The typical process pressure for Plasma-Enhanced Chemical Vapor Deposition (PECVD) generally ranges between 0.1 to 10 Torr (approximately 0.01 to 1.3 mbar), though some processes may operate at slightly lower or higher pressures depending on specific requirements. This low-pressure environment is crucial for maintaining plasma stability, promoting film uniformity, and minimizing substrate damage. Factors such as plate spacing, RF power supply frequency, and gas pressure significantly influence the quality of the deposition process. Additionally, pressures outside this range (e.g., atmospheric pressure CVD) are possible but require specialized equipment and conditions.
Key Points Explained:
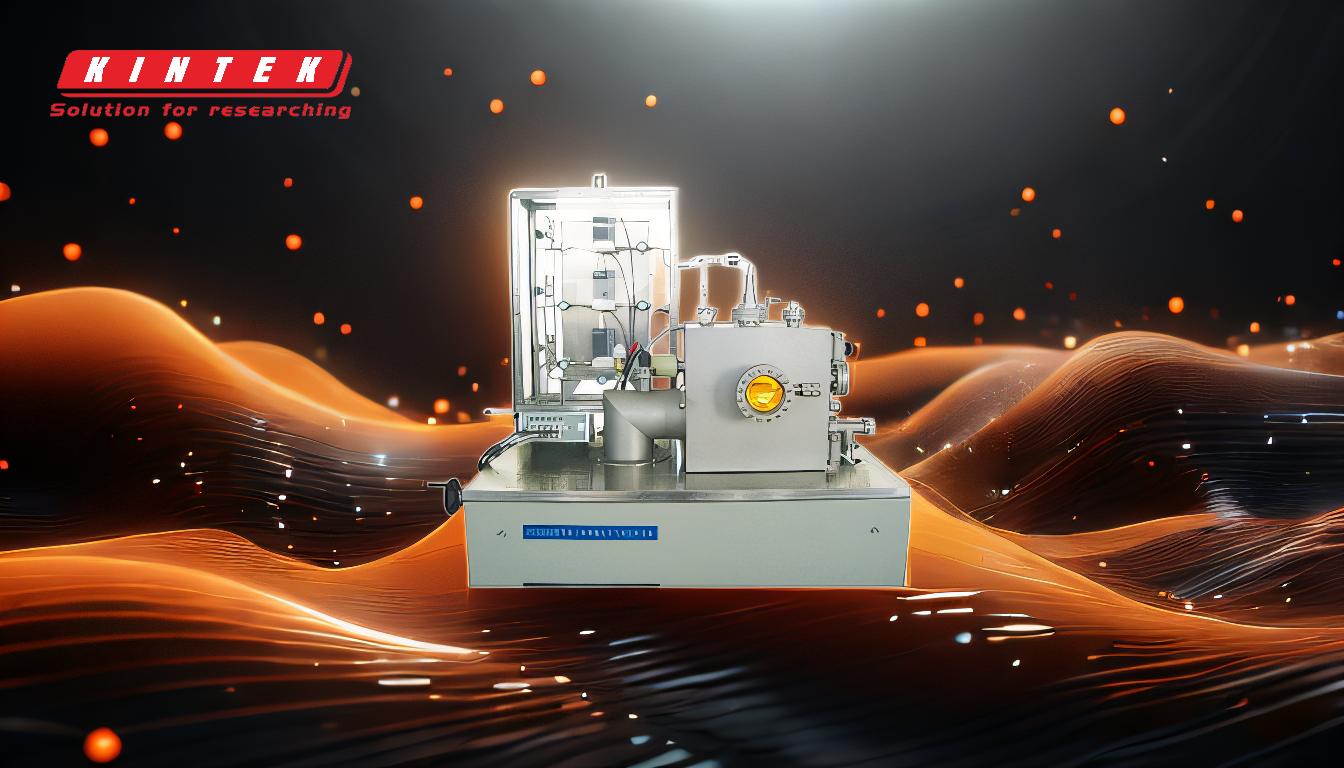
-
Typical Pressure Range for PECVD:
- PECVD systems typically operate in the range of 0.1 to 10 Torr (approximately 0.01 to 1.3 mbar). This range ensures optimal plasma conditions for film deposition.
- Some references suggest a narrower range of 1 to 2 Torr for standard processes, with temperatures between 200°C and 400°C.
- Lower pressures (e.g., 50 mtorr to 5 torr) are also used, depending on the specific application and equipment configuration.
-
Importance of Low Pressure:
- Low pressure reduces gas scattering, which improves film uniformity and coverage, especially on complex or stepped surfaces.
- It also minimizes substrate damage by lowering the energy of ion bombardment, making it suitable for temperature-sensitive materials.
- Low-pressure environments facilitate chemical reactions at lower temperatures compared to thermal CVD, enabling the deposition of a wider range of materials.
-
Effects of Pressure on Film Quality:
-
High Pressure:
- Increases the reaction rate due to higher gas concentration.
- Reduces the mean free path of particles, which can hinder film coverage on steps and complex geometries.
- Enhances plasma polymerization, potentially leading to irregular growth networks and increased defects.
-
Low Pressure:
- Decreases film denseness, which can result in needle-like defects.
- Reduces the reaction rate, but improves uniformity and step coverage.
-
High Pressure:
-
Factors Influencing Pressure Selection:
- Plate Spacing and Chamber Dimensions: These affect the ignition voltage and deposition uniformity. Smaller spacing may require lower pressures to maintain plasma stability.
- RF Power Supply Frequency: Higher frequencies (e.g., 40 MHz) can influence ion bombardment and film density, often requiring precise pressure control.
- Gas Pressure Stability: Maintaining consistent pressure is critical for achieving uniform film properties and minimizing defects.
-
Specialized PECVD Processes:
- Atmospheric Pressure CVD: Some PECVD systems operate at atmospheric pressure using specialized dielectric barrier discharge sources. These systems are less common and require advanced equipment to maintain plasma stability.
- Low-Temperature PECVD: Processes at temperatures below 200°C are possible, often used for temperature-sensitive substrates like polymers or flexible electronics.
-
Practical Considerations for Equipment Purchasers:
- Compatibility: Ensure the system can operate within the required pressure range for your specific applications.
- Control Mechanisms: Look for systems with precise pressure control and monitoring capabilities to maintain process stability.
- Scalability: Consider whether the system can handle variations in pressure for different materials or deposition requirements.
By understanding these key points, equipment and consumable purchasers can make informed decisions about PECVD systems and processes, ensuring optimal performance and film quality for their specific applications.
Summary Table:
Aspect | Details |
---|---|
Typical Pressure Range | 0.1 to 10 Torr (0.01 to 1.3 mbar) |
Importance of Low Pressure | Reduces gas scattering, minimizes substrate damage, enables lower-temperature reactions |
Effects of High Pressure | Increases reaction rate, reduces mean free path, enhances plasma polymerization |
Effects of Low Pressure | Improves uniformity, reduces denseness, may cause needle-like defects |
Key Influencing Factors | Plate spacing, RF power frequency, gas pressure stability |
Specialized Processes | Atmospheric pressure CVD, low-temperature PECVD |
Practical Considerations | Compatibility, control mechanisms, scalability |
Looking to optimize your PECVD process? Contact our experts today for tailored solutions!