Ball mills are widely used in various industries for grinding and mixing materials, and the size of the balls used in these mills plays a critical role in determining their performance. The choice of ball size is influenced by the size of the particles being processed, as larger balls are more effective for breaking down large particles, while smaller balls are better suited for fine particles. This ensures efficient grinding, optimal energy consumption, and desired particle size distribution. Understanding the relationship between ball size and particle size is essential for maximizing mill performance and achieving the desired grinding outcomes.
Key Points Explained:
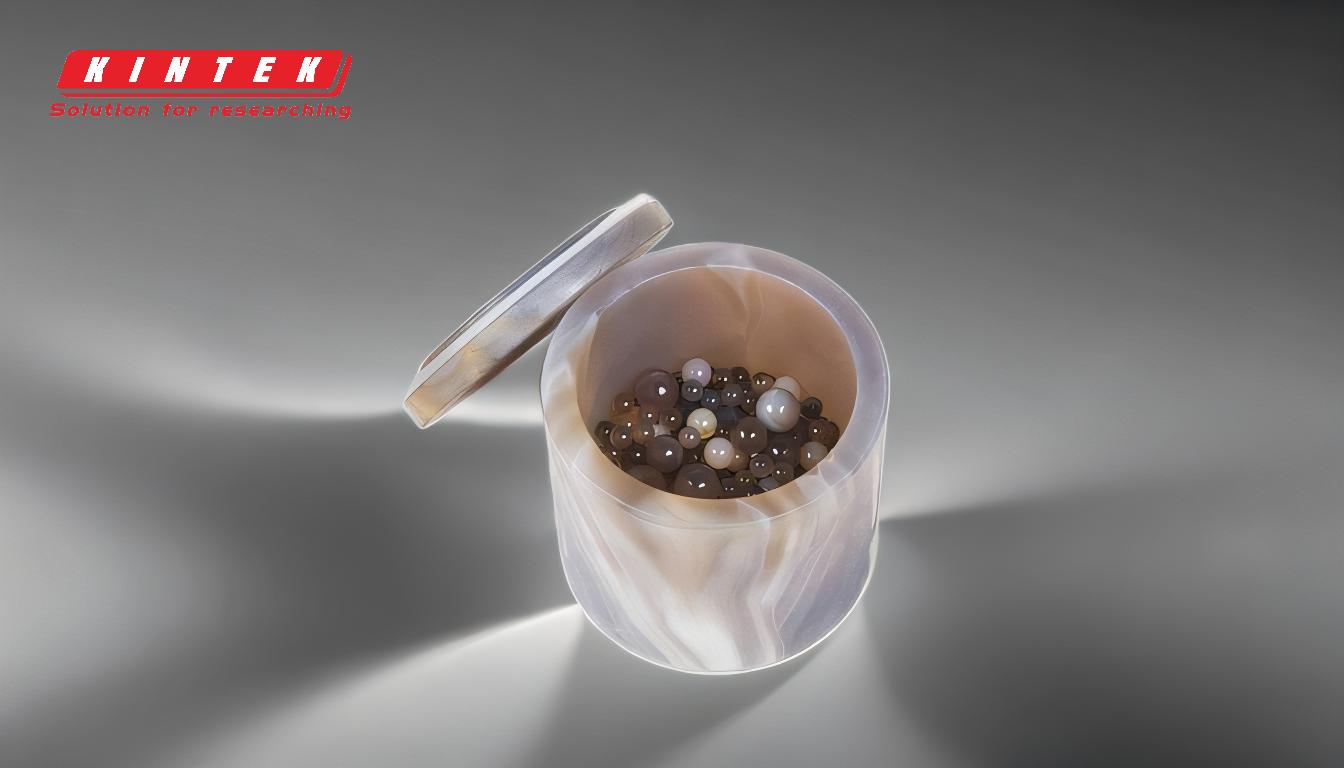
-
Impact of Ball Size on Grinding Efficiency:
- Larger Balls: Larger balls are more effective in breaking down large particles due to their greater mass and kinetic energy. When large particles are fed into the mill, larger balls can deliver the necessary force to fracture them effectively.
- Smaller Balls: Smaller balls are better suited for grinding fine particles. Their smaller size allows for more frequent collisions with fine particles, leading to a more uniform and precise grinding process. This is particularly important for achieving the desired fineness in the final product.
-
Energy Consumption and Ball Size:
- Larger Balls: While larger balls are effective for coarse grinding, they require more energy to operate due to their higher mass. This can lead to increased energy consumption, which may not be efficient for fine grinding tasks.
- Smaller Balls: Smaller balls consume less energy compared to larger balls, making them more energy-efficient for fine grinding. However, they may not be as effective for breaking down large particles, which could lead to inefficiencies in the grinding process if not properly matched to the particle size.
-
Particle Size Distribution:
- Larger Balls: The use of larger balls can result in a broader particle size distribution, as they are more effective at breaking down large particles but may not be as precise in grinding fine particles.
- Smaller Balls: Smaller balls contribute to a more uniform particle size distribution, as they are better at grinding fine particles to a consistent size. This is crucial for applications where a narrow particle size distribution is required.
-
Optimal Ball Size Selection:
- Matching Ball Size to Particle Size: The selection of ball size should be based on the size of the particles being processed. For coarse grinding, larger balls are preferred, while for fine grinding, smaller balls are more effective. This ensures that the grinding process is both efficient and effective.
- Balancing Ball Size and Mill Performance: It is important to balance the size of the balls with the overall performance of the mill. Using a mixture of different ball sizes can sometimes be beneficial, as it allows for both coarse and fine grinding within the same mill. This approach can optimize the grinding process and improve overall mill performance.
-
Practical Considerations:
- Mill Design and Operation: The design and operation of the ball mill also play a role in determining the optimal ball size. Factors such as mill speed, filling ratio, and the type of material being ground should be considered when selecting ball sizes.
- Cost and Maintenance: The cost of balls and the maintenance requirements of the mill should also be taken into account. Larger balls may be more expensive and could lead to higher wear and tear on the mill, while smaller balls may require more frequent replacement due to their smaller size.
In conclusion, the use of different size balls in ball mills is essential for achieving efficient and effective grinding. By matching the ball size to the particle size, optimizing energy consumption, and ensuring a uniform particle size distribution, operators can maximize the performance of their ball mills and achieve the desired grinding outcomes.
Summary Table:
Aspect | Larger Balls | Smaller Balls |
---|---|---|
Grinding Efficiency | Effective for breaking down large particles due to greater mass and kinetic energy. | Better suited for fine grinding, ensuring uniform and precise particle size. |
Energy Consumption | Higher energy consumption due to greater mass. | More energy-efficient for fine grinding tasks. |
Particle Size Distribution | Broader distribution; effective for coarse grinding but less precise for fine particles. | Uniform distribution; ideal for achieving narrow particle size requirements. |
Optimal Use Case | Coarse grinding of large particles. | Fine grinding of small particles. |
Practical Considerations | Higher cost and wear on mill components. | May require frequent replacement due to smaller size. |
Maximize your ball mill's performance—contact our experts today for tailored solutions!