A hammermill shredder is a versatile and efficient machine used to reduce the size of various materials through a high-speed rotary hammer mechanism. The process involves feeding material into a chamber where rapidly rotating hammers strike and break down the material into smaller particles. These particles are then forced through a screen or grate, which determines the final size of the shredded product. Hammermill shredders are widely used in industries such as agriculture, recycling, and manufacturing due to their ability to handle a wide range of materials, including wood, paper, plastics, and biomass. The key to their effectiveness lies in the combination of impact, shear, and attrition forces applied by the hammers, which ensures thorough and consistent shredding.
Key Points Explained:
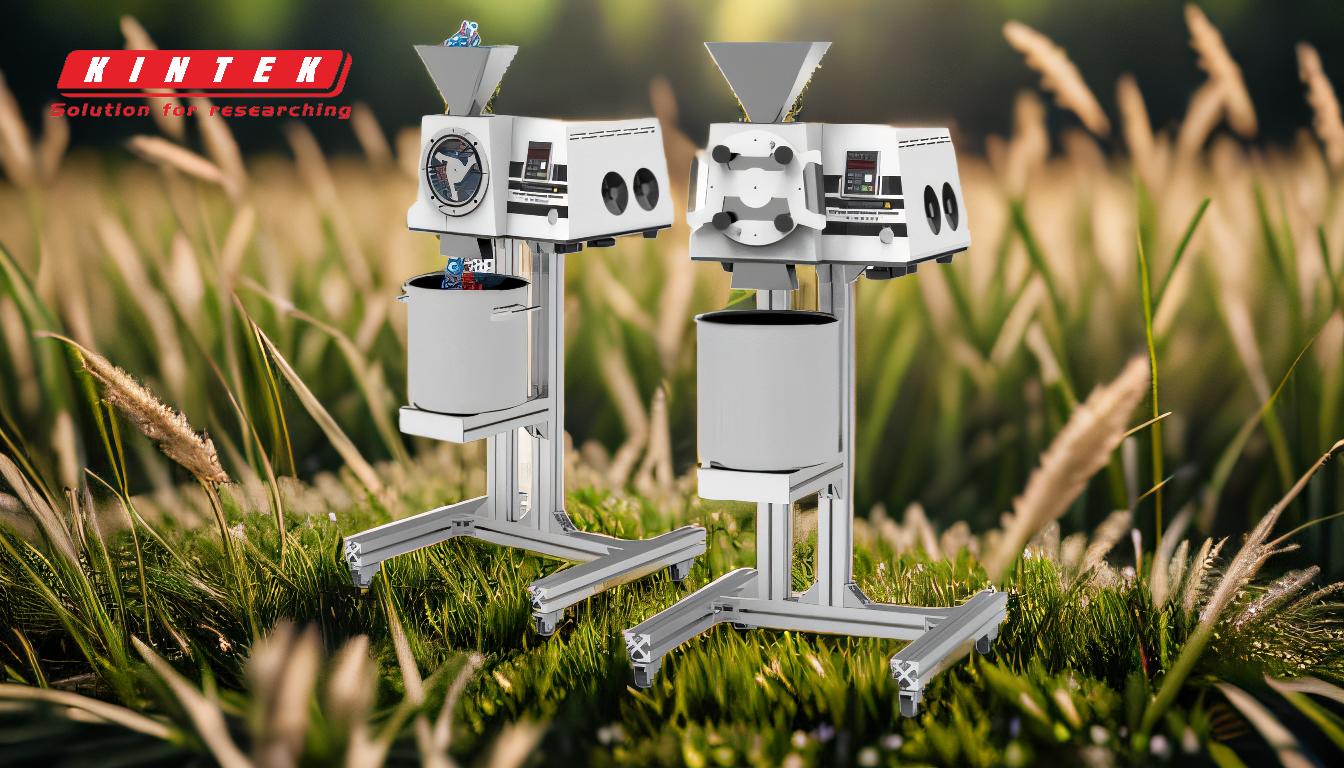
-
Basic Structure and Components:
- A hammermill shredder consists of several key components, including a rotor, hammers, a screen or grate, and a feed mechanism.
- The rotor is the central rotating shaft that holds the hammers, which are typically made of hardened steel to withstand the forces involved in shredding.
- The screen or grate is positioned at the bottom of the shredding chamber and determines the size of the shredded material by controlling the exit of particles.
-
Operation Principle:
- The material to be shredded is fed into the shredding chamber, either manually or through an automated feed system.
- As the rotor spins at high speed, the hammers strike the material repeatedly, breaking it down through a combination of impact, shear, and attrition forces.
- The material is forced against the screen or grate, which further reduces its size by allowing only particles smaller than the screen openings to pass through.
-
Types of Hammers:
- Hammers in a hammermill shredder can vary in shape, size, and material, depending on the type of material being processed.
- Common types include swing hammers, rigid hammers, and reversible hammers, each designed for specific applications and material types.
- The choice of hammer type affects the efficiency and effectiveness of the shredding process, as well as the wear and tear on the machine.
-
Applications:
- Hammermill shredders are used in a variety of industries, including agriculture (for shredding crop residues and animal feed), recycling (for reducing the size of waste materials), and manufacturing (for processing raw materials).
- They are particularly effective for shredding fibrous materials, such as wood and paper, as well as brittle materials like plastics and glass.
-
Advantages:
- Hammermill shredders are known for their high throughput and ability to handle a wide range of materials.
- They are relatively simple to operate and maintain, with replaceable hammers and screens that can be easily swapped out as needed.
- The shredding process is highly efficient, with minimal energy loss, making it a cost-effective solution for many industries.
-
Maintenance and Safety:
- Regular maintenance is essential to ensure the longevity and optimal performance of a hammermill shredder.
- This includes routine inspection and replacement of worn hammers and screens, as well as lubrication of moving parts.
- Safety precautions, such as proper guarding and operator training, are also critical to prevent accidents during operation.
In summary, a hammermill shredder works by using high-speed rotating hammers to break down materials through a combination of impact, shear, and attrition forces. The shredded material is then forced through a screen or grate to achieve the desired particle size. This versatile machine is widely used across various industries for its efficiency, simplicity, and ability to handle a diverse range of materials.
Summary Table:
Aspect | Details |
---|---|
Key Components | Rotor, hammers, screen/grate, feed mechanism |
Operation Principle | High-speed hammers break materials via impact, shear, and attrition forces |
Common Hammer Types | Swing, rigid, and reversible hammers |
Applications | Agriculture, recycling, manufacturing |
Advantages | High throughput, versatile, easy maintenance, cost-effective |
Maintenance | Regular inspection, hammer/screen replacement, lubrication |
Ready to enhance your material processing? Contact us today to find the perfect hammermill shredder for your needs!