Cleaning ball milling media is essential to maintain its performance and prevent cross-contamination between different materials. The process involves removing residues, contaminants, and debris from the media's surface. Common cleaning methods include mechanical cleaning, chemical cleaning, and ultrasonic cleaning. The choice of method depends on the type of media, the material being milled, and the level of contamination. Proper cleaning ensures the longevity of the media and consistent milling results. Below, the key points for cleaning ball milling media are explained in detail.
Key Points Explained:
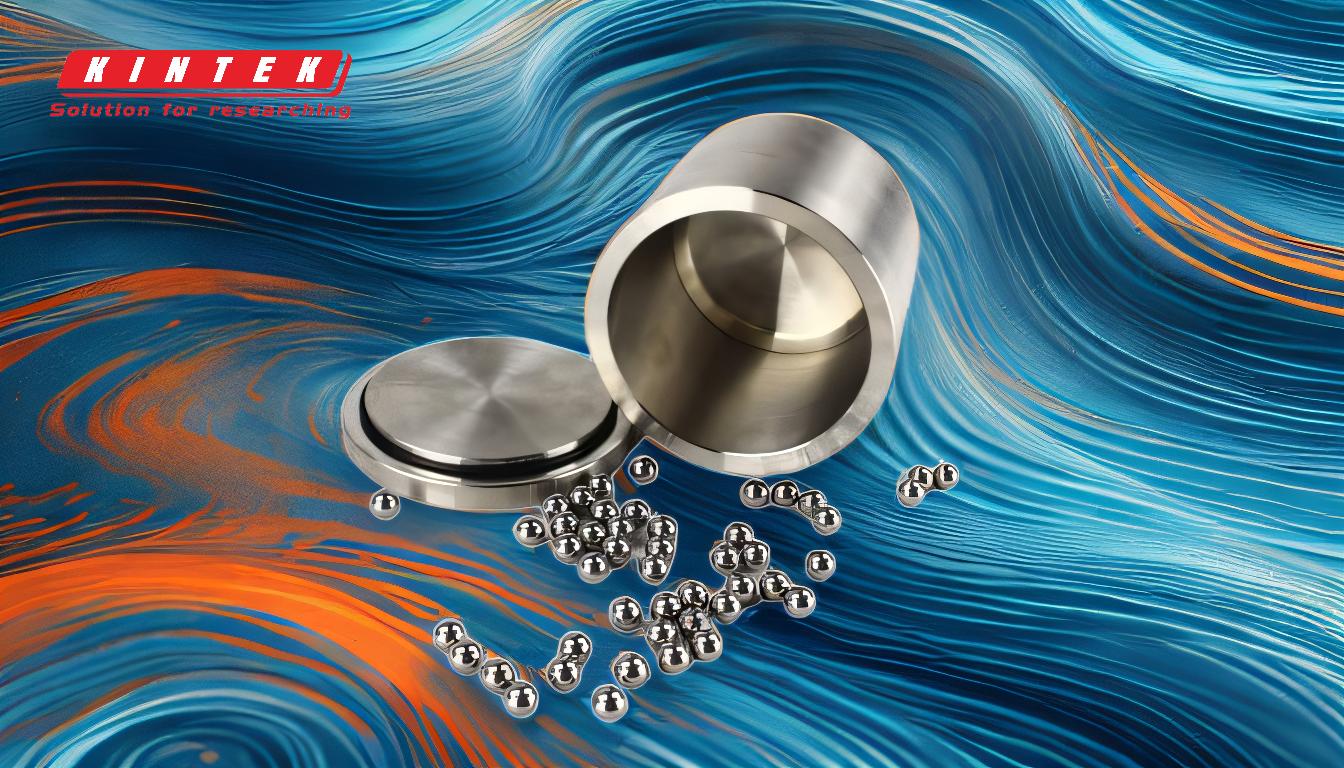
-
Understanding the Importance of Cleaning Ball Milling Media
- Ball milling media accumulates residues from the materials being milled, which can affect the quality of future milling processes.
- Contaminants can lead to cross-contamination, altering the properties of the final product.
- Regular cleaning extends the lifespan of the media and ensures consistent milling performance.
-
Types of Ball Milling Media and Their Cleaning Requirements
- Stainless Steel Media: Resistant to corrosion but may require thorough cleaning to remove metal residues.
- Ceramic Media: Fragile and prone to chipping; requires gentle cleaning methods.
- Tungsten Carbide Media: Durable but may need specialized cleaning agents to remove stubborn residues.
- Plastic or Polymer Media: Sensitive to harsh chemicals; requires mild cleaning solutions.
-
Mechanical Cleaning Methods
- Abrasive Cleaning: Using soft abrasives like sand or fine grit to scrub the media manually.
- Tumbling: Placing the media in a tumbler with cleaning agents (e.g., soapy water) to remove residues through friction.
- Brushing: Using soft-bristle brushes to clean the media surface without damaging it.
-
Chemical Cleaning Methods
- Acidic Solutions: Suitable for removing metal oxides and inorganic residues (e.g., dilute hydrochloric acid for stainless steel media).
- Alkaline Solutions: Effective for organic residues (e.g., sodium hydroxide solutions).
- Solvents: Use solvents like acetone or ethanol for removing grease or oil-based contaminants.
- Always rinse thoroughly after chemical cleaning to remove any residual cleaning agents.
-
Ultrasonic Cleaning
- Ultrasonic cleaners use high-frequency sound waves to create cavitation bubbles, which dislodge contaminants from the media surface.
- This method is highly effective for intricate or hard-to-reach areas.
- Suitable for all types of media, provided the cleaning solution is compatible with the material.
-
Drying and Storage After Cleaning
- After cleaning, dry the media completely to prevent rust or corrosion (especially for metal media).
- Use a clean, dry cloth or air-drying methods.
- Store the media in a dry, dust-free environment to maintain cleanliness until the next use.
-
Safety Considerations
- Wear appropriate personal protective equipment (PPE) when handling cleaning agents, especially acids and alkalis.
- Ensure proper ventilation when using chemical cleaners.
- Dispose of used cleaning solutions responsibly, following local regulations.
-
Frequency of Cleaning
- Clean the media after each milling session to prevent residue buildup.
- For heavy contamination, perform a deep cleaning periodically.
- Inspect the media regularly for signs of wear or damage, which may necessitate replacement.
By following these steps, you can effectively clean ball milling media, ensuring optimal performance and longevity. The choice of cleaning method should align with the type of media and the nature of the contaminants to achieve the best results.
Summary Table:
Aspect | Details |
---|---|
Importance of Cleaning | Prevents cross-contamination, ensures consistent results, and extends lifespan. |
Media Types & Cleaning | Stainless Steel, Ceramic, Tungsten Carbide, Plastic/Polymer – each requires specific methods. |
Mechanical Cleaning | Abrasive cleaning, tumbling, brushing. |
Chemical Cleaning | Acidic, alkaline solutions, and solvents for different residues. |
Ultrasonic Cleaning | High-frequency sound waves for intricate cleaning. |
Drying & Storage | Dry thoroughly, store in a clean, dust-free environment. |
Safety Considerations | Use PPE, ensure ventilation, and dispose of chemicals responsibly. |
Cleaning Frequency | Clean after each session; deep clean periodically for heavy contamination. |
Need help choosing the right cleaning method for your ball milling media? Contact our experts today!