Cleaning a ball mill is essential to maintain its efficiency, prevent cross-contamination between materials, and ensure the longevity of the equipment. The process involves removing residual materials, cleaning the milling media (balls), and ensuring the interior and exterior surfaces are free from debris. Proper cleaning depends on the type of material being milled, the size of the mill, and the milling media used. This guide outlines a step-by-step approach to cleaning a ball mill, including considerations for different materials and safety precautions.
Key Points Explained:
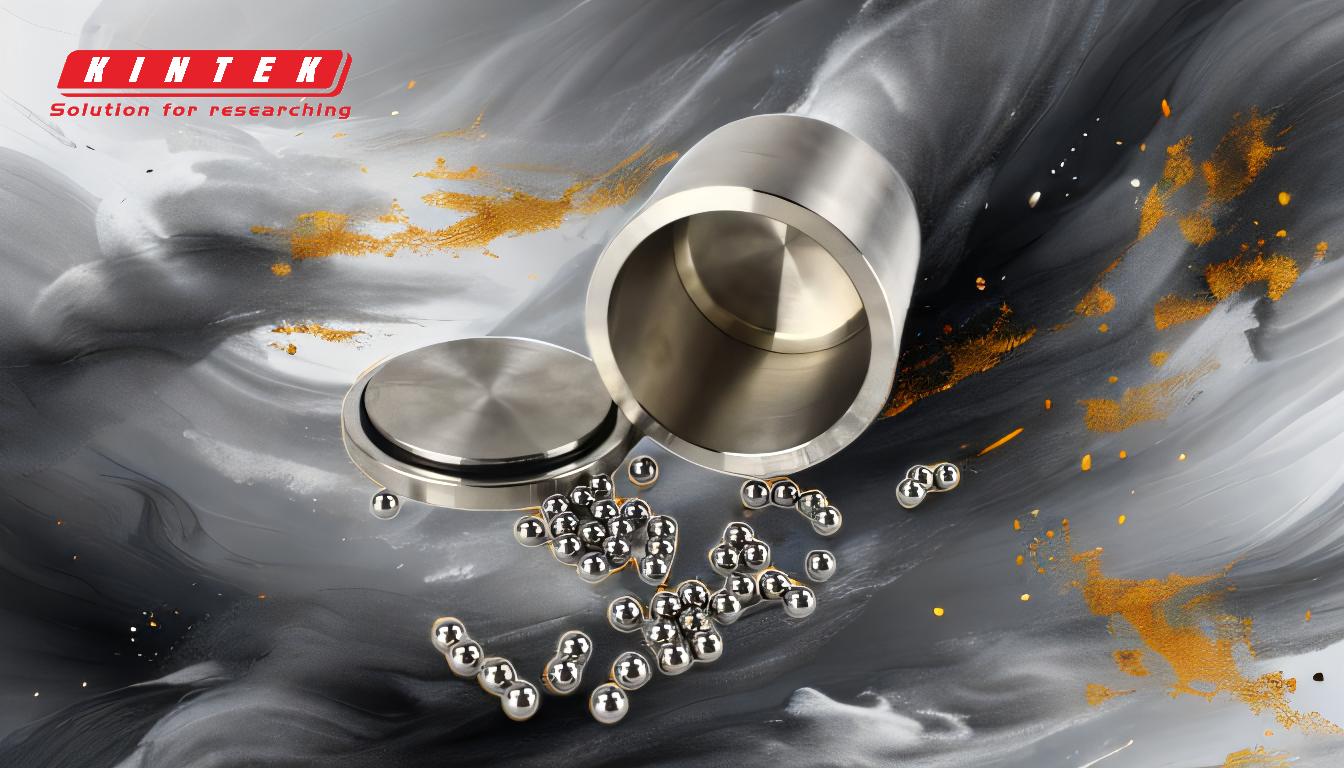
-
Preparation for Cleaning
- Safety First: Wear appropriate personal protective equipment (PPE) such as gloves, goggles, and masks to protect against dust and chemical exposure.
