Planetary ball mills are highly effective for grinding and reducing particle sizes, particularly for small samples. They are capable of producing nanoparticles, with typical particle sizes ranging from 1 nanometer to 100 nanometers. The size of the particles can be influenced by factors such as the speed of rotation of the balls, the milling time, and the power applied. For specific applications, planetary ball mills can produce nano powders in the range of 2 to 20 nanometers, making them suitable for advanced material synthesis and research.
Key Points Explained:
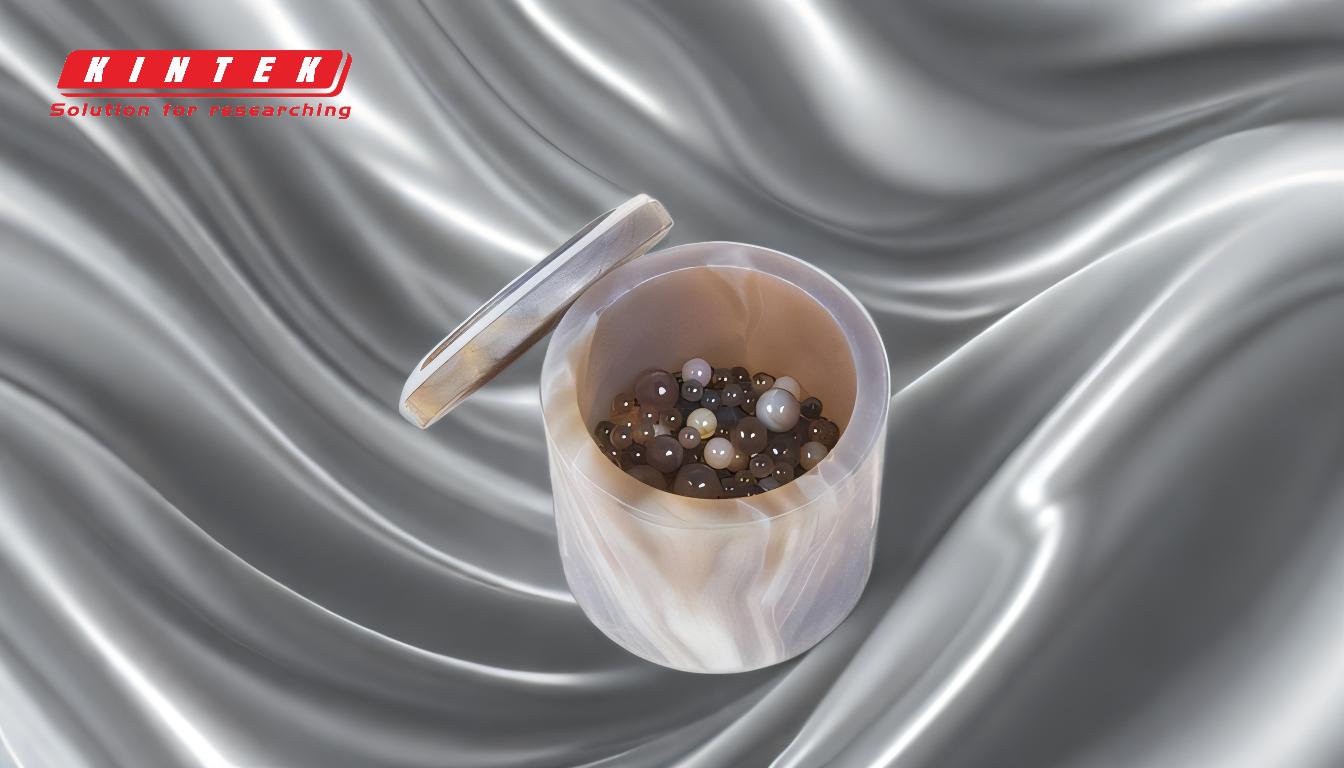
-
Particle Size Range:
- Planetary ball mills are designed to grind materials into very fine particles, typically in the nanometer range.
- The size of nanoparticles produced by planetary ball mills generally falls between 1 nanometer and 100 nanometers.
- For specific applications, such as advanced material synthesis, planetary ball mills can produce nano powders in the range of 2 to 20 nanometers.
-
Factors Influencing Particle Size:
- Speed of Rotation: The speed at which the balls rotate within the mill significantly impacts the particle size. Higher rotation speeds can lead to finer particles due to increased collision energy.
- Milling Time: Longer milling times generally result in smaller particle sizes as the material is subjected to more grinding action.
- Power Applied: The power settings of the mill can also affect the final particle size. Increased power can lead to finer particles, while reduced power may result in larger particles.
-
Comparison with Other Milling Techniques:
- Jet Mills: Jet mills typically achieve particle sizes in the 1- to 10-micron range, known as micronization. For some materials, particles as small as 200 nanometers can be achieved by increasing power and milling time.
- Ball Mills: Planetary ball mills, on the other hand, are more suited for producing nanoparticles, with typical sizes ranging from 1 nanometer to 100 nanometers.
-
Advantages of Planetary Ball Mills:
- Multi-Dimensional Motion: The unique multi-dimensional motion of planetary ball mills ensures that small particles are more fully collided and ground, allowing for faster achievement of the required grinding fineness.
- Suitability for Small Samples: Planetary ball mills are particularly suitable for grinding small particle samples, making them ideal for laboratory and research applications.
-
Applications:
- Material Synthesis: Planetary ball mills are widely used in the synthesis of advanced materials, including nanoparticles, due to their ability to produce very fine and uniform particle sizes.
- Research and Development: They are also commonly used in research and development settings where precise control over particle size is crucial.
In summary, planetary ball mills are versatile and efficient tools for producing nanoparticles, with typical particle sizes ranging from 1 nanometer to 100 nanometers. The ability to control factors such as rotation speed, milling time, and power allows for precise adjustment of particle size, making them suitable for a wide range of applications in material synthesis and research.
Summary Table:
Aspect | Details |
---|---|
Particle Size Range | 1 nanometer to 100 nanometers; 2-20 nm for advanced applications. |
Key Factors | Speed of rotation, milling time, and power applied. |
Advantages | Multi-dimensional motion, suitability for small samples, precise control. |
Applications | Material synthesis, research, and development. |
Comparison with Jet Mills | Jet mills produce 1-10 micron particles; planetary ball mills excel in nanoscale grinding. |
Unlock the potential of nanoscale materials—contact our experts today to find the right planetary ball mill for your needs!