Sputter coating is a critical process in scanning electron microscopy (SEM) used to prepare non-conductive or poorly conductive specimens for imaging and analysis. By applying an ultra-thin layer of conductive material, such as gold, platinum, or gold/palladium alloys, sputter coating prevents charging effects caused by the electron beam, enhances secondary electron detection, and improves the signal-to-noise ratio. This results in higher-quality images and protects beam-sensitive samples from damage. The process is particularly essential for materials that would otherwise accumulate surface electrons, leading to imaging artifacts. Sputter coating is also tailored for specific applications, such as using carbon coatings for X-ray spectroscopy to avoid interference from metal coatings.
Key Points Explained:
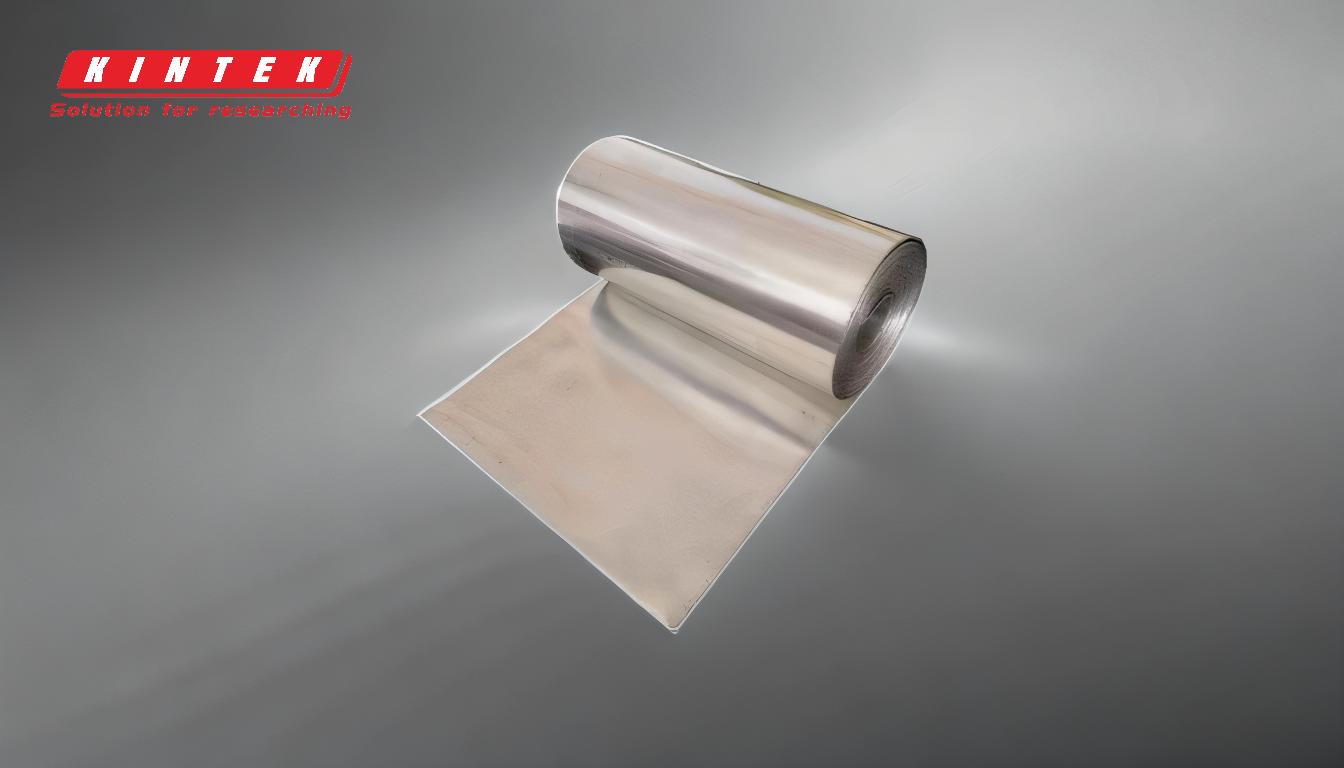
-
Preventing Charging Effects:
- Non-conductive or poorly conductive specimens can accumulate surface electrons when exposed to the electron beam in an SEM, leading to charging effects. These effects distort the image and make accurate analysis difficult.
- Sputter coating applies a thin conductive layer (typically 2–20 nm thick) to the specimen, which dissipates the accumulated electrons and prevents charging.
-
Enhancing Secondary Electron Detection:
- Secondary electrons are crucial for creating high-resolution topographic images in SEM. A conductive coating increases the emission of secondary electrons from the specimen's surface.
- This enhancement improves the signal-to-noise ratio, resulting in clearer and more detailed images.
-
Improving Signal-to-Noise Ratio:
- The conductive layer reduces background noise and enhances the signal from the specimen, leading to better image quality.
- This is particularly important for beam-sensitive samples, which require minimal electron beam exposure to avoid damage.
-
Protecting Beam-Sensitive Samples:
- Some specimens, such as biological or organic materials, are sensitive to the electron beam and can degrade under prolonged exposure.
- The conductive coating provides a protective layer, reducing thermal damage and preserving the specimen's integrity during imaging.
-
Material Choices for Sputter Coating:
- Commonly used metals include gold, gold/palladium, platinum, silver, chromium, and iridium. Each material has specific properties that make it suitable for different applications.
- For example, gold/palladium alloys are often chosen for their fine grain size, which minimizes interference with high-resolution imaging.
- Carbon coatings are preferred for X-ray spectroscopy to avoid interference from metal coatings.
-
Applications in SEM and Beyond:
- Sputter coating is primarily used in SEM to prepare specimens for imaging and analysis.
- It is also employed in other fields, such as materials science and nanotechnology, to create thin films with specific electrical or structural properties.
-
Process and Thickness Control:
- The sputter coating process involves depositing a thin layer of conductive material onto the specimen using a sputtering device.
- The thickness of the coating (typically 2–20 nm) is carefully controlled to ensure optimal conductivity without obscuring the specimen's surface features.
By addressing these key points, sputter coating ensures that non-conductive or poorly conductive specimens can be effectively imaged and analyzed in an SEM, providing researchers with high-quality data and insights.
Summary Table:
Key Benefits of Sputter Coating | Details |
---|---|
Prevents Charging Effects | Dissipates surface electrons for distortion-free imaging. |
Enhances Secondary Electron Detection | Improves signal-to-noise ratio for clearer images. |
Protects Beam-Sensitive Samples | Reduces thermal damage and preserves specimen integrity. |
Material Choices | Gold, platinum, gold/palladium, carbon, and more for specific applications. |
Applications | SEM imaging, materials science, nanotechnology, and X-ray spectroscopy. |
Thickness Control | 2–20 nm coatings ensure optimal conductivity and surface feature visibility. |
Optimize your SEM imaging with sputter coating—contact our experts today for tailored solutions!