Activated carbon regeneration, also known as reactivation, is the process of removing adsorbed contaminants from activated carbon through physical or chemical methods. This process restores the carbon's adsorption capacity without destroying its original structure, allowing it to be reused. Regeneration is a cost-effective and environmentally friendly approach, as it extends the lifespan of activated carbon and reduces waste. The methods used for regeneration depend on the type of contaminants adsorbed and the specific application of the activated carbon. Common techniques include thermal, chemical, and biological regeneration.
Key Points Explained:
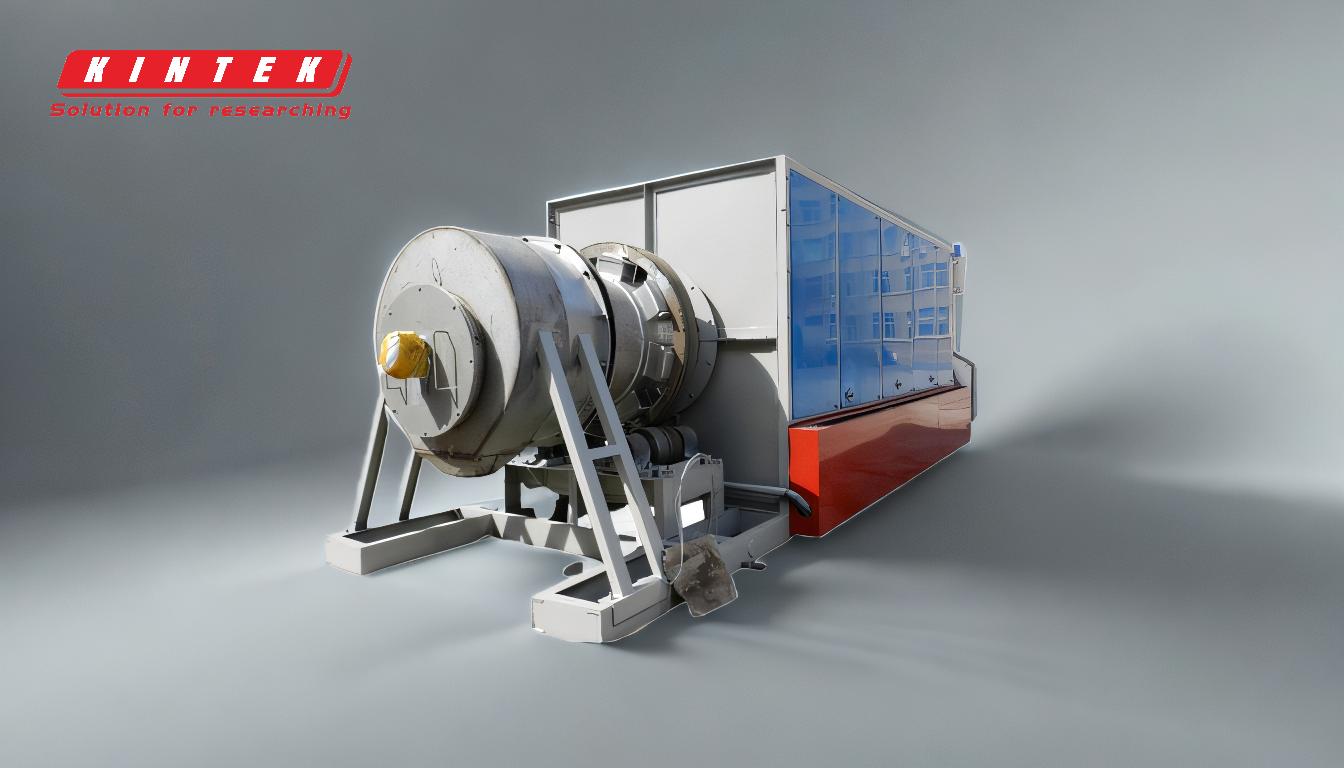
-
Definition of Activated Carbon Regeneration:
- Regeneration refers to the removal of adsorbed materials from activated carbon while preserving its original structure.
- The goal is to restore the carbon's adsorption performance so it can be reused.
-
Purpose of Regeneration:
- Cost-Effectiveness: Reusing activated carbon reduces the need for frequent replacements, lowering operational costs.
- Environmental Benefits: Regeneration minimizes waste and reduces the environmental impact of disposing of spent carbon.
- Sustainability: Extending the lifespan of activated carbon aligns with sustainable resource management practices.
-
Methods of Regeneration:
-
Thermal Regeneration:
- Involves heating the carbon to high temperatures (600–900°C) in the absence of oxygen to vaporize and burn off adsorbed contaminants.
- Commonly used for organic contaminants.
-
Chemical Regeneration:
- Uses chemical agents (e.g., acids, bases, or solvents) to desorb contaminants from the carbon.
- Suitable for specific contaminants that are chemically reactive.
-
Biological Regeneration:
- Utilizes microorganisms to break down adsorbed organic contaminants.
- Often used in wastewater treatment applications.
-
Thermal Regeneration:
-
Factors Influencing Regeneration:
- Type of Contaminants: The nature of the adsorbed materials determines the most effective regeneration method.
- Carbon Structure: The porosity and surface area of the activated carbon affect its regeneration efficiency.
- Application: Different industries (e.g., water treatment, air purification) may require tailored regeneration approaches.
-
Advantages of Regeneration:
- Economic Savings: Reduces the need for new activated carbon purchases.
- Resource Efficiency: Maximizes the use of existing materials.
- Waste Reduction: Decreases the volume of spent carbon sent to landfills.
-
Challenges in Regeneration:
- Energy Consumption: Thermal regeneration, in particular, requires significant energy input.
- Loss of Carbon: Some carbon may be lost during the regeneration process, reducing its overall lifespan.
- Contaminant Residues: Incomplete regeneration can leave behind residual contaminants, affecting performance.
By understanding these key points, purchasers of activated carbon and related equipment can make informed decisions about when and how to implement regeneration processes, ensuring optimal performance and cost-efficiency.
Summary Table:
Aspect | Details |
---|---|
Definition | Removal of adsorbed contaminants while preserving carbon structure. |
Purpose | Cost-effectiveness, environmental benefits, and sustainability. |
Methods | Thermal, chemical, and biological regeneration. |
Factors Influencing | Contaminant type, carbon structure, and application. |
Advantages | Economic savings, resource efficiency, and waste reduction. |
Challenges | Energy consumption, carbon loss, and residual contaminants. |
Discover how activated carbon regeneration can benefit your operations—contact us today!