PVD (Physical Vapor Deposition) finishing utilizes a wide range of materials, both inorganic and organic, to create coatings with specific functional and aesthetic properties. The materials used in PVD coatings include metals, alloys, ceramics, and specialized compounds like carbides, nitrides, silicides, and borides. Common examples include titanium, zirconium, aluminum, gold, and diamond-like carbon (DLC). These coatings are applied to substrates such as stainless steel, titanium, glass, plastics, and ceramics, often after pre-treatment processes like electroplating. The choice of materials depends on the desired properties, such as hardness, conductivity, or corrosion resistance, and the specific application, whether in aerospace, automotive, medical devices, or decorative industries.
Key Points Explained:
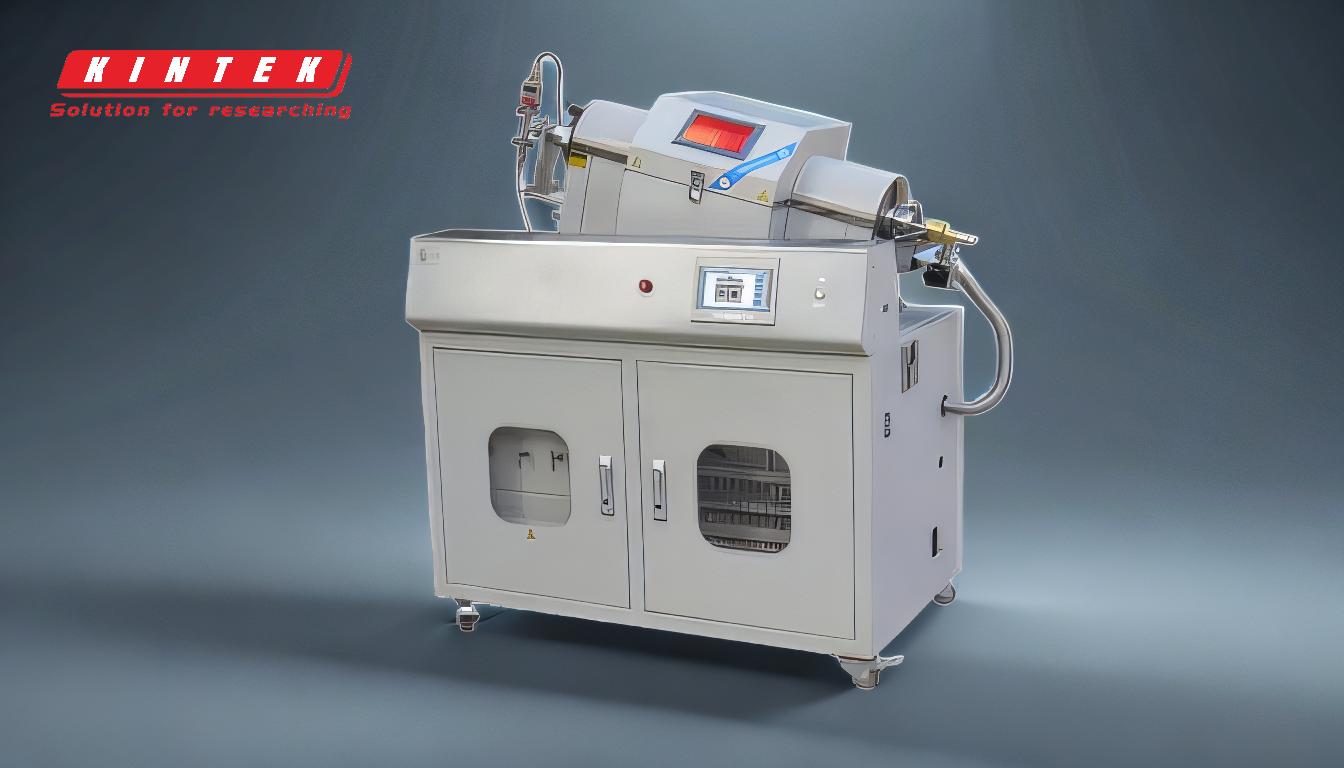
-
Types of Materials Used in PVD Coatings:
- Metals and Alloys: Titanium, zirconium, aluminum, stainless steel, copper, and gold are commonly used. These materials provide properties like durability, conductivity, and aesthetic appeal.
