Sputtering is a critical process in thin-film deposition, particularly in industries requiring precise, uniform, and high-quality coatings. It involves bombarding a target material with high-energy ions, causing atoms to eject and deposit onto a substrate. This method is widely used in applications such as semiconductor manufacturing, optics, and scanning electron microscopy (SEM). Sputtering ensures uniform film thickness, strong atomic-level bonding, and the ability to coat complex geometries. It is also valued for its ability to deposit a wide range of materials, including metals, ceramics, and plastics, at lower temperatures, making it suitable for temperature-sensitive substrates.
Key Points Explained:
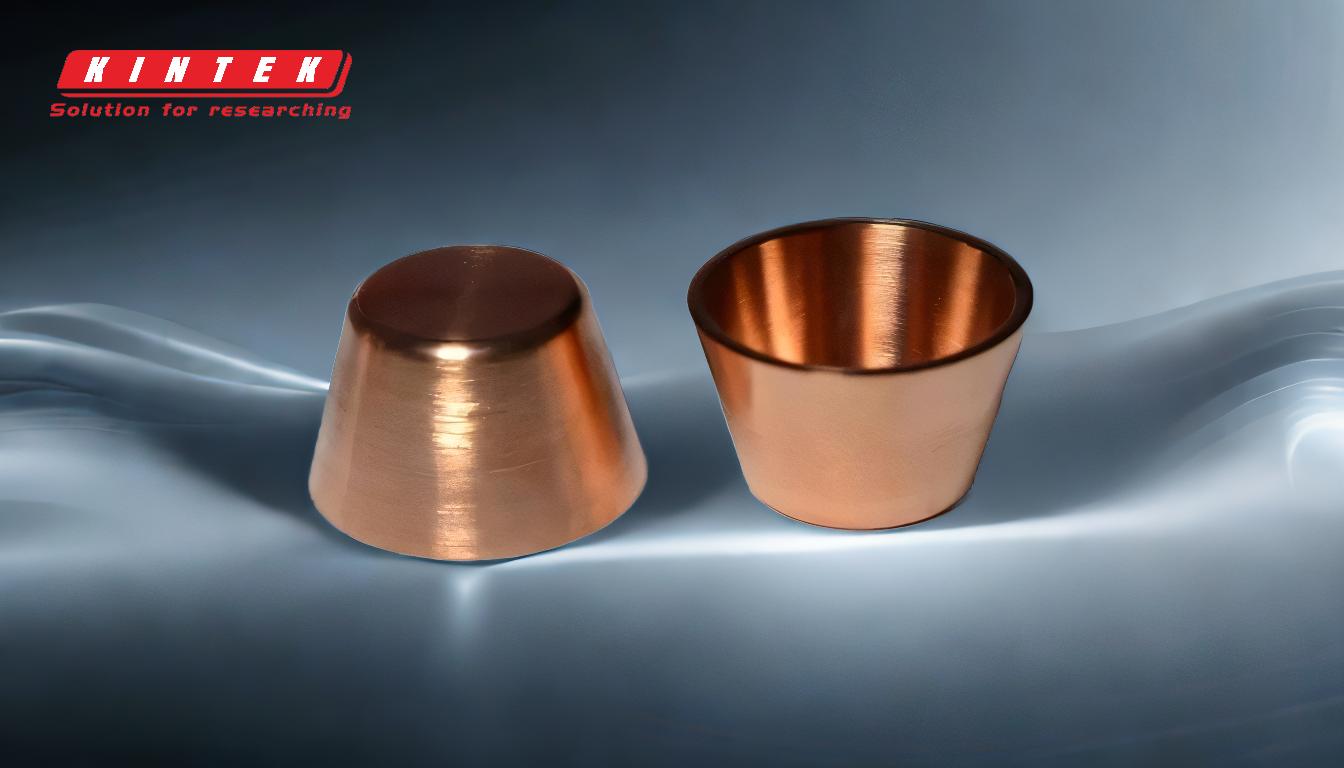
-
Uniform Thin-Film Deposition:
- Sputtering enables the creation of thin, uniform coatings, which are essential for applications like semiconductor devices and optical coatings. The process ensures consistent thickness across the substrate, even on complex, three-dimensional surfaces.
- The momentum transfer mechanism ensures that ejected target atoms are evenly distributed, resulting in a dense and uniform film.
-
Strong Atomic-Level Bonding:
- The high-energy ions used in sputtering create strong atomic-level bonds between the deposited material and the substrate. This results in durable coatings with excellent adhesion, which is crucial for applications requiring long-term reliability, such as protective coatings in aerospace or medical devices.
-
Versatility in Material Deposition:
- Sputtering can deposit a wide range of materials, including metals, ceramics, and plastics. This versatility makes it suitable for diverse industries, from electronics to decorative coatings.
- The process can be tailored to achieve specific material properties, such as conductivity, reflectivity, or hardness, by selecting appropriate target materials and deposition parameters.
-
Precision Control Over Film Thickness:
- Sputtering allows for precise control over film thickness by adjusting deposition time and other process parameters. This level of control is critical for applications like microelectronics, where even nanometer-scale variations can impact performance.
-
Lower Deposition Temperatures:
- Unlike some other deposition methods, sputtering can be performed at relatively low temperatures. This makes it ideal for coating temperature-sensitive substrates, such as polymers or biological specimens, without causing damage.
-
Ability to Coat Complex Geometries:
- Sputtering is highly effective for coating complex, three-dimensional surfaces, such as those found in SEM specimens or intricate mechanical components. The process ensures uniform coverage even in hard-to-reach areas.
-
Reduction of Residual Stress:
- Sputtering densifies the deposited film, reducing residual stress and improving the mechanical properties of the coating. This is particularly important for applications requiring high durability and resistance to cracking or delamination.
-
Use in Scanning Electron Microscopy (SEM):
- In SEM, sputtering is used to coat non-conductive specimens with a thin conductive layer, such as gold or platinum. This enhances the specimen's conductivity, allowing for clearer imaging and analysis.
-
Momentum Transfer Mechanism:
- The sputtering process relies on momentum transfer, where high-energy ions collide with the target material, ejecting atoms that then deposit onto the substrate. This mechanism ensures efficient and controlled material deposition.
-
Vacuum Environment and Inert Gas:
- Sputtering is performed in a vacuum chamber with an inert gas, such as argon. The vacuum environment minimizes contamination, while the inert gas is ionized to create the plasma needed for the process.
In summary, sputtering is required because it offers unparalleled precision, uniformity, and versatility in thin-film deposition. Its ability to create strong, durable coatings on complex surfaces at lower temperatures makes it indispensable in industries ranging from electronics to microscopy. By leveraging the momentum transfer mechanism and operating in a controlled vacuum environment, sputtering ensures high-quality results that meet the stringent demands of modern technology.
Summary Table:
Key Benefits of Sputtering | Applications |
---|---|
Uniform thin-film deposition | Semiconductor manufacturing, optics |
Strong atomic-level bonding | Aerospace, medical devices |
Versatility in material deposition | Electronics, decorative coatings |
Precision control over film thickness | Microelectronics |
Lower deposition temperatures | Temperature-sensitive substrates |
Ability to coat complex geometries | SEM specimens, intricate components |
Reduction of residual stress | High-durability applications |
Use in SEM for conductive coatings | Scanning electron microscopy |
Momentum transfer mechanism | Efficient and controlled material deposition |
Vacuum environment and inert gas | Minimized contamination, controlled plasma |
Interested in how sputtering can enhance your thin-film deposition process? Contact our experts today for tailored solutions!