Thin film optical coating technology involves the application of ultra-thin layers of materials onto substrates to modify their optical properties. These coatings are used to enhance performance, durability, and functionality in various applications, such as anti-reflective coatings, reflective coatings, UV/IR protection, and more. The technology leverages precise deposition techniques to create layers that are nanometers to micrometers thick, enabling control over light transmission, reflection, and absorption. Applications span industries like optics, electronics, solar energy, and aerospace, making thin film coatings critical for improving efficiency, reducing glare, and protecting surfaces from environmental damage.
Key Points Explained:
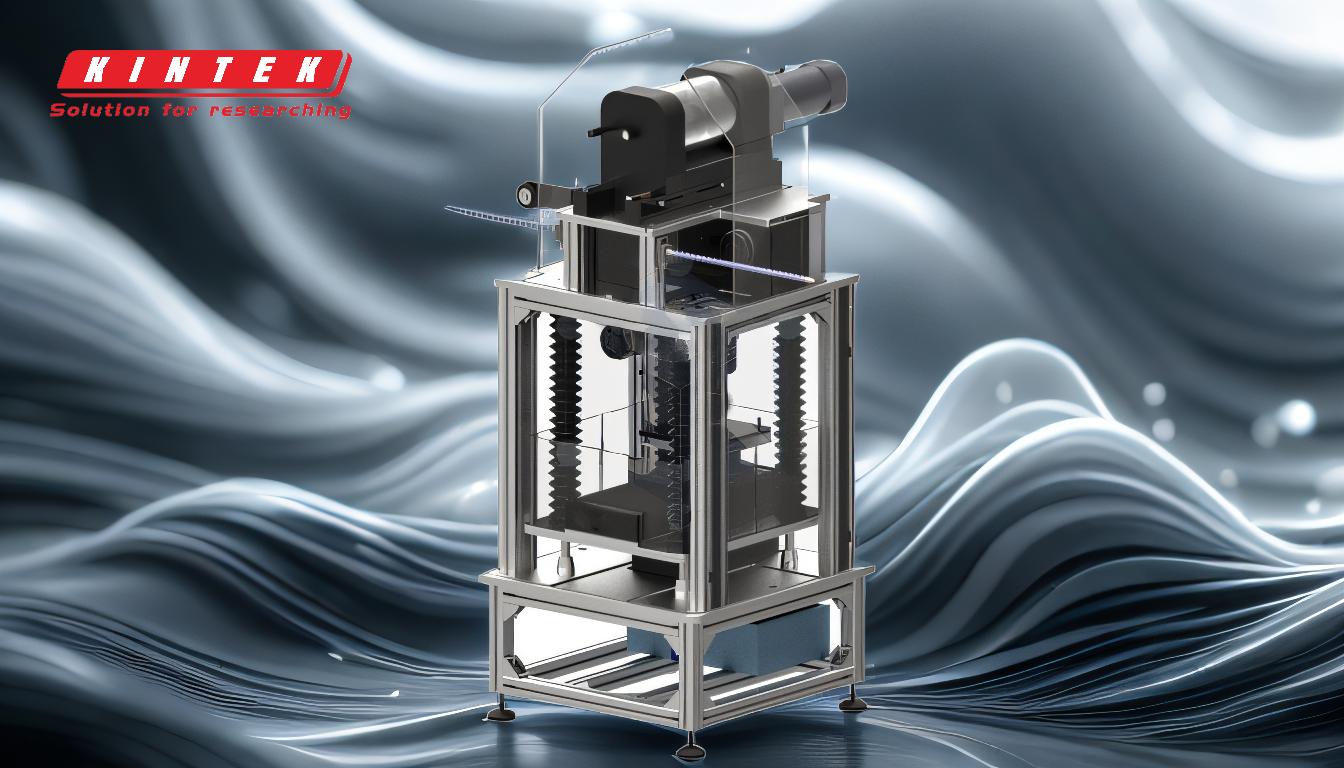
-
Definition and Purpose of Thin Film Optical Coatings:
- Thin film optical coatings are ultra-thin layers of materials applied to substrates to alter their optical properties.
- These coatings are designed to control light behavior, such as reflection, transmission, and absorption, to improve performance in specific applications.
- Common purposes include reducing glare, enhancing light transmission, and protecting surfaces from environmental factors like UV radiation.
-
Applications of Thin Film Optical Coatings:
- Anti-Reflective Coatings: Used in lenses, displays, and solar panels to minimize glare and improve light transmission.
- Reflective Coatings: Applied in mirrors, telescopes, and laser systems to enhance reflectivity.
- Scratch-Resistant Coatings: Protect optical components like camera lenses and eyeglasses from wear and tear.
- UV- and IR-Reflective Coatings: Shield surfaces from harmful ultraviolet and infrared radiation, commonly used in windows and solar panels.
- Self-Cleaning Coatings: Utilize hydrophobic or photocatalytic properties to repel dirt and water, often used in glass and optical devices.
-
Materials and Deposition Techniques:
- Materials used in thin film coatings include metals (e.g., aluminum, silver), dielectrics (e.g., silicon dioxide, titanium dioxide), and organic compounds.
- Deposition techniques include:
- Physical Vapor Deposition (PVD): Evaporates or sputters materials onto the substrate.
- Chemical Vapor Deposition (CVD): Uses chemical reactions to deposit thin films.
- Atomic Layer Deposition (ALD): Provides precise control over film thickness at the atomic level.
- Spin Coating: Commonly used for applying uniform thin films on flat surfaces.
-
Benefits of Thin Film Optical Coatings:
- Enhanced Performance: Improves optical efficiency, such as increasing light transmission in lenses or reflectivity in mirrors.
- Durability: Protects surfaces from scratches, corrosion, and environmental damage.
- Aesthetic and Functional Flexibility: Allows for customization of color, reflectivity, and other optical properties.
- Energy Efficiency: In solar panels, coatings improve light absorption and reduce energy loss.
-
Industries Utilizing Thin Film Optical Coatings:
- Optics and Optoelectronics: Used in lenses, cameras, displays, and sensors.
- Solar Energy: Enhances the efficiency and durability of photovoltaic cells.
- Aerospace and Defense: Protects surfaces and improves optical performance in harsh environments.
- Consumer Electronics: Found in smartphones, smartwatches, and OLED displays.
- Medical Devices: Used in diagnostic equipment and wearable sensors.
-
Challenges and Future Trends:
- Precision and Uniformity: Achieving consistent film thickness and composition across large surfaces remains a challenge.
- Cost-Effectiveness: Advanced deposition techniques can be expensive, limiting widespread adoption.
- Sustainability: Developing eco-friendly materials and processes is a growing focus.
- Innovations: Emerging trends include nanostructured coatings, adaptive optics, and integration with flexible electronics.
By leveraging thin film optical coating technology, industries can achieve significant advancements in performance, durability, and efficiency, making it a cornerstone of modern optical and electronic applications.
Summary Table:
Aspect | Details |
---|---|
Definition | Ultra-thin layers applied to substrates to modify optical properties. |
Applications | Anti-reflective, reflective, scratch-resistant, UV/IR protection, self-cleaning. |
Materials | Metals (aluminum, silver), dielectrics (silicon dioxide, titanium dioxide). |
Deposition Techniques | PVD, CVD, ALD, spin coating. |
Benefits | Enhanced performance, durability, energy efficiency, and customization. |
Industries | Optics, solar energy, aerospace, consumer electronics, medical devices. |
Challenges | Precision, cost-effectiveness, sustainability, and innovation. |
Unlock the potential of thin film optical coatings for your industry—contact us today to learn more!