Metals can indeed be shaped into various forms through a variety of manufacturing processes. These processes leverage the unique properties of metals, such as malleability and ductility, to transform them into desired shapes and sizes. Techniques like casting, forging, rolling, extrusion, and machining are commonly used to achieve this. Each method has its own advantages and is chosen based on the specific requirements of the final product, such as strength, precision, and complexity. Understanding these processes is crucial for anyone involved in the design, engineering, or procurement of metal components.
Key Points Explained:
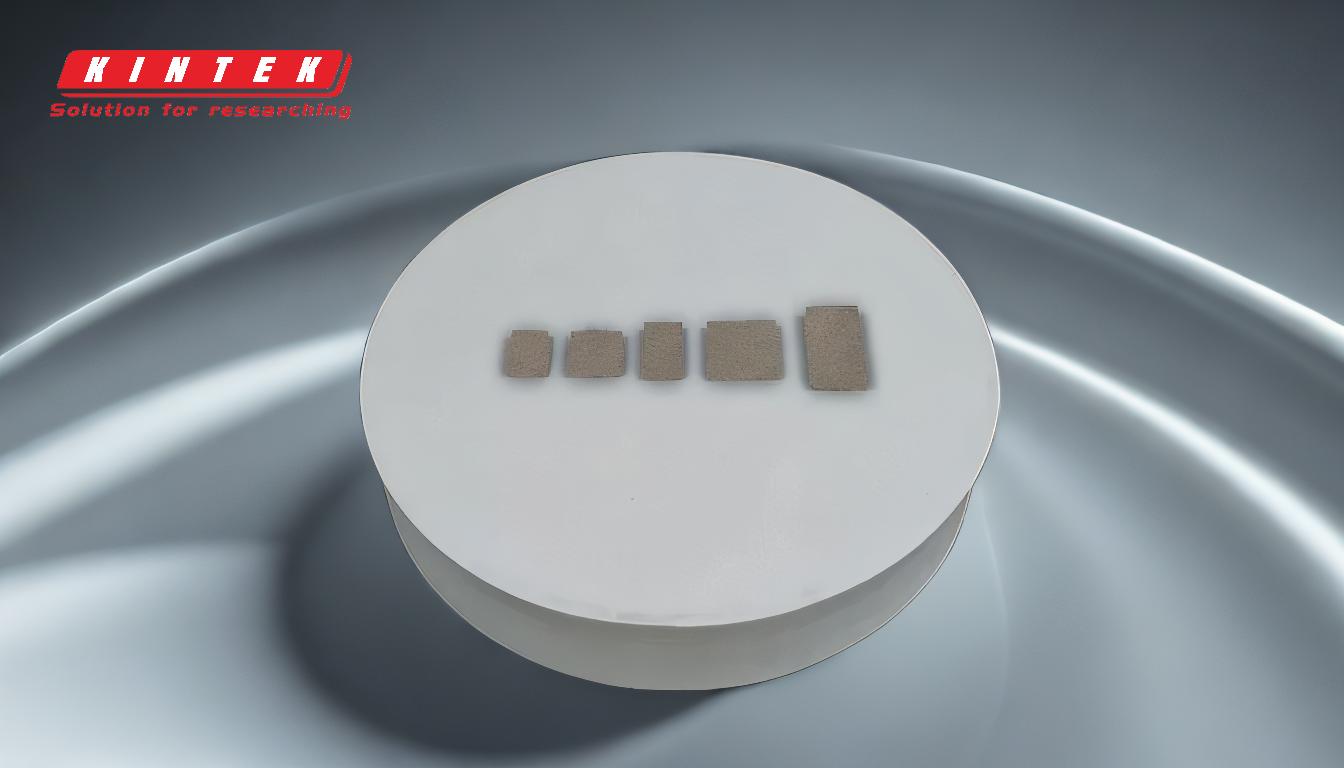
-
Malleability and Ductility of Metals:
- Metals are inherently malleable and ductile, meaning they can be deformed under stress without breaking. This property allows them to be shaped into various forms through mechanical processes.
- Malleability refers to the ability of a metal to be hammered or rolled into thin sheets, while ductility refers to the ability to be drawn into wires.
-
Casting:
- Casting is one of the oldest and most versatile methods for shaping metals. It involves pouring molten metal into a mold where it solidifies into the desired shape.
- This method is ideal for creating complex shapes and large components. Common casting techniques include sand casting, die casting, and investment casting.
-
Forging:
- Forging involves shaping metal using localized compressive forces, typically with a hammer or die. This process enhances the metal's strength by aligning its grain structure.
- Forged parts are known for their durability and are often used in high-stress applications such as automotive and aerospace components.
-
Rolling:
- Rolling is a process where metal is passed through a pair of rollers to reduce its thickness and achieve a uniform cross-section. This method is commonly used to produce sheets, plates, and foils.
- Hot rolling is performed at high temperatures, making the metal easier to shape, while cold rolling is done at room temperature to improve surface finish and dimensional accuracy.
-
Extrusion:
- Extrusion involves forcing metal through a die to create long, uniform shapes such as rods, tubes, and profiles. This method is efficient for producing complex cross-sections with a consistent quality.
- Both hot and cold extrusion techniques are used, depending on the metal and the desired properties of the final product.
-
Machining:
- Machining is a subtractive process where material is removed from a metal workpiece using cutting tools to achieve the desired shape and dimensions. Common machining operations include turning, milling, drilling, and grinding.
- This method offers high precision and is suitable for producing intricate parts with tight tolerances.
-
Other Shaping Techniques:
- Stamping: Used for creating flat metal parts with specific shapes and patterns, often used in the production of automotive body panels and electronic components.
- Drawing: Involves pulling metal through a die to reduce its diameter and increase its length, commonly used in wire production.
- Powder Metallurgy: A process where metal powders are compacted and sintered to form complex shapes, often used for small, intricate parts.
-
Selection of Shaping Method:
- The choice of shaping method depends on factors such as the type of metal, the desired shape and size of the final product, required mechanical properties, and production volume.
- For example, casting is preferred for large, complex parts, while machining is chosen for high-precision components.
Understanding these various methods and their applications allows for informed decision-making when designing or purchasing metal components, ensuring that the chosen process meets the specific needs of the project.
Summary Table:
Shaping Method | Description | Common Applications |
---|---|---|
Casting | Molten metal is poured into a mold to solidify into the desired shape. | Complex shapes, large components |
Forging | Metal is shaped using compressive forces, enhancing strength. | Automotive, aerospace parts |
Rolling | Metal is passed through rollers to reduce thickness. | Sheets, plates, foils |
Extrusion | Metal is forced through a die to create uniform shapes. | Rods, tubes, profiles |
Machining | Material is removed using cutting tools for precision. | Intricate, high-precision parts |
Stamping | Flat metal parts are created with specific shapes. | Automotive panels, electronics |
Drawing | Metal is pulled through a die to reduce diameter. | Wire production |
Powder Metallurgy | Metal powders are compacted and sintered. | Small, intricate parts |
Need help selecting the right metal shaping method for your project? Contact our experts today!