The vacuum level of a rotary vacuum pump, such as a rotary vane or rotary piston pump, typically ranges from 5x10^-2 mbar to below 10^-3 mbar, depending on the specific type and design. Rotary vane pumps, which are oil-sealed, are commonly used for applications requiring strong and consistent vacuum pressures below 10^-3 mbar, such as in freeze dryers, mass spectrometry, and hydraulic brake systems. These pumps are cost-effective and suitable for continuous suction and dry gas extraction. However, their vacuum level is influenced by factors like the solvent's evaporation rate and the system's temperature. While rotary vane pumps are reliable, they do have drawbacks, such as generating toxic oil waste and challenges in sourcing spare parts.
Key Points Explained:
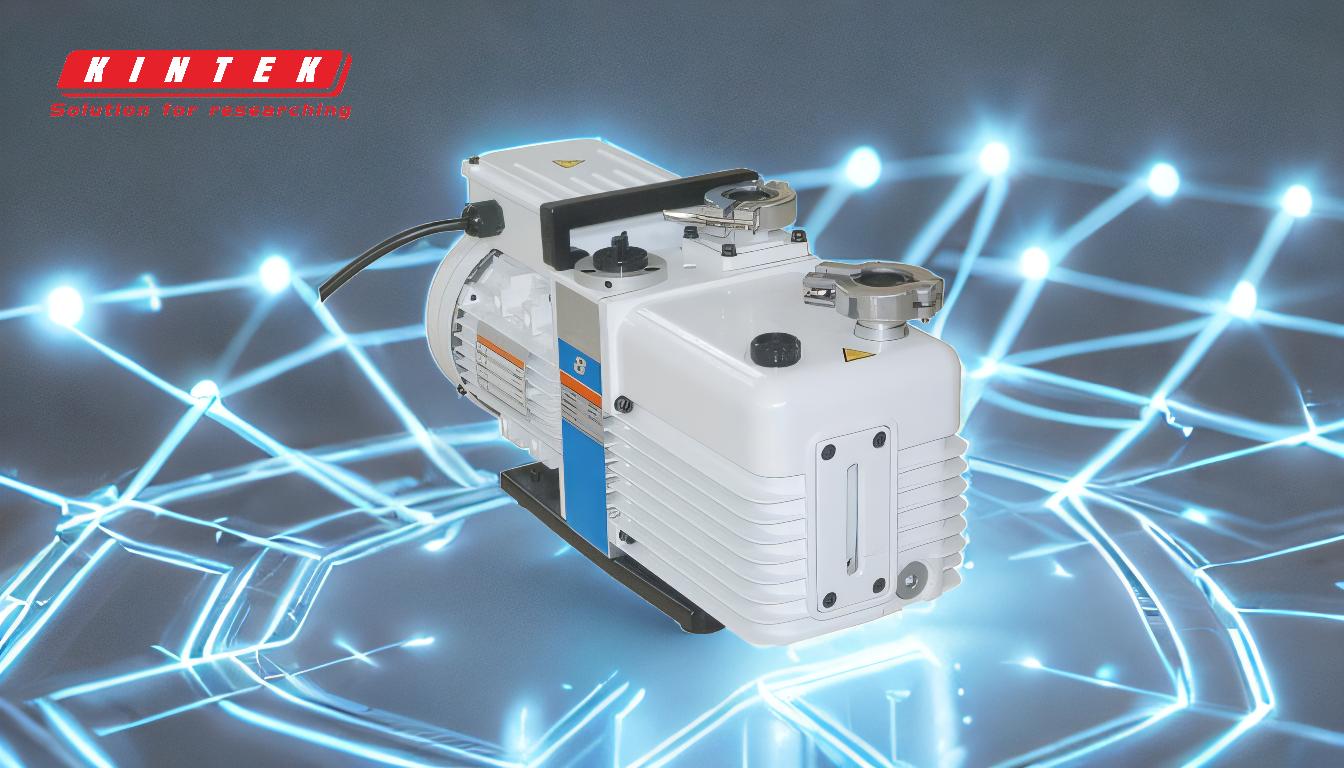
-
Vacuum Level Range of Rotary Vacuum Pumps:
- Rotary vane vacuum pumps typically achieve vacuum levels of 5x10^-2 mbar to below 10^-3 mbar.
- Turbomolecular pumps, another type of rotary pump, can achieve even lower vacuum levels, down to 1x10^-5 mbar.
- The vacuum level depends on the pump's design, sealing mechanism, and operational conditions.
-
Rotary Vane Vacuum Pumps:
- These are oil-sealed pumps that provide strong and consistent vacuum pressures below 10^-3 mbar.
- They are widely used in applications like hydraulic brake systems, freeze dryers, and mass spectrometry.
- Rotary vane pumps are cost-effective and suitable for continuous suction and dry gas extraction.
- They are equipped with air filters to remove dust particles, making them usable directly in the atmosphere.
-
Factors Affecting Vacuum Level:
- The evaporation rate of solvents and the system's temperature significantly influence the required vacuum level.
- The chemical composition of the gas being pumped affects the pumping rate, with different pump types (e.g., momentum transfer or entrapment pumps) being more effective for specific gases.
-
Rotary Piston Vacuum Pumps:
- These pumps use an eccentric wheel as the rotor and operate as two-stroke, double-acting pumps with two separate compression chambers.
- During operation, one chamber undergoes an intake stroke while the other performs an exhaust stroke, progressively reducing the compression chamber's size.
- This design allows for efficient fluid compression and ejection.
-
Advantages of Rotary Vacuum Pumps:
- They are easy to use and cost-effective.
- Suitable for continuous operation and dry gas extraction.
- Equipped with air filters for dust removal, enhancing their usability in atmospheric conditions.
-
Disadvantages of Rotary Vacuum Pumps:
- Oil-sealed pumps generate toxic oil waste, requiring proper disposal.
- Finding replacement spare parts can be challenging, especially for older or less common models.
- The small clearances between the rotor and housing require self-lubricating or low-friction materials to prevent fluid leakage, which can wear over time.
-
Applications of Rotary Vacuum Pumps:
- Commonly used in laboratory settings, industrial processes, and specialized equipment like freeze dryers and mass spectrometers.
- Ideal for processes requiring consistent low-pressure regions and continuous suction.
By understanding these key points, a purchaser can evaluate whether a rotary vacuum pump meets their specific requirements, considering factors like vacuum level, application, and maintenance needs.
Summary Table:
Aspect | Details |
---|---|
Vacuum Level Range | 5x10^-2 mbar to below 10^-3 mbar (rotary vane); down to 1x10^-5 mbar (turbomolecular) |
Key Applications | Freeze dryers, mass spectrometry, hydraulic brake systems |
Advantages | Cost-effective, continuous suction, dry gas extraction, equipped with air filters |
Disadvantages | Generates toxic oil waste, spare parts challenges, wear over time |
Factors Affecting Performance | Solvent evaporation rate, system temperature, gas chemical composition |
Need help selecting the right rotary vacuum pump for your application? Contact our experts today!