Compression molding is a manufacturing process where a material, typically a thermosetting polymer, is placed in a heated mold cavity and compressed to take the shape of the mold. For shallow or flat parts, such as control panel dashboards and ashtrays, a flash-type compression mold is commonly used. This type of mold allows excess material (flash) to escape during the compression process, which is later trimmed off to achieve the final product. The design of flash-type molds ensures uniform pressure distribution and precise shaping of flat or shallow components.
Key Points Explained:
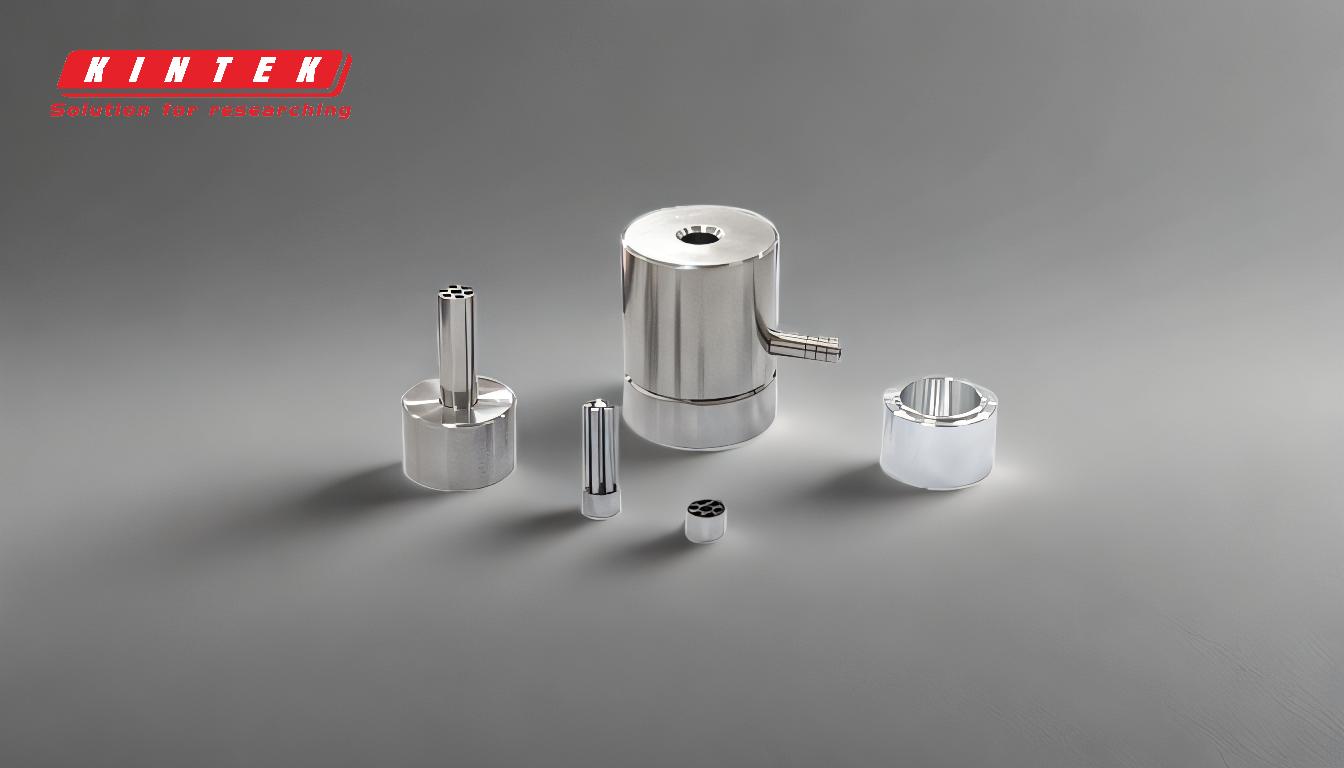
-
Flash-Type Compression Molds:
- Flash-type molds are specifically designed for shallow or flat parts.
- During the molding process, excess material (flash) is squeezed out of the mold cavity.
- The flash is later trimmed off to produce a clean and precise final product.
-
Applications of Flash-Type Molds:
- These molds are ideal for manufacturing components like control panel dashboards and ashtrays, which are typically flat or shallow in design.
- The ability to handle excess material makes flash-type molds suitable for parts that require high dimensional accuracy.
-
Advantages of Flash-Type Molds:
- Uniform Pressure Distribution: The design ensures even pressure across the mold, which is critical for maintaining the integrity of flat or shallow parts.
- Material Efficiency: Excess material is minimized, and any flash produced can be recycled or reused.
- Precision: The trimming process ensures a high level of precision and a clean finish on the final product.
-
Considerations for Equipment and Consumable Purchasers:
- Mold Design: Ensure the mold is designed to accommodate the specific dimensions and geometry of the part.
- Material Selection: Choose materials that are compatible with the compression molding process and the intended application.
- Trimming Equipment: Invest in reliable trimming tools to efficiently remove flash and achieve a high-quality finish.
- Cost Efficiency: Evaluate the balance between mold cost, material waste, and production efficiency to optimize the overall process.
By understanding the role of flash-type compression molds in producing shallow or flat parts, purchasers can make informed decisions about mold design, material selection, and process optimization to achieve high-quality results.
Summary Table:
Key Aspect | Details |
---|---|
Design Purpose | Specifically for shallow or flat parts (e.g., dashboards, ashtrays). |
Excess Material Handling | Excess material (flash) escapes during compression and is trimmed later. |
Applications | Ideal for parts requiring high dimensional accuracy and clean finishes. |
Advantages | - Uniform pressure distribution - Material efficiency - High precision |
Purchasing Considerations | - Mold design - Material selection - Trimming tools - Cost efficiency |
Optimize your compression molding process with flash-type molds—contact our experts today!