Tubular heaters are essential components in various heating applications, from industrial processes to household appliances. Their construction involves a precise combination of materials and techniques to ensure efficient heat generation and durability. The core components include a metallic tube (often made of copper, stainless steel, or other alloys), a nichrome resistance heating alloy wire, and magnesium oxide powder for insulation. The tube is sealed at both ends to prevent moisture ingress, and the entire assembly is compressed to optimize heat transfer. Below is a detailed breakdown of the manufacturing process and key considerations.
Key Points Explained:
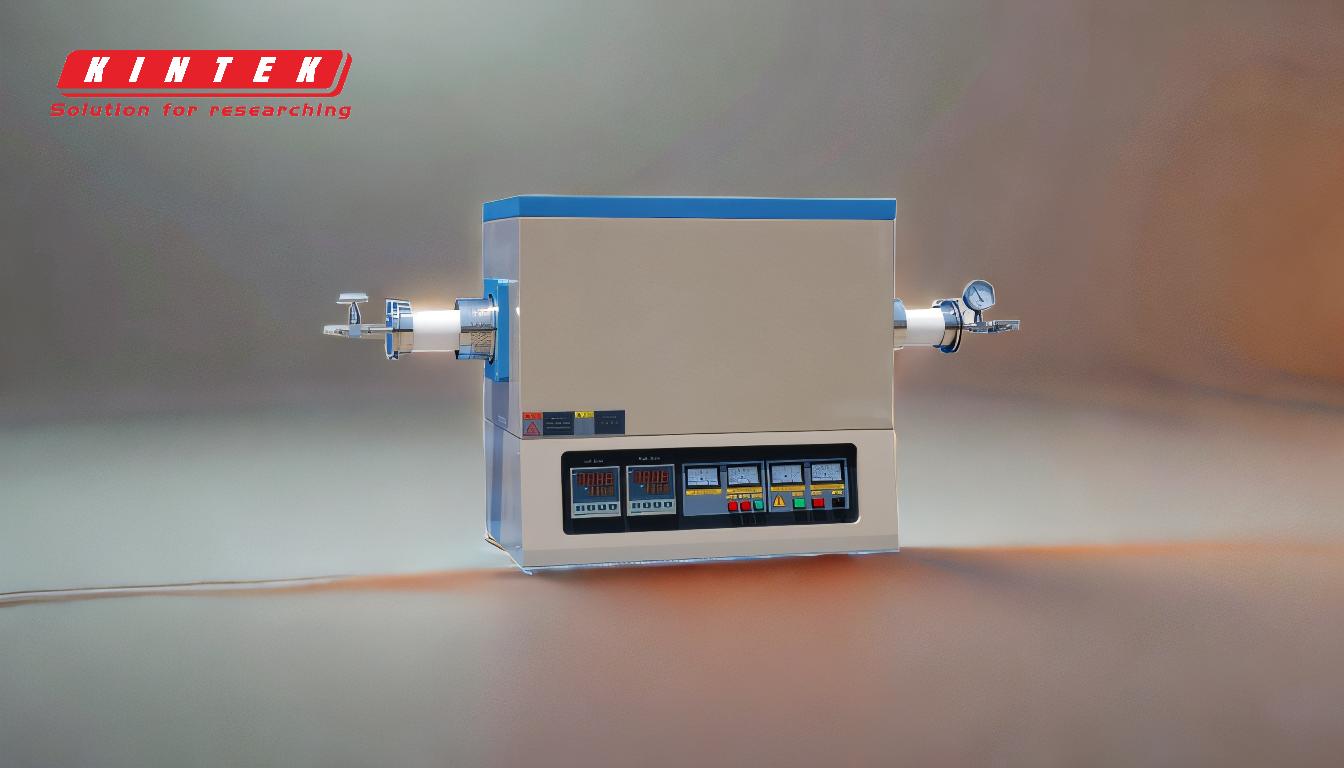
-
Core Components of Tubular Heaters
- Metallic Tube: The outer shell of the heater is typically made from seamless metal pipes such as carbon steel, titanium, stainless steel, or copper. The choice of material depends on the application, with stainless steel being common for corrosion resistance and copper for high thermal conductivity.
- Nichrome Heating Wire: A fine coil of nichrome (a nickel-chromium alloy) is used as the heating element. Nichrome is chosen for its high resistivity and ability to withstand high temperatures without oxidizing.
- Magnesium Oxide Powder: This powder fills the gap between the nichrome wire and the metallic tube. It acts as both an electrical insulator and a thermal conductor, ensuring efficient heat transfer while preventing electrical shorts.
-
Manufacturing Process
- Tube Preparation: The seamless metal tube is cut to the required length and cleaned to remove any impurities.
- Insertion of Nichrome Wire: The nichrome wire is coiled and inserted into the tube. The wire's resistance determines the heater's power output.
- Filling with Magnesium Oxide Powder: The tube is filled with magnesium oxide powder, which is compacted to ensure uniform insulation and heat transfer.
- Sealing the Ends: The tube's ends are sealed with insulating material to prevent moisture ingress, which could compromise the heater's performance and safety.
- Compression: The tube is compressed to reduce its diameter, ensuring maximum contact between the nichrome wire, magnesium oxide powder, and the tube's inner wall. This step enhances heat transfer efficiency.
-
Customization and Shaping
- Tubular heaters can be bent or shaped into various configurations (e.g., straight, U-shaped, or coiled) to meet specific application requirements. This flexibility makes them suitable for a wide range of uses, from industrial ovens to water heaters.
-
Quality and Safety Considerations
- Material Selection: The choice of tube material and nichrome wire must align with the operating environment (e.g., corrosive or high-temperature conditions).
- Insulation Integrity: Proper sealing and compression are critical to prevent moisture ingress and ensure electrical safety.
- Thermal Efficiency: The design must optimize heat transfer while minimizing energy loss.
-
Applications of Tubular Heaters
- Industrial Heating: Used in furnaces, boilers, and industrial ovens.
- Domestic Appliances: Found in water heaters, coffee makers, and space heaters.
- Specialized Uses: Custom shapes and materials allow for use in medical equipment, food processing, and more.
By understanding the materials, manufacturing process, and design considerations, purchasers can make informed decisions when selecting tubular heaters for specific applications. The combination of durable materials, efficient insulation, and precise engineering ensures reliable performance and longevity.
Summary Table:
Component | Description |
---|---|
Metallic Tube | Made of materials like stainless steel or copper for durability and conductivity. |
Nichrome Heating Wire | A nickel-chromium alloy wire for high resistivity and heat resistance. |
Magnesium Oxide Powder | Insulates and conducts heat efficiently, preventing electrical shorts. |
Manufacturing Process | Includes tube preparation, wire insertion, powder filling, sealing, and compression. |
Applications | Used in industrial heating, domestic appliances, and specialized equipment. |
Looking for reliable tubular heaters? Contact us today for expert guidance and solutions!