- Power Off: Ensure the ball mill is completely powered off and disconnected from any energy source before starting the cleaning process.
- Empty the Mill: Remove any remaining material from the mill. This can be done by tilting the mill or using a vacuum system to extract fine particles.
-
Cleaning the Milling Media (Balls)
- Remove the Balls: Carefully take out the milling balls from the mill. The number and size of the balls will depend on the mill's design.
-
Wash the Balls: Clean the balls using a suitable solvent or cleaning agent. For example:
- Water and Detergent: For general cleaning, a mixture of water and mild detergent can be used.
- Organic Solvents: For organic residues, solvents like acetone or ethanol may be necessary.
- Acidic or Alkaline Solutions: For inorganic residues, acidic (e.g., dilute hydrochloric acid) or alkaline (e.g., sodium hydroxide) solutions may be required.
- Dry the Balls: After washing, thoroughly dry the balls to prevent rust or corrosion. Use a clean, dry cloth or let them air dry.
-
Cleaning the Mill Chamber
- Wipe Down the Interior: Use a clean, lint-free cloth to wipe down the interior surfaces of the mill chamber. For stubborn residues, use a brush or sponge with the appropriate cleaning solution.
- Rinse if Necessary: If the mill chamber is heavily soiled, rinse it with water or a solvent, ensuring that all cleaning agents are completely removed afterward.
- Inspect for Damage: While cleaning, inspect the interior for any signs of wear, cracks, or damage that may need repair.
-
Cleaning the Exterior
- Wipe Down Surfaces: Clean the exterior surfaces of the mill using a damp cloth and mild detergent. Avoid using abrasive materials that could scratch or damage the surface.
- Check Seals and Gaskets: Inspect and clean any seals or gaskets to ensure they are free from debris and in good condition.
-
Reassembly and Final Checks
- Reinstall the Balls: Once the balls and mill chamber are clean and dry, reinstall the balls into the mill.
- Check Alignment: Ensure that the mill is properly aligned and that all components are securely in place.
- Test Run: Before resuming regular operations, perform a test run to ensure the mill is functioning correctly and that there are no unusual noises or vibrations.
-
Special Considerations for Different Materials
- Metal Powders: If the mill was used for metal powders, extra care should be taken to remove all traces of metal to prevent oxidation or contamination.
- Ceramic or Glass Materials: For ceramic or glass materials, avoid using abrasive cleaning agents that could scratch the surfaces.
- Organic Materials: When milling organic materials, ensure that all organic residues are completely removed to prevent microbial growth or contamination.
-
Maintenance and Preventive Measures
- Regular Cleaning Schedule: Establish a regular cleaning schedule based on the frequency of use and the types of materials being milled.
- Lubrication: Periodically lubricate moving parts to ensure smooth operation and prevent wear.
- Inspect for Wear: Regularly inspect the mill and milling media for signs of wear or damage and replace components as needed.
By following these steps, you can ensure that your ball mill remains in optimal condition, providing consistent performance and extending its operational life. Proper cleaning not only maintains the mill's efficiency but also ensures the quality of the materials being processed.
Summary Table:
Step | Key Actions |
---|---|
Preparation | - Wear PPE, power off, and empty the mill. |
Cleaning Milling Balls | - Remove, wash with suitable solvents, and dry thoroughly. |
Cleaning Mill Chamber | - Wipe interior, rinse if needed, and inspect for damage. |
Cleaning Exterior | - Wipe surfaces and check seals/gaskets. |
Reassembly & Checks | - Reinstall balls, check alignment, and perform a test run. |
Material Considerations | - Follow specific cleaning steps for metal, ceramic, or organic materials. |
Maintenance | - Establish a cleaning schedule, lubricate parts, and inspect for wear. |
Need help maintaining your ball mill? Contact our experts today for personalized advice!