Wood pellets are indeed primarily made from sawdust, which is a byproduct of wood processing industries such as sawmills and furniture manufacturing. Sawdust is collected, dried, and compressed under high pressure to form small, cylindrical pellets. These pellets are used as a renewable energy source for heating and electricity generation. The process of making wood pellets involves several steps, including drying, grinding, pelletizing, cooling, and packaging. The use of sawdust not only provides an efficient way to utilize waste materials but also contributes to reducing greenhouse gas emissions by replacing fossil fuels.
Key Points Explained:
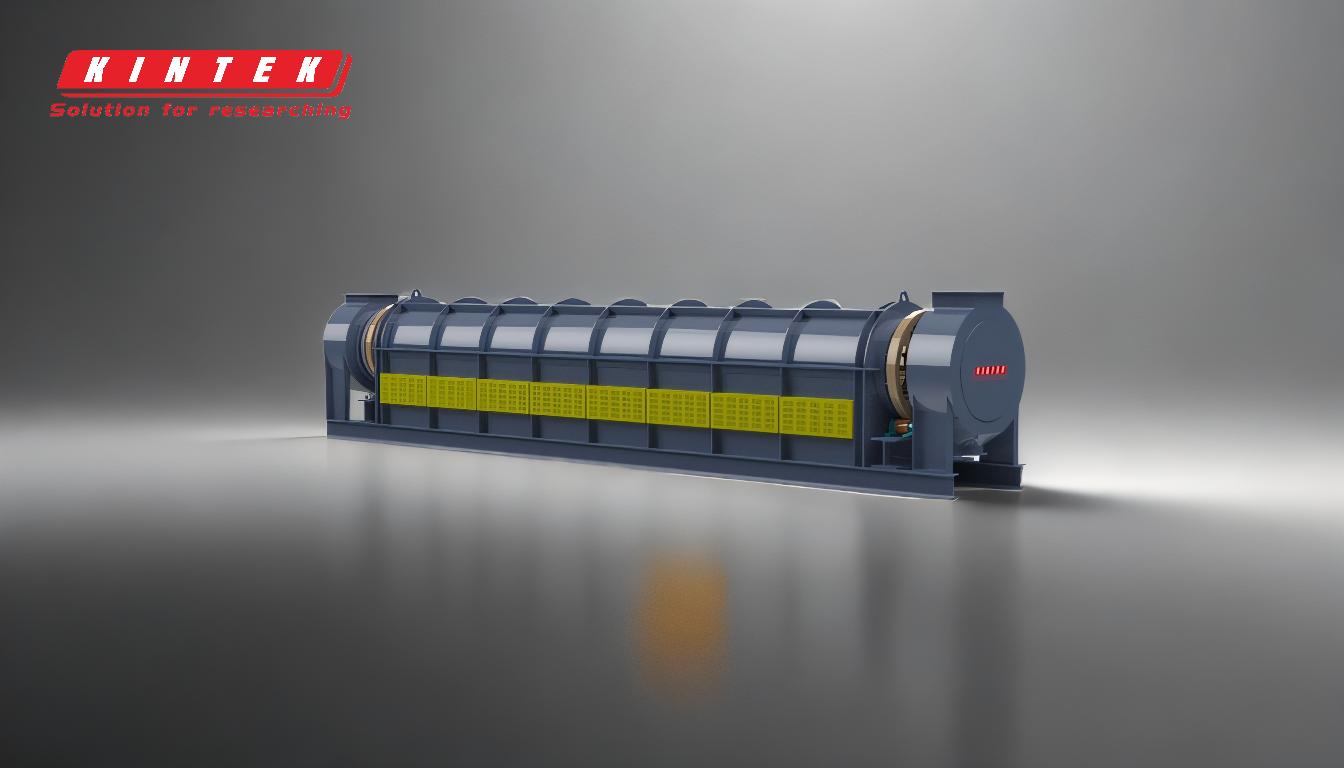
-
Primary Raw Material - Sawdust:
- Wood pellets are primarily made from sawdust, which is a byproduct of wood processing industries. This includes sawmills, furniture manufacturing, and other woodworking operations.
- Sawdust is an ideal raw material because it is abundant, readily available, and cost-effective. Using sawdust also helps in reducing waste and promoting sustainability.
-
Collection and Preparation:
- Sawdust is collected from various sources and then transported to pellet manufacturing facilities.
- The collected sawdust is often mixed with other wood residues, such as wood chips and shavings, to ensure a consistent quality of the final product.
-
Drying Process:
- Before pelletizing, the sawdust must be dried to reduce its moisture content. Typically, the moisture content is reduced to around 10-15%.
- Drying is crucial because high moisture content can affect the pelletizing process and the quality of the final pellets.
-
Grinding:
- After drying, the sawdust is ground into a fine powder. This step ensures that the material has a uniform size, which is essential for the pelletizing process.
- Grinding also helps in breaking down any larger particles that may be present in the sawdust.
-
Pelletizing:
- The ground sawdust is then fed into a pellet mill, where it is compressed under high pressure. The heat generated during compression causes the lignin in the wood to act as a natural binder, holding the pellet together.
- The pellets are extruded through small holes in a die, forming cylindrical shapes. The size of the pellets can vary, but they are typically around 6-8 mm in diameter and 10-30 mm in length.
-
Cooling and Screening:
- After pelletizing, the pellets are hot and need to be cooled down. Cooling is usually done using a cooling system that blows air over the pellets.
- Once cooled, the pellets are screened to remove any fines or broken pieces. This ensures that only high-quality pellets are packaged and sold.
-
Packaging:
- The final step is packaging the pellets for distribution. Pellets are typically packaged in bags or bulk containers, depending on the intended use.
- Packaging is important to protect the pellets from moisture and other environmental factors that could degrade their quality.
-
Environmental Benefits:
- Using sawdust to make wood pellets is an environmentally friendly practice. It helps in reducing waste and promotes the use of renewable energy sources.
- Wood pellets are considered carbon-neutral because the carbon dioxide released during combustion is offset by the carbon dioxide absorbed by the trees during their growth.
-
Applications:
- Wood pellets are primarily used for heating in residential and commercial settings. They are also used in power plants to generate electricity.
- The high energy density and low moisture content of wood pellets make them an efficient and clean-burning fuel source.
In summary, wood pellets are made from sawdust through a series of well-defined steps that ensure the production of high-quality, efficient, and environmentally friendly fuel. The use of sawdust not only provides a sustainable solution for waste management but also contributes to the reduction of greenhouse gas emissions.
Summary Table:
Key Steps in Wood Pellet Production | Details |
---|---|
Primary Raw Material | Sawdust from sawmills and woodworking industries |
Collection and Preparation | Mixed with wood chips and shavings for consistency |
Drying Process | Moisture reduced to 10-15% for optimal pelletizing |
Grinding | Sawdust ground into fine powder for uniformity |
Pelletizing | Compressed under high pressure to form cylindrical pellets |
Cooling and Screening | Pellets cooled and screened to remove fines |
Packaging | Packaged in bags or bulk containers for distribution |
Environmental Benefits | Reduces waste and greenhouse gas emissions |
Applications | Used for heating and electricity generation |
Interested in sustainable energy solutions? Contact us today to learn more about wood pellets!