Pulverization is a critical process in various industries, aimed at reducing solid materials into fine powders or smaller particles, typically ranging between 100 and 50 micrometers. This mechanical reduction enhances the material's usability in industrial or pharmaceutical applications by improving surface area, reactivity, and uniformity. Pulverizers, the equipment used for this process, can operate in batch or continuous modes, often incorporating additional functions like cooling, heating, or aeration to optimize the material for its intended use. The process is essential for ensuring materials meet specific size and consistency requirements, which are vital for downstream processing, formulation, or application.
Key Points Explained:
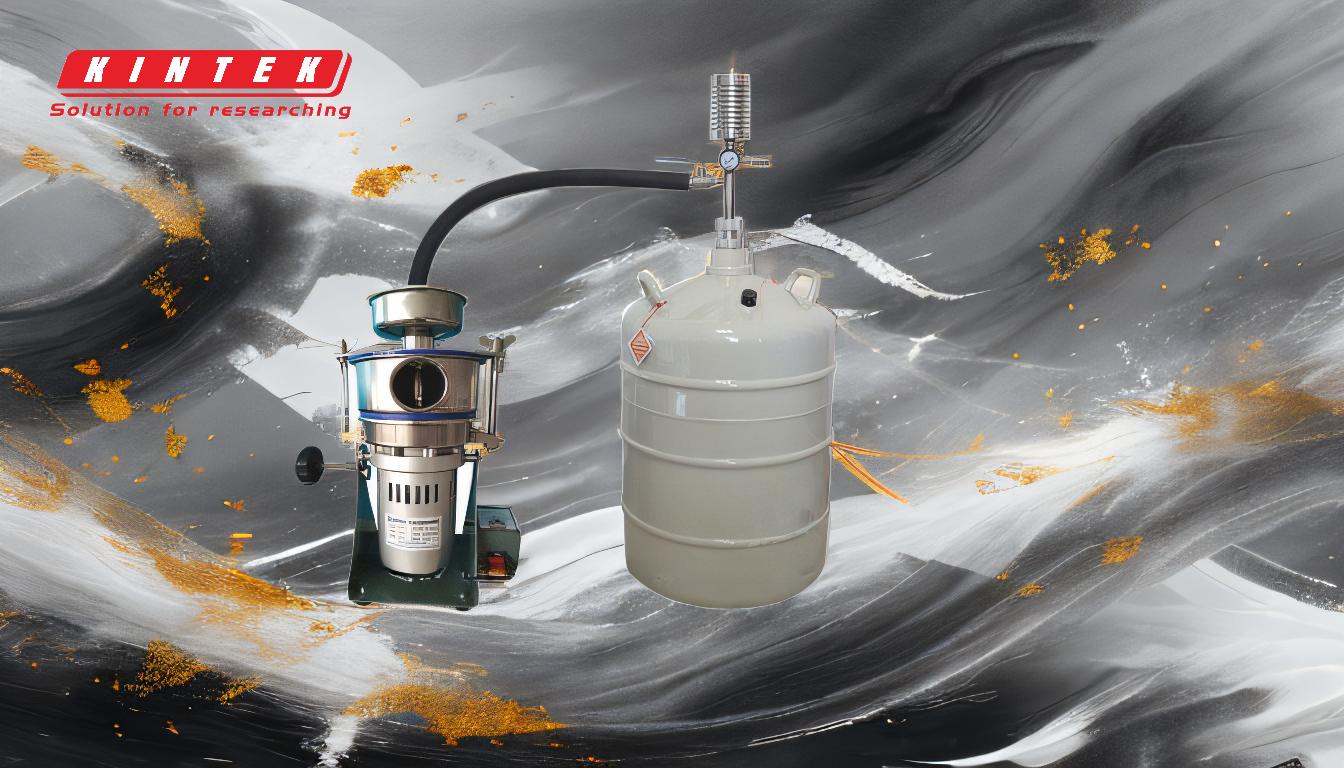
-
Purpose of Pulverization:
- Mechanical Reduction: Pulverization breaks down coarse solid materials into smaller, more manageable particles. This is crucial for materials that need to be processed further or used in applications requiring fine powders.
- Enhanced Surface Area: By reducing particle size, pulverization increases the material's surface area, which can improve reactivity, solubility, and mixing efficiency in industrial or pharmaceutical processes.
- Uniformity and Consistency: Achieving a consistent particle size ensures uniformity in product quality, which is essential for applications like drug formulation, chemical reactions, or material blending.
-
Industrial and Pharmaceutical Applications:
- Industrial Use: In industries such as mining, construction, and manufacturing, pulverization is used to prepare raw materials for further processing. For example, ores are pulverized to extract metals, and construction materials are ground to specific sizes for use in concrete or asphalt.
- Pharmaceutical Use: In the pharmaceutical industry, pulverization is critical for creating fine powders that can be easily compressed into tablets or dissolved in liquids. This ensures accurate dosing and bioavailability of active pharmaceutical ingredients (APIs).
-
Pulverization Process:
- Batch vs. Continuous Processing: Pulverizers can operate in batch mode, where materials are processed in discrete quantities, or continuously, where materials are fed into the system and processed without interruption. The choice depends on the scale and requirements of the operation.
- Additional Functions: Modern pulverizers often include features like cooling, heating, or aeration to modify the material's properties as it exits the machine. For example, cooling prevents heat-sensitive materials from degrading, while aeration can improve flowability.
-
Particle Size Control:
- Fineness Levels: Pulverizers can produce particles of varying fineness, from coarse to very fine, depending on the application. The desired particle size is determined by the material's intended use and the specific requirements of the process.
- Precision and Consistency: Advanced pulverizers are designed to achieve precise particle size distributions, ensuring consistency across batches. This is particularly important in industries like pharmaceuticals, where even minor variations can affect product performance.
-
Equipment and Technology:
- Types of Pulverizers: There are various types of pulverizers, including hammer mills, ball mills, and jet mills, each suited to different materials and applications. The choice of equipment depends on factors like material hardness, desired particle size, and processing capacity.
- Innovations in Pulverization: Advances in pulverization technology have led to more efficient and precise equipment, reducing energy consumption and improving output quality. For example, cryogenic pulverization uses liquid nitrogen to cool materials, making them more brittle and easier to grind.
-
Economic and Environmental Considerations:
- Cost Efficiency: Pulverization can reduce transportation and storage costs by decreasing the volume of materials. It also minimizes waste by ensuring that materials are fully utilized in downstream processes.
- Environmental Impact: Efficient pulverization processes can reduce energy consumption and emissions, contributing to more sustainable industrial practices. Additionally, recycling and reusing pulverized materials can minimize environmental footprint.
In summary, pulverization is a versatile and essential process that enhances the usability and performance of materials across various industries. By reducing particle size, increasing surface area, and ensuring uniformity, pulverization supports efficient processing, formulation, and application of materials, ultimately contributing to better product quality and sustainability.
Summary Table:
Key Aspect | Details |
---|---|
Purpose | Mechanical reduction, enhanced surface area, and uniformity. |
Applications | Industrial (mining, construction) and pharmaceutical (tablets, APIs). |
Processing Modes | Batch or continuous, with cooling, heating, or aeration options. |
Particle Size Control | Precise fineness levels for consistency in product quality. |
Equipment Types | Hammer mills, ball mills, jet mills, and cryogenic pulverizers. |
Economic & Environmental | Cost efficiency, reduced waste, and sustainable practices. |
Ready to optimize your pulverization process? Contact our experts today for tailored solutions!