A sieve shaker is a device used to separate particles of different sizes by vibrating a stack of sieves with varying mesh sizes. The working principle revolves around a vibration motor that generates mechanical vibrations, which are transmitted to the sieves. These vibrations cause particles to move and pass through the sieve openings if they are smaller than the mesh size. Larger particles remain on the sieve, while smaller ones fall to the next level. This process continues through the stack, resulting in the separation of particles into distinct size fractions. The sieve shaker enhances efficiency, accuracy, and consistency compared to manual sieving, making it a valuable tool in material analysis and quality control.
Key Points Explained:
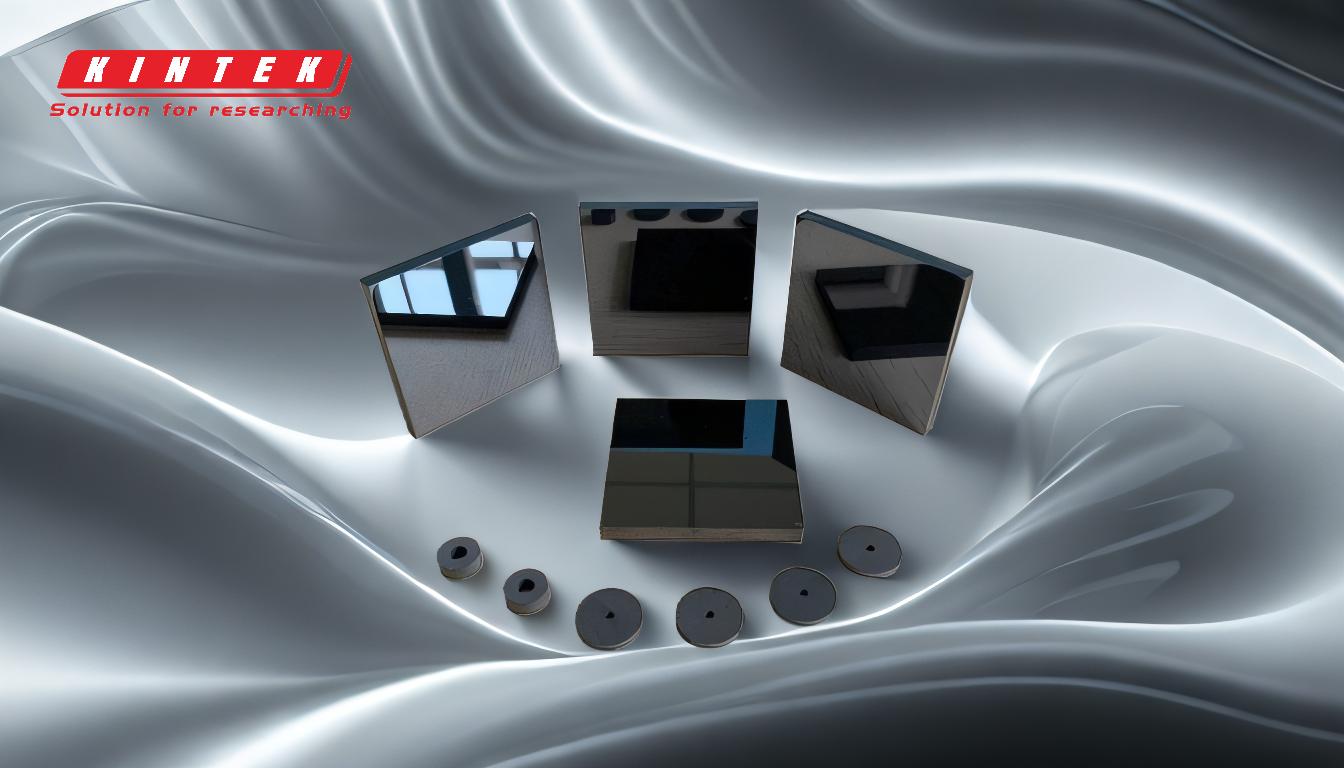
-
Vibration Motor as the Core Component:
- The sieve shaker operates using a vibration motor, typically a YZU vertical vibration motor, which serves as the primary source of mechanical energy.
