Using ceramic casting molds involves a series of steps to transform liquid clay (slip) into a solid ceramic piece. The process begins with preparing the mold and slip, followed by filling the mold, removing excess slip, releasing the casting, and finishing the piece. Each step requires careful attention to detail to ensure the final product is free of defects and meets the desired specifications. Below is a detailed explanation of the process.
Key Points Explained:
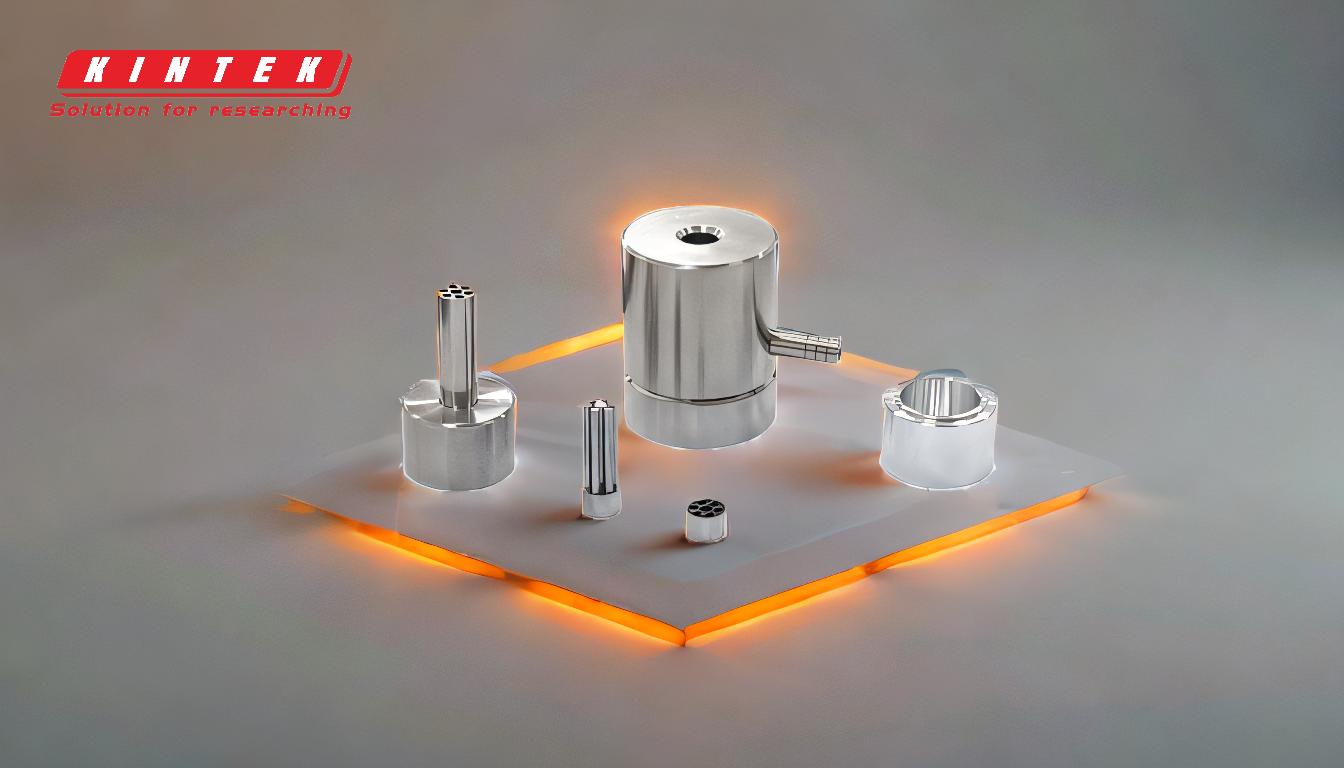
-
Preparing the Mold and Slip
- Mold Preparation: Ensure the mold is clean and free of debris. Align the two halves of the mold precisely and secure them tightly using rubber bands or clamps. This prevents slip from leaking out during the casting process.
- Slip Preparation: The slip (liquid clay) should be properly mixed to achieve a smooth, consistent texture. Any lumps or air bubbles can lead to imperfections in the final piece.
-
Filling the Mold with Slip
- Slowly pour the slip into the mold through the designated opening. Pouring too quickly can trap air bubbles, which may cause defects in the finished piece.
- Fill the mold until the slip reaches the top. Ensure the slip evenly coats the interior surfaces of the mold.
-
Removing Excess Slip
- After the slip has been poured, allow it to sit for a few minutes to begin setting. Then, carefully pour out the excess slip from the mold. This step ensures the walls of the ceramic piece are of uniform thickness.
- The timing for this step is crucial. If the slip is poured out too soon, the walls may be too thin; if left too long, the piece may become too thick or uneven.
-
Releasing the Casting from the Mold
- Allow the slip to fully set and harden within the mold. The drying time depends on the size of the piece and the type of slip used.
- Once the piece is firm enough to handle, gently separate the mold halves and carefully remove the casting. Be cautious to avoid damaging the piece during this step.
-
Finishing the Piece
- After removing the casting, inspect it for any imperfections, such as seams or rough edges. Use tools like sponges, knives, or sandpaper to smooth and refine the piece.
- Allow the piece to dry completely before proceeding to the next steps, such as bisque firing, glazing, and final firing.
By following these steps meticulously, you can create high-quality ceramic pieces using casting molds. Proper preparation, timing, and attention to detail are essential for achieving the best results.
Summary Table:
Step | Key Actions |
---|---|
1. Preparing the Mold and Slip | - Clean and align mold halves. Secure tightly. - Mix slip to a smooth, lump-free consistency. |
2. Filling the Mold | - Pour slip slowly to avoid air bubbles. - Ensure even coating of mold surfaces. |
3. Removing Excess Slip | - Allow slip to set briefly. - Pour out excess slip at the right time for uniform thickness. |
4. Releasing the Casting | - Let slip harden fully. - Gently separate mold halves and remove casting carefully. |
5. Finishing the Piece | - Smooth imperfections with tools. - Dry completely before firing and glazing. |
Ready to create flawless ceramic pieces? Contact our experts today for personalized guidance!