When deciding between a rod mill and a ball mill, the choice depends on the specific application, material properties, and desired output. Rod mills are better suited for coarse grinding and are often used in primary grinding stages, particularly for brittle materials. They produce a more uniform particle size with fewer fines. Ball mills, on the other hand, are versatile and excel in fine grinding, making them ideal for secondary and tertiary grinding stages. They are more energy-efficient for finer grinding but may produce more fines. The decision should consider factors like material hardness, required particle size, energy consumption, and operational costs.
Key Points Explained:
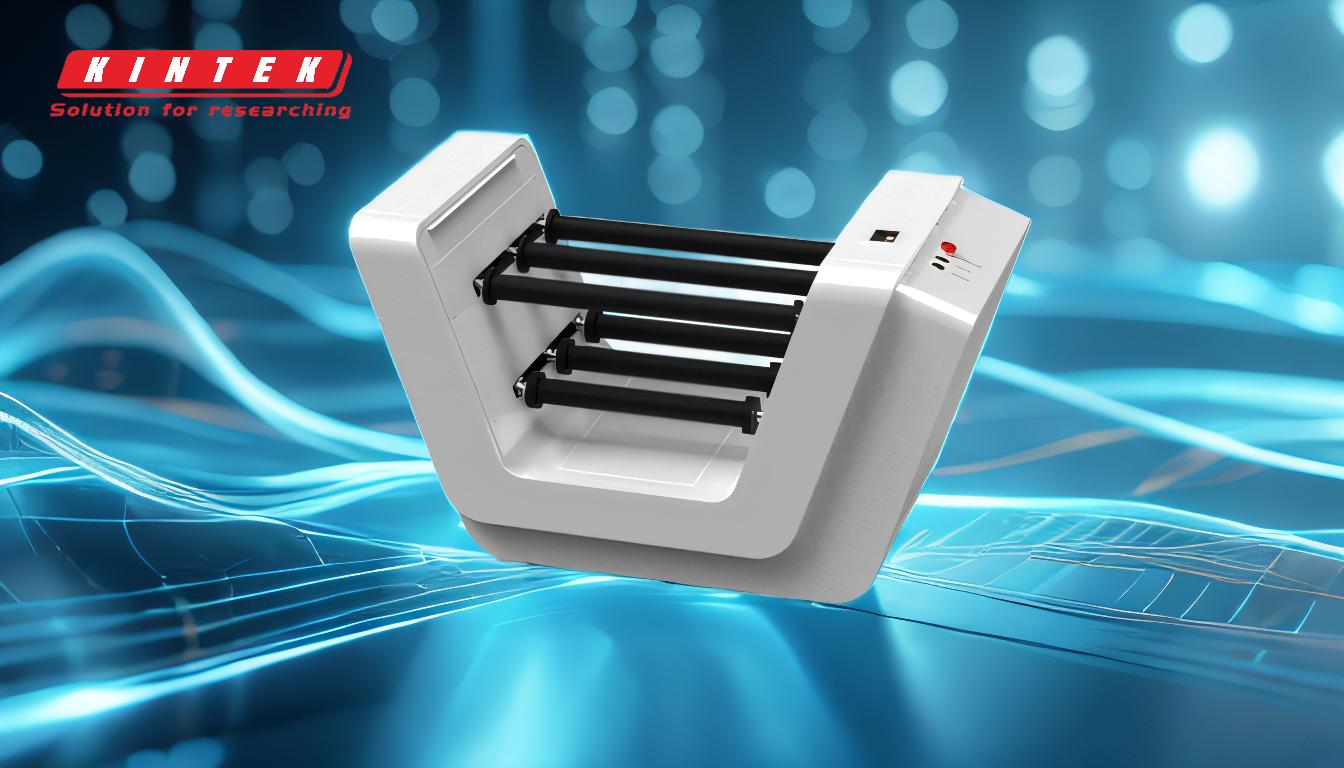
-
Primary Function and Applications:
- Rod Mills: Primarily used for coarse grinding in the primary stage. They are ideal for grinding brittle materials like coal, limestone, and phosphate. Rod mills are also suitable for wet grinding processes where a uniform particle size is required.
- Ball Mills: Versatile and used for both coarse and fine grinding. They are commonly employed in secondary and tertiary grinding stages, especially for materials requiring fine grinding, such as cement, silicates, and ceramics.
-
Particle Size Distribution:
- Rod Mills: Produce a more uniform particle size with fewer fines. This is because the grinding action in rod mills is more linear and less impact-based, leading to less over-grinding.
- Ball Mills: Tend to produce a wider range of particle sizes, including more fines. The impact and attrition forces in ball mills can lead to over-grinding, especially in finer grinding applications.
-
Energy Efficiency:
- Rod Mills: Generally more energy-efficient for coarse grinding. The grinding media (rods) have a larger surface area, which allows for more efficient grinding of larger particles.
- Ball Mills: More energy-efficient for fine grinding. The smaller grinding media (balls) allow for more effective grinding of finer particles, but this comes at the cost of higher energy consumption for coarser grinding.
-
Operational Considerations:
- Rod Mills: Require less maintenance and are easier to operate. The rods are less prone to wear and tear compared to balls, reducing downtime and maintenance costs.
- Ball Mills: May require more maintenance due to the higher wear rate of the balls. However, they offer greater flexibility in terms of grinding media and can be adapted to a wider range of materials and grinding conditions.
-
Cost Implications:
- Rod Mills: Generally lower initial cost and operational cost for coarse grinding applications. The lower wear rate of rods also contributes to reduced operational expenses.
- Ball Mills: Higher initial and operational costs, especially for fine grinding applications. However, the versatility and efficiency of ball mills can justify the higher costs in many industrial applications.
-
Material Properties:
- Rod Mills: Best suited for materials that are brittle and require coarse grinding. The linear grinding action of rods is less likely to cause excessive wear on the mill itself.
- Ball Mills: Suitable for a wide range of materials, including those that require fine grinding. The impact and attrition forces in ball mills can handle harder materials more effectively.
-
Environmental Impact:
- Rod Mills: Generally have a lower environmental impact due to lower energy consumption and reduced wear on grinding media.
- Ball Mills: May have a higher environmental impact due to higher energy consumption and increased wear on grinding media, leading to more frequent replacements.
In conclusion, the choice between a rod mill and a ball mill depends on the specific requirements of the grinding process, including the material properties, desired particle size, energy efficiency, and cost considerations. Rod mills are better for coarse grinding and uniform particle size, while ball mills are more versatile and efficient for fine grinding.
Summary Table:
Aspect | Rod Mill | Ball Mill |
---|---|---|
Primary Function | Coarse grinding, ideal for brittle materials like coal, limestone, phosphate. | Versatile, used for both coarse and fine grinding, e.g., cement, silicates. |
Particle Size | Uniform particle size with fewer fines. | Wider range of particle sizes, including more fines. |
Energy Efficiency | More efficient for coarse grinding. | More efficient for fine grinding. |
Maintenance | Less maintenance, rods are less prone to wear. | Higher maintenance due to wear on balls. |
Cost | Lower initial and operational costs for coarse grinding. | Higher initial and operational costs, especially for fine grinding. |
Material Suitability | Best for brittle materials requiring coarse grinding. | Suitable for a wide range of materials, including fine grinding applications. |
Need help choosing the right mill for your application? Contact our experts today for personalized advice!