The size of a pyrolysis plant varies depending on its design, capacity, and intended application. Continuous pyrolysis plants are generally compact, designed for long-term operation (8-10 years), and capable of processing large volumes of waste materials like tires, plastics, and biomass. They can operate 24/7 for extended periods, with capacities ranging from small-scale units processing 4 tons per day to larger industrial systems. The modular design allows for scalability, enabling users to expand the plant's capacity as needed. The plant typically includes a reactor, condenser, and energy module, with some designs integrating these components to reduce energy losses. Overall, the size of a pyrolysis plant is influenced by its processing capacity, operational requirements, and modularity.
Key Points Explained:
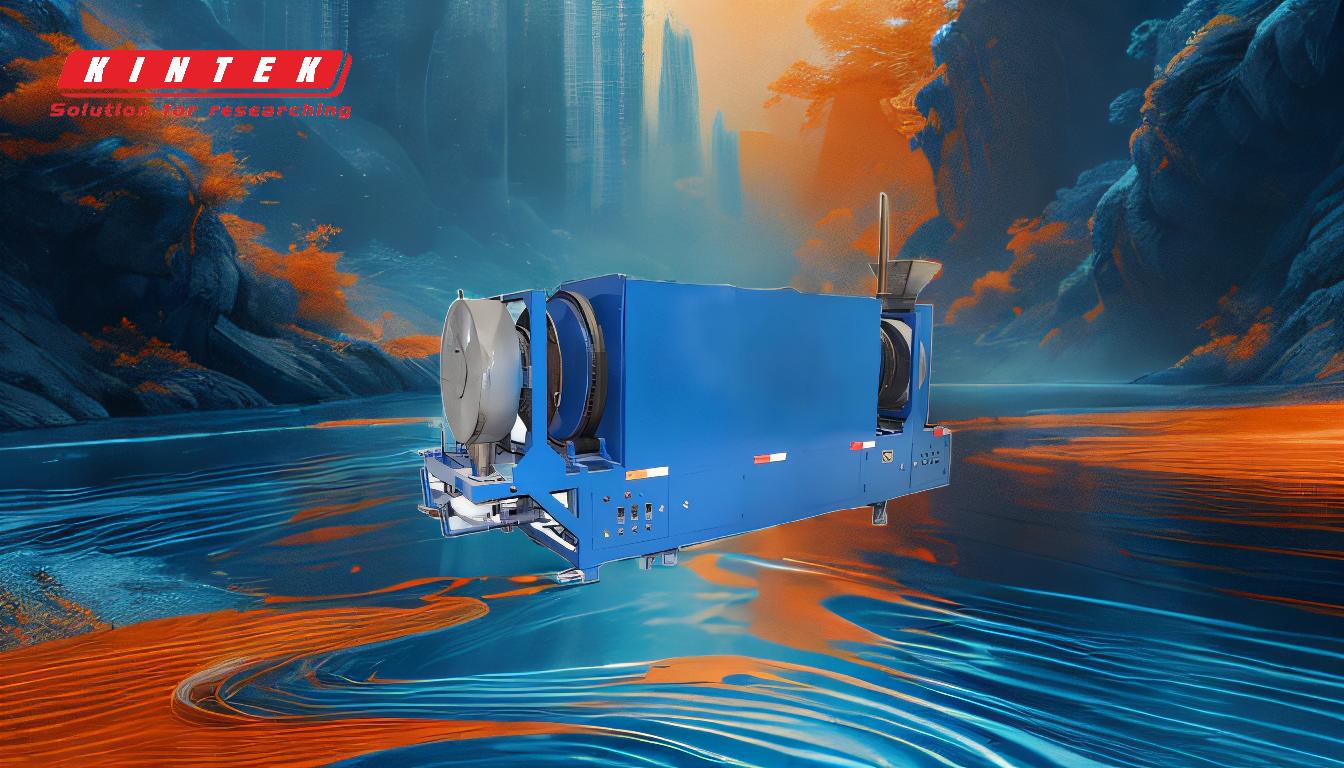
-
Variability in Size Based on Design and Capacity:
- Pyrolysis plants are not one-size-fits-all; their dimensions depend on factors like processing capacity, feedstock type, and operational goals.
- Continuous pyrolysis plants, for instance, are designed for high-volume, uninterrupted operation, making them larger than batch-type plants.
- Smaller units might process 4 tons of waste per day, while industrial-scale plants can handle significantly more.
-
Compact and Modular Design:
- Many pyrolysis plants, especially continuous ones, are compact and modular, allowing for easy installation and scalability.
- Modularity enables users to start with a smaller unit and expand capacity by adding more reactors or modules as needed.
- This design flexibility makes pyrolysis plants suitable for both small businesses and large industrial operations.
-
Components Influencing Size:
- The primary components of a pyrolysis plant include the reactor, condenser, and energy module (furnace).
- The reactor size directly correlates with the plant's processing capacity. Larger reactors are needed for higher throughput.
- Some designs integrate the reactor and energy module to save space and reduce energy losses, though this requires advanced construction materials.
-
Processing Capacity and Output:
- The size of a pyrolysis plant is closely tied to its daily processing capacity. For example, a tire pyrolysis system can process 1000 kg of tires per reactor in 4-6 hours, yielding a daily output of 4 tons per reactor.
- Continuous plants can operate 24/7 for over 30 days, making them larger but more efficient for high-volume processing.
-
Scalability and Expansion:
- One of the key advantages of pyrolysis plants is their ability to expand indefinitely. Users can add more reactors or modules to increase capacity without significant redesign.
- This scalability makes pyrolysis plants adaptable to growing business needs or increased waste processing demands.
-
Environmental and Safety Considerations:
- Despite their size, pyrolysis plants are designed with environmental and safety features, such as de-dusting systems and hydroseals, to prevent pollution.
- These features may add to the overall footprint of the plant but are essential for sustainable and compliant operation.
-
Energy Efficiency and Space Optimization:
- Modern pyrolysis plants are designed to minimize energy losses, often by integrating components like the reactor and furnace.
- This integration reduces the overall size of the plant while improving energy efficiency, though it requires high-quality materials and precise temperature control.
-
Application-Specific Sizing:
- The size of a pyrolysis plant also depends on its intended application. For example, plants processing tires may require additional space for handling and preprocessing, while those processing plastics or biomass might have different spatial requirements.
In summary, the size of a pyrolysis plant is influenced by its design, capacity, modularity, and application. Continuous plants are generally larger due to their high processing capacity and 24/7 operation, while modular designs allow for scalability. The integration of components like the reactor and energy module can optimize space and energy efficiency, though this may increase the complexity of the system. Ultimately, the size of a pyrolysis plant is tailored to meet the specific needs of the user, balancing capacity, efficiency, and environmental considerations.
Summary Table:
Factor | Description |
---|---|
Design & Capacity | Size varies based on processing capacity, feedstock type, and operational goals. |
Modularity | Compact and modular designs allow for easy scalability and installation. |
Key Components | Reactor, condenser, and energy module influence overall size and efficiency. |
Processing Capacity | Ranges from 4 tons/day for small units to larger industrial systems. |
Scalability | Expandable by adding more reactors or modules to meet growing demands. |
Environmental Features | Includes de-dusting systems and hydroseals for sustainable operation. |
Energy Efficiency | Integrated components reduce energy losses and optimize space. |
Application-Specific | Size varies by feedstock (tires, plastics, biomass) and preprocessing needs. |
Ready to scale your waste processing? Contact us today to find the perfect pyrolysis plant for your needs!