Sputter coating is a sophisticated thin-film deposition technique widely used in nanotechnology and materials science. It involves bombarding a target material with high-energy particles, typically argon ions, in a vacuum environment. This process dislodges atoms from the target, which then deposit onto a substrate, forming a thin, uniform film. Sputter coating is versatile, capable of handling metals, alloys, and insulators, and offers precise control over film thickness and composition. It is particularly advantageous for applications requiring strong adhesion, dense films, and uniform coatings over large areas. The technique is essential in industries such as semiconductor manufacturing, optics, and microscopy, where high-quality thin films are critical.
Key Points Explained:
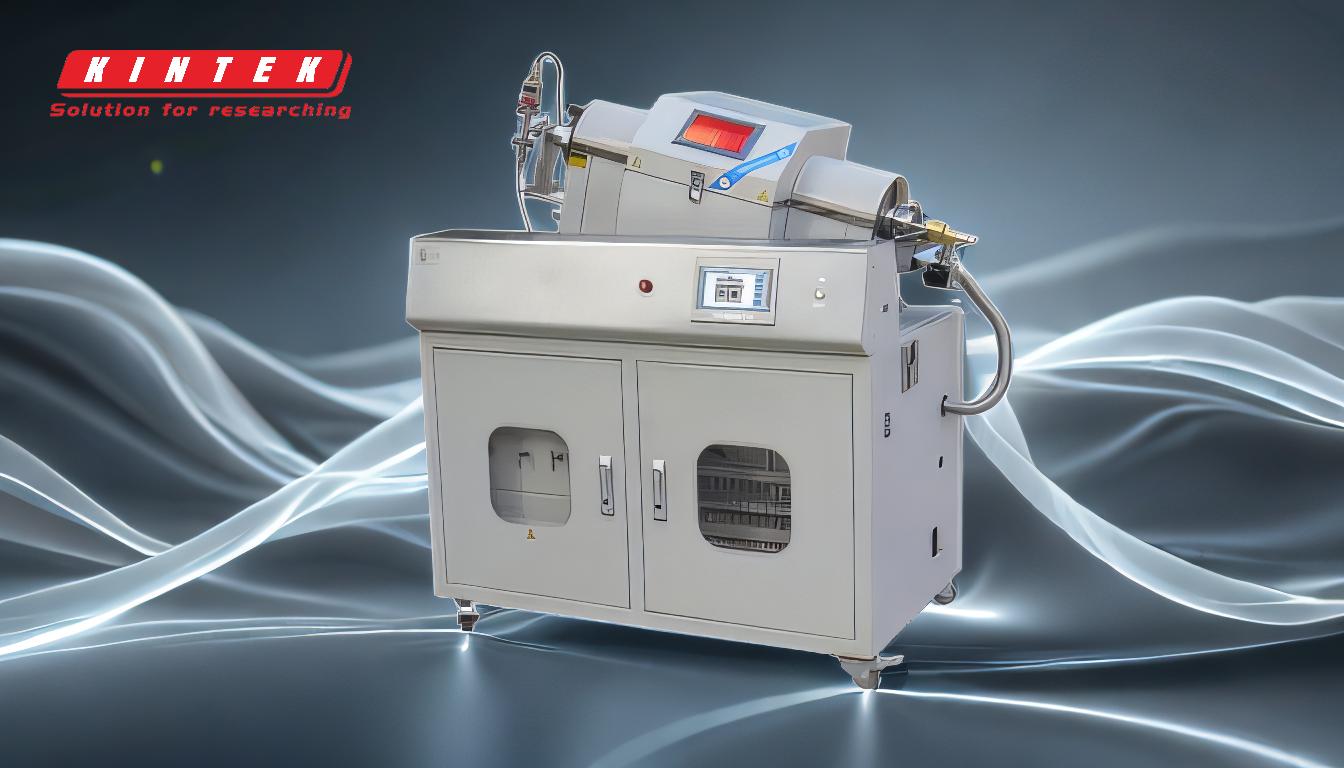
-
Basic Principle of Sputter Coating:
- Sputter coating involves the use of high-energy particles, usually argon ions, to bombard a target material in a vacuum. This bombardment causes atoms to be ejected from the target and deposited onto a substrate, forming a thin film. The process is initiated by ionizing argon gas and accelerating the ions towards the target material.
-
Types of Sputtering Techniques:
- DC Diode Sputtering: The simplest form, but has limitations such as low deposition rates and inability to sputter insulating materials.
- DC Triple and Quadrupole Sputtering: These methods improve ionization and stabilize discharge, though challenges like low plasma concentration and deposition rates persist.
-
Key Characteristics of Sputter Coating:
- Versatility: Can be used with metals, alloys, and insulators.
- Composition Control: Multi-component targets can produce films of the same composition.
- Reactive Sputtering: Adding gases like oxygen can create compound films.
- Precision: High control over film thickness through target input current and sputtering time.
- Uniformity: Excellent for producing large-area uniform films.
- Flexibility: Sputtered particles are not affected by gravity, allowing flexible arrangement of target and substrate.
- Adhesion and Density: Stronger adhesion and denser films compared to vacuum evaporation.
- Nucleation Density: High nucleation density allows for extremely thin continuous films.
- Target Longevity: Targets have a long service life, enabling continuous production.
- Shape Flexibility: Targets can be made into various shapes for better control and efficiency.
-
Applications of Sputter Coating:
- Semiconductor Manufacturing: Used for depositing thin films on silicon wafers.
- Optics: Essential for creating coatings on optical components.
- Microscopy: Improves secondary electron emission in Scanning Electron Microscopy (SEM) by reducing charging and thermal damage.
-
Advantages Over Other Techniques:
- Strong Adhesion: Films adhere more strongly to substrates.
- Dense Films: Produces denser and more uniform films.
- Lower Temperature Crystallization: Can form crystalline films at lower temperatures.
- High Precision: Allows for precise control over film thickness and composition.
-
Process Details:
- Vacuum Environment: The process occurs in a vacuum chamber to avoid contamination and ensure uniform deposition.
- Plasma Creation: Gaseous plasma is created, and ions are accelerated towards the target material.
- Deposition: Ejected particles from the target deposit onto the substrate, forming a thin film.
-
Improvements and Innovations:
- Plasma Sputter Coating: Uses plasma ions to vaporize the coating material, enhancing precision and uniformity.
- Reactive Sputtering: Incorporates reactive gases to create compound films, expanding the range of possible coatings.
Sputter coating is a versatile and precise method for depositing thin films, offering numerous advantages over other deposition techniques. Its ability to produce high-quality, uniform films with strong adhesion makes it indispensable in various high-tech industries.
Summary Table:
Aspect | Details |
---|---|
Basic Principle | Bombarding a target material with high-energy particles in a vacuum. |
Key Characteristics | Versatile, precise, uniform, strong adhesion, dense films, flexible. |
Applications | Semiconductor manufacturing, optics, microscopy. |
Advantages | Strong adhesion, dense films, lower temperature crystallization, precision. |
Process | Occurs in a vacuum, involves plasma creation and deposition. |
Interested in sputter coating solutions for your industry? Contact us today to learn more!