Atomic Layer Deposition (ALD) achieves conformal deposition due to its unique self-limiting, sequential reaction mechanism. Unlike traditional deposition methods, ALD alternates between two or more precursor gases, which react with the substrate surface in a controlled, layer-by-layer fashion. This process ensures that each precursor fully saturates the surface before being purged, eliminating line-of-sight dependencies and enabling uniform coverage even on highly complex or high-aspect-ratio structures. The self-terminating nature of the reactions, combined with precise control over film thickness and stoichiometry, allows ALD to produce highly conformal films with excellent step coverage, making it ideal for applications requiring uniform coatings on intricate geometries.
Key Points Explained:
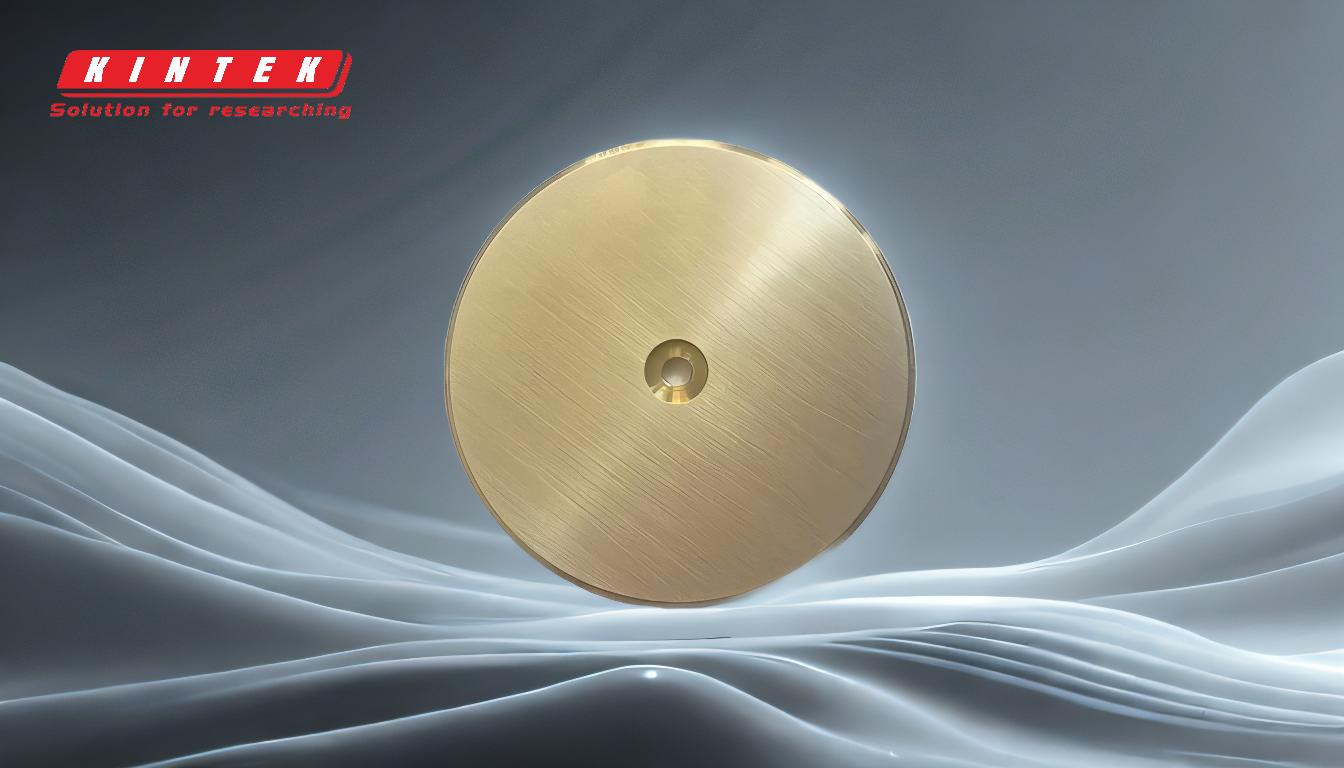
-
Self-Limiting Reaction Mechanism
- ALD relies on sequential, self-limiting chemical reactions between gas-phase precursors and the substrate surface.