- The motor drives the upper vibrating plate, generating vibrations that are transmitted to the sieve stack.
- This vibration mechanism ensures consistent and uniform agitation of the sieves, enabling particles to move freely and interact with the mesh openings.
-
Transmission of Vibrations:
- The vibrations produced by the motor are transferred to the sieve stack through the vibrating plate or machine base.
- This ensures that all sieves in the stack receive the same vibrational energy, maintaining uniformity in the separation process.
- The vibrations are designed to be sufficient to move particles but not so intense as to damage the sieves or the material being analyzed.
-
Particle Separation Mechanism:
- As the sieves vibrate, particles smaller than the mesh openings pass through to the lower sieves, while larger particles remain on the current sieve.
- This process is repeated across multiple sieves with progressively smaller mesh sizes, resulting in the stratification of particles by size.
- The final result is a stack of sieves, each containing particles of a specific size range, allowing for accurate determination of the material's particle size distribution.
-
Advantages Over Manual Sieving:
- Efficiency: The sieve shaker automates the sieving process, significantly reducing the time required compared to manual methods.
- Accuracy: Consistent vibrations ensure that particles are evenly distributed and properly separated, minimizing human error.
- Flexibility: The device can accommodate various sieve sizes and materials, making it suitable for a wide range of applications.
-
Applications of Sieve Shakers:
- Sample Size Reduction: Sieve shakers are used to reduce bulk samples into smaller, more manageable fractions for analysis.
- Material Separation: They are essential in industries such as construction, pharmaceuticals, food processing, and mining for separating materials by particle size.
- Particle Analysis: Sieve shakers help determine the particle size distribution of materials, which is critical for quality control and research purposes.
-
Compliance with Industry Standards:
- Many sieve shakers are designed to comply with industry standards, ensuring that the results obtained are reliable and reproducible.
- This compliance is particularly important in industries where precise particle size analysis is required for regulatory or quality assurance purposes.
-
Types of Sieve Shakers:
- Mechanical Sieve Shakers: These use moving parts to oscillate, tap, or agitate the sieve stack, providing a combination of motions to enhance particle separation.
- Vibratory Sieve Shakers: These rely solely on vibrations generated by a motor to achieve particle separation, offering simplicity and ease of use.
-
Key Considerations for Equipment Purchasers:
- Motor Power and Vibration Intensity: Ensure the motor provides sufficient vibration for the specific material being analyzed.
- Sieve Compatibility: Verify that the shaker can accommodate the required sieve sizes and materials.
- Durability and Maintenance: Choose a device made from robust materials that can withstand frequent use and is easy to maintain.
- Compliance with Standards: Select a shaker that meets relevant industry standards to ensure accurate and reliable results.
By understanding these key points, equipment and consumable purchasers can make informed decisions when selecting a sieve shaker that meets their specific needs and ensures optimal performance in particle size analysis and material separation tasks.
Summary Table:
Key Aspect | Details |
---|---|
Core Component | Vibration motor (e.g., YZU vertical motor) drives the sieving process. |
Vibration Transmission | Vibrations are uniformly transferred to the sieve stack for consistent results. |
Particle Separation | Particles are separated by size as they pass through mesh openings. |
Advantages | - Efficiency: Faster than manual sieving. - Accuracy: Reduces human error. - Flexibility: Adaptable to various materials. |
Applications | Sample size reduction, material separation, and particle size analysis. |
Compliance | Meets industry standards for reliable and reproducible results. |
Types | - Mechanical: Oscillates or taps. - Vibratory: Uses motor vibrations. |
Purchasing Considerations | Motor power, sieve compatibility, durability, and compliance with standards. |
Ready to optimize your material analysis? Contact us today to find the perfect sieve shaker for your needs!