- Ceramics: Materials like silicon oxide and aluminum chromium (AlCr) are used for their hardness and wear resistance.
- Specialized Compounds: Carbides (e.g., TiC), nitrides (e.g., TiN, Cr2N), silicides, and borides are employed for specific performance requirements, such as high-temperature resistance or improved tool life.
- Organic Materials: A limited range of organic materials can also be used in PVD coatings, though they are less common compared to inorganic materials.
-
Common PVD Coating Materials and Their Applications:
- Gold: Used in aerospace electronics and decorative applications like watches and jewelry.
- Titanium Nitride (TiN): Widely used for decorative purposes (e.g., phones, glasses) and to enhance the durability of tools and hardware.
- Zinc Tin (ZnSn): Applied as an optical coating in low-emissivity (low-e) windows and glass.
- Diamond-like Carbon (DLC): Provides exceptional hardness and low friction, making it suitable for automotive and industrial components.
- Indium Tin Oxide (ITO): Used in LCDs, plasma displays, and touch panels due to its high conductivity and transparency.
-
Substrates Suitable for PVD Coatings:
- Metals: Stainless steel (e.g., 303, 440C, 17-4), titanium alloys, and tool steels are commonly coated. Aluminum is rarely used due to its low melting point.
- Non-Metals: Glass, ceramics, plastics (e.g., ABS), and nylon can also be coated, provided they are vacuum-compatible.
- Pre-Treatment: Substrates are often pre-treated with organic coatings or electroplated with nickel and chromium to improve adhesion and durability.
-
Industry-Specific Applications:
- Aerospace: Gold coatings for electronics and specialized compounds for high-temperature resistance.
- Automotive: DLC and TiN coatings for wear resistance and improved performance of engine components.
- Medical Devices: Stainless steel and titanium alloys are coated for biocompatibility and corrosion resistance.
- Decorative: TiN and gold coatings are used in jewelry, watches, and consumer electronics for aesthetic appeal.
-
Factors Influencing Material Selection:
- Performance Requirements: Hardness, wear resistance, conductivity, and corrosion resistance dictate the choice of materials.
- Substrate Compatibility: The material must withstand the PVD process, which involves heating to high temperatures (up to 800°F).
- Application Environment: The operating conditions (e.g., high temperature, exposure to chemicals) influence the selection of coating materials.
-
Advantages of PVD Coatings:
- Versatility: PVD can deposit a wide range of materials onto various substrates.
- Durability: Coatings are highly resistant to wear, corrosion, and high temperatures.
- Aesthetic Appeal: Materials like gold and TiN provide decorative finishes.
- Environmental Friendliness: PVD is a cleaner process compared to traditional coating methods, with minimal waste and emissions.
In summary, PVD finishing employs a diverse array of materials, each selected for its unique properties and suitability for specific applications. The process is highly versatile, enabling the creation of durable, functional, and aesthetically pleasing coatings across numerous industries.
Summary Table:
Category | Materials | Applications |
---|---|---|
Metals & Alloys | Titanium, zirconium, aluminum, stainless steel, copper, gold | Durability, conductivity, aesthetic appeal |
Ceramics | Silicon oxide, aluminum chromium (AlCr) | Hardness, wear resistance |
Specialized Compounds | Carbides (TiC), nitrides (TiN, Cr2N), silicides, borides | High-temperature resistance, improved tool life |
Organic Materials | Limited range of organic materials | Less common, niche applications |
Common Applications | Gold (aerospace, decorative), TiN (tools, hardware), DLC (automotive) | Aerospace, automotive, medical devices, decorative industries |
Learn how PVD coatings can enhance your products—contact us today for expert advice!