- Each precursor is introduced separately, allowing it to react completely with the surface until all reactive sites are occupied.
- Once the surface is saturated, the reaction stops, ensuring a uniform monolayer is formed. This self-limiting behavior is key to achieving conformal deposition.
-
Alternating Precursor Pulses and Purge Steps
- ALD alternates between two or more precursor gases, separated by inert gas purging.
- The purge steps remove excess precursors and reaction by-products, preventing gas-phase reactions and ensuring only surface reactions occur.
- This sequential pulsing and purging process allows for precise control over film growth, layer by layer, resulting in highly conformal coatings.
-
No Line-of-Sight Dependency
- Unlike traditional deposition methods such as physical vapor deposition (PVD), ALD does not require a direct line of sight between the precursor source and the substrate.
- The precursors diffuse into all areas of the substrate, including high-aspect-ratio features, trenches, and curved surfaces, ensuring uniform coverage.
-
Conformality on Complex Geometries
- ALD's ability to deposit films conformally is particularly advantageous for substrates with intricate geometries, such as MEMS devices, medical implants, and semiconductor structures.
- The process can achieve excellent step coverage, even on features with aspect ratios as high as 2000:1, making it suitable for advanced applications in nanotechnology and microelectronics.
-
Precise Thickness Control and Uniformity
- Film thickness in ALD is determined by the number of deposition cycles, with each cycle adding a predictable and consistent layer.
- This precision allows for nanometer-level control over film thickness, ensuring uniformity across the entire substrate.
-
Wide Range of Materials and Applications
- ALD can deposit a variety of materials, including oxides, nitrides, metals, and polymers, making it versatile for different applications.
- Its conformal deposition capability is utilized in fields such as semiconductor engineering, catalysis, energy storage, and medical device coatings.
-
Low Defect Density and High Reproducibility
- The self-limiting nature of ALD minimizes defects and ensures high reproducibility.
- The process is scalable and can produce films with consistent properties over large areas, making it suitable for industrial applications.
-
Amorphous or Crystalline Film Formation
- Depending on the substrate and process temperature, ALD can produce either amorphous or crystalline films.
- This flexibility allows for tailoring film properties to meet specific application requirements.
-
Effective Reduction of Surface Reactions
- In applications like battery electrodes, ALD coatings reduce unwanted surface reactions between the electrode and electrolyte.
- The conformal nature of the coating ensures complete coverage, enhancing electrochemical performance and longevity.
-
Challenges and Considerations
- While ALD offers exceptional conformality, it is a relatively slow process compared to other deposition techniques.
- The need for highly pure substrates and the complexity of precursor chemistry can increase costs and operational challenges.
In summary, ALD's conformal deposition capability stems from its self-limiting, sequential reaction mechanism, alternating precursor pulses, and lack of line-of-sight dependency. These features enable uniform, precise, and defect-free coatings on complex geometries, making ALD a powerful tool for advanced applications in nanotechnology, microelectronics, and beyond.
Summary Table:
Key Feature | Description |
---|---|
Self-Limiting Reaction Mechanism | Ensures uniform monolayer formation through sequential, self-terminating reactions. |
Alternating Precursor Pulses | Precise control over film growth via alternating precursor pulses and purge steps. |
No Line-of-Sight Dependency | Uniform coverage on high-aspect-ratio structures without direct precursor access. |
Conformality on Complex Geometries | Ideal for MEMS, medical implants, and semiconductor structures with intricate designs. |
Precise Thickness Control | Nanometer-level accuracy in film thickness for consistent, uniform coatings. |
Wide Range of Materials | Deposits oxides, nitrides, metals, and polymers for versatile applications. |
Low Defect Density | Minimizes defects and ensures high reproducibility for industrial scalability. |
Amorphous or Crystalline Films | Tailors film properties based on substrate and temperature requirements. |
Reduced Surface Reactions | Enhances electrochemical performance in applications like battery electrodes. |
Challenges | Slower process and higher costs due to precursor chemistry and substrate purity. |
Learn how ALD can revolutionize your thin-film applications—contact our experts today!