Removing sputter coating involves understanding the nature of the coating and the substrate it adheres to. Sputter coatings are typically thin films deposited at an atomic level, forming strong bonds with the substrate. The removal process depends on the type of coating material, the substrate, and the application requirements. Common methods include mechanical polishing, chemical etching, and plasma cleaning. Each method has its advantages and limitations, and the choice depends on factors like coating thickness, substrate sensitivity, and desired surface finish. Below, we explore the key points and methods for removing sputter coatings effectively.
Key Points Explained:
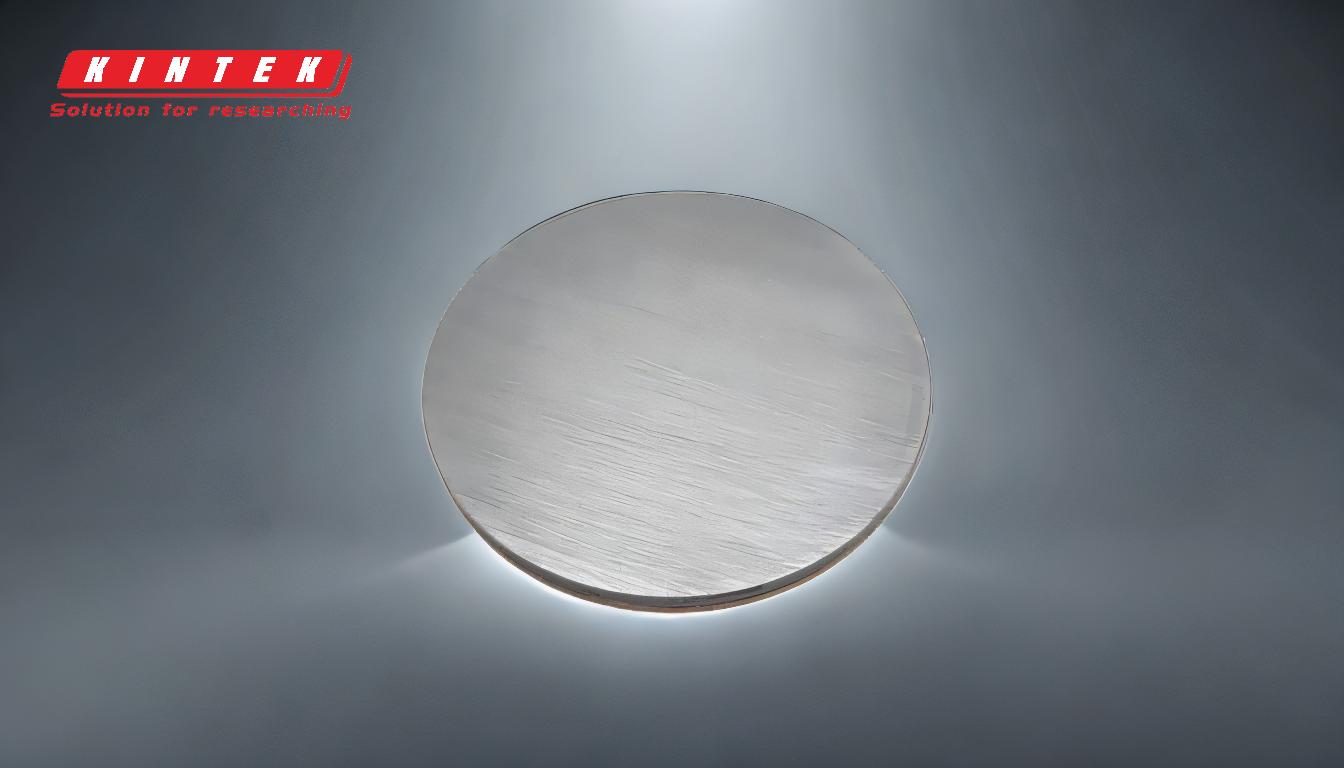
-
Understanding Sputter Coating Adhesion
- Sputter coatings form strong atomic-level bonds with the substrate due to the high-energy momentum transfer process during deposition.
- The adhesion strength depends on the coating material (e.g., gold, platinum, carbon) and the substrate (e.g., glass, metal, polymer).
- This strong bond makes removal challenging and requires careful selection of removal techniques to avoid damaging the substrate.
-
Mechanical Removal Methods
-
Polishing or Abrasion:
- Use fine abrasives or polishing compounds to physically remove the coating.
- Suitable for thicker coatings or robust substrates like metals.
- Risks include scratching or damaging the substrate if not done carefully.
-
Ultrasonic Cleaning:
- Utilizes high-frequency sound waves in a liquid medium to dislodge coatings.
- Effective for loosely adhered coatings or small, intricate parts.
- May not work well for strongly bonded or very thin coatings.
-
Polishing or Abrasion:
-
Chemical Removal Methods
-
Chemical Etching:
- Use specific chemicals (e.g., acids or solvents) to dissolve the coating material.
- Example: Gold coatings can be removed using aqua regia (a mixture of nitric and hydrochloric acids).
- Requires careful handling and disposal of hazardous chemicals.
-
Selective Solvents:
- Choose solvents that target the coating material without affecting the substrate.
- Example: Acetone or isopropanol for organic coatings on glass.
- Test compatibility with the substrate to avoid damage.
-
Chemical Etching:
-
Plasma Cleaning
- Uses reactive gases in a plasma state to break down and remove the coating at a molecular level.
- Suitable for thin coatings and delicate substrates like polymers or semiconductors.
- Requires specialized equipment and controlled environments.
-
Considerations for Substrate Sensitivity
- Delicate substrates (e.g., glass, polymers) require non-invasive methods like plasma cleaning or mild chemical etching.
- Robust substrates (e.g., metals) can withstand more aggressive methods like mechanical polishing.
- Always test removal methods on a small area to ensure no damage occurs.
-
Post-Removal Surface Preparation
- After removal, clean the substrate thoroughly to remove any residual coating or chemicals.
- Use deionized water or appropriate cleaning agents to ensure a pristine surface.
- Inspect the surface for any damage or irregularities before further processing.
-
Safety and Environmental Considerations
- Wear appropriate personal protective equipment (PPE) when handling chemicals or abrasive materials.
- Dispose of hazardous waste (e.g., used chemicals or abrasives) in compliance with local regulations.
- Ensure proper ventilation when using solvents or plasma cleaning systems.
By understanding these key points, you can choose the most appropriate method for removing sputter coatings based on your specific application and substrate requirements. Always prioritize safety and precision to achieve the desired results.
Summary Table:
Method | Best For | Advantages | Limitations |
---|---|---|---|
Mechanical Polishing | Thick coatings, robust substrates | Effective for strong bonds; no chemicals required | Risk of substrate damage; not for delicate surfaces |
Chemical Etching | Specific coating materials | Precise removal; effective for thin coatings | Hazardous chemicals; requires careful handling |
Plasma Cleaning | Thin coatings, delicate substrates | Non-invasive; molecular-level removal | Requires specialized equipment |
Need help choosing the right sputter coating removal method? Contact our experts today for personalized advice!