonged milling can lead to contamination from the grinding media or the milling environment.
- Heat Generation: High-energy ball milling can generate heat, which may affect the material properties. Cryogenic ball milling is one solution to mitigate this issue.
- Energy Consumption: Ball milling can be energy-intensive, especially for high-energy or long-duration processes.
In summary, ball milling serves as a critical tool in material science for reducing particle size, synthesizing nanoparticles, and developing innovative materials. Its ability to control particle size and morphology through a balance of cold welding and fracturing makes it indispensable in both research and industrial applications.
Summary Table:
Aspect | Details |
---|---|
Purpose | Particle size reduction, mixing, homogenization, nanoparticle synthesis. |
Mechanism | Balances cold welding and fracturing for precise particle control. |
Applications | Material synthesis, innovative product development, cryogenic milling. |
Advantages | Scalability, versatility, precise particle size control. |
Challenges | Contamination, heat generation, energy consumption. |
Learn how ball milling can revolutionize your material synthesis process—contact us today!