The speed of a sieving machine is a critical factor that directly impacts the efficiency and accuracy of the particle separation process. It is influenced by factors such as the type of material being sieved, the mesh size, and the design of the machine. Generally, sieving machines operate at speeds ranging from 100 to 300 RPM (revolutions per minute), but this can vary depending on the specific application. The speed must be optimized to ensure that particles are effectively separated without causing damage to the material or the sieve itself.
Key Points Explained:
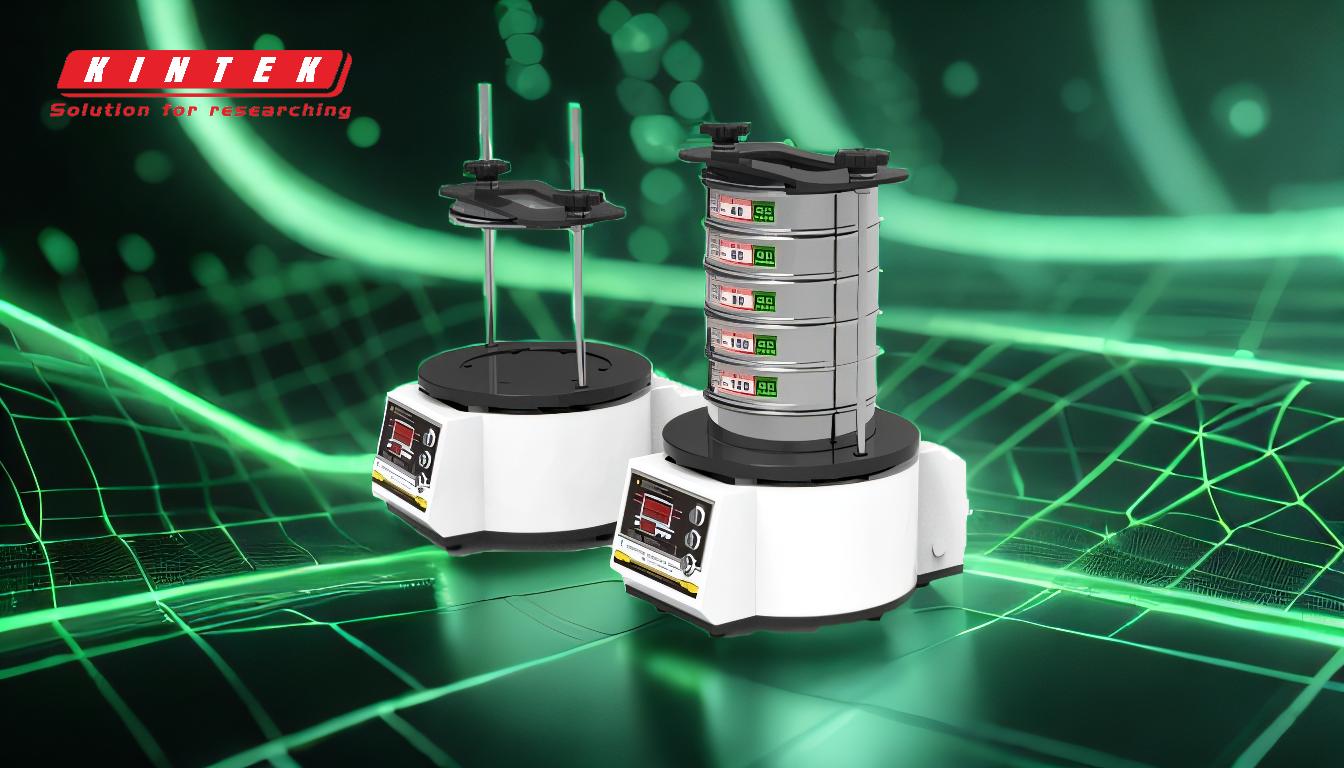
-
Definition of Sieving Machine Speed:
- The speed of a sieving machine refers to the rate at which the sieve vibrates or rotates to facilitate the separation of particles. It is typically measured in revolutions per minute (RPM).
-
Typical Speed Range:
- Most sieving machines operate within a speed range of 100 to 300 RPM. This range is suitable for a wide variety of materials and mesh sizes, ensuring efficient separation without excessive wear and tear.
-
Factors Influencing Speed:
- Material Characteristics: The size, shape, and density of the particles being sieved can affect the optimal speed. For example, finer particles may require a higher speed to pass through the mesh, while larger particles may need a slower speed to avoid clogging.
- Mesh Size: The size of the mesh openings plays a significant role in determining the appropriate speed. Smaller mesh sizes may require higher speeds to ensure that particles pass through, whereas larger mesh sizes may need lower speeds to prevent damage to the sieve.
- Machine Design: The design of the sieving machine, including the type of motion (e.g., vibratory, rotary) and the amplitude of vibration, can influence the optimal operating speed.
-
Importance of Optimizing Speed:
- Efficiency: Operating at the correct speed ensures that particles are separated efficiently, reducing the time required for the sieving process.
- Accuracy: Proper speed settings help achieve accurate particle size distribution, which is crucial for quality control in various industries.
- Machine Longevity: Running the machine at an appropriate speed minimizes wear and tear, extending the lifespan of the sieve and the machine.
-
Adjusting Speed for Different Applications:
- Fine Powders: For fine powders, higher speeds (closer to 300 RPM) may be necessary to ensure that particles pass through the mesh without clogging.
- Coarse Materials: For coarser materials, lower speeds (around 100 RPM) are often sufficient to separate particles without causing damage to the sieve or the material.
- Variable Speed Machines: Some advanced sieving machines come with variable speed settings, allowing operators to adjust the speed based on the specific requirements of the material being sieved.
-
Impact of Speed on Sieve Performance:
- Over-Speeding: Running the machine at speeds higher than recommended can lead to excessive vibration, which may cause damage to the sieve or the machine. It can also result in inaccurate separation due to particles bouncing off the mesh.
- Under-Speeding: Operating at speeds lower than necessary can result in incomplete separation, with particles not passing through the mesh efficiently. This can lead to longer sieving times and reduced throughput.
-
Practical Considerations for Purchasers:
- Application Requirements: When selecting a sieving machine, consider the specific requirements of your application, including the type of material, desired particle size, and throughput.
- Speed Control Features: Look for machines with adjustable speed settings to accommodate different materials and mesh sizes.
- Durability and Maintenance: Ensure that the machine is designed to handle the intended speed range without excessive wear, and consider the ease of maintenance.
In summary, the speed of a sieving machine is a crucial parameter that must be carefully selected and adjusted based on the material being processed, the mesh size, and the machine's design. Proper optimization of speed ensures efficient and accurate particle separation, prolongs the life of the equipment, and meets the specific needs of various industrial applications.
Summary Table:
Aspect | Details |
---|---|
Typical Speed Range | 100-300 RPM |
Key Influencing Factors | Material type, mesh size, machine design |
Fine Powders | Higher speeds (~300 RPM) for efficient separation |
Coarse Materials | Lower speeds (~100 RPM) to avoid damage |
Over-Speeding Risks | Excessive vibration, sieve damage, inaccurate separation |
Under-Speeding Risks | Incomplete separation, longer sieving times, reduced throughput |
Optimization Benefits | Improved efficiency, accuracy, and machine longevity |
Need help selecting the right sieving machine speed for your application? Contact our experts today for tailored advice!