Pyrolysis reactors are specialized equipment designed to thermally decompose organic materials in the absence of oxygen, converting them into useful byproducts such as syngas, biochar, and fuel oil. These reactors operate based on thermodynamic principles and rely on external heat sources to maintain high temperatures. Depending on the design, such as fluidized bed reactors or rotating drum reactors, they can handle different types of waste materials, including plastics, rubber, tires, and biomass. The process involves multiple systems, including feeding, pyrolysis, discharging, and gas recycling, ensuring efficient and eco-friendly waste conversion. Pyrolysis reactors are integral to sustainable waste management and energy recovery.
Key Points Explained:
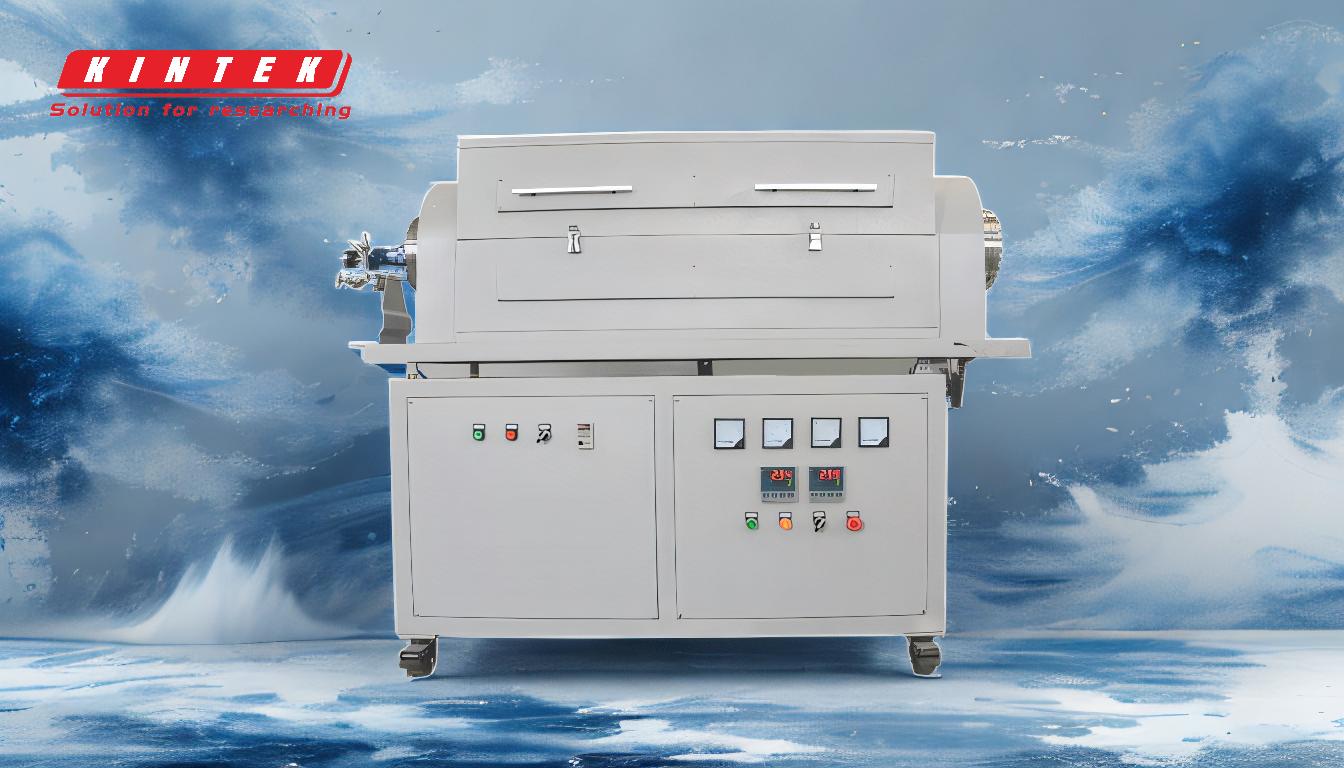
-
Principle of Pyrolysis Reactors:
- Pyrolysis reactors operate in a closed system with no oxygen, relying on external heat to thermally decompose organic materials.
- The process is governed by thermodynamic principles, where high temperatures (typically 400–800°C) break down complex molecules into simpler ones.
- This absence of oxygen prevents combustion, ensuring the production of valuable byproducts like syngas, biochar, and fuel oil.
-
Types of Pyrolysis Reactors:
-
Fluidized Bed Reactor:
- Separates waste into two zones: the bed section (low oxygen) and the free section (secondary air addition).
- In the bed section, drying, pyrolysis, and gasification occur under low oxygen conditions.
- In the free section, further burning takes place at temperatures of 825°C or higher, with a gas retention period of at least 2 seconds.
-
Rotating Drum Reactor:
- Consists of a drum-shaped vessel that rotates continuously to circulate heat internally.
- Ideal for slow pyrolysis of biomass, producing syngas and biochar.
- The drum is housed in a furnace that supplies the necessary heat.
-
Fluidized Bed Reactor:
-
Components of a Pyrolysis Reactor System:
-
Feeding System:
- Delivers raw materials to the reactor automatically in a fully sealed manner, ensuring no oxygen enters the system.
-
Pyrolysis Reactor:
- The core component where high-temperature pyrolysis occurs, involving physical and chemical reactions.
-
Discharging System:
- Transports solid byproducts like carbon black into a cooling tank equipped with water-cooling pipes.
-
Syn-Gas Recycling System:
- Captures and recycles combustible gases produced during pyrolysis, which can be reused to heat the reactor.
-
De-Dusting System:
- Purifies emission gases to meet stringent environmental standards, such as EU emission regulations.
-
Feeding System:
-
Applications and Benefits:
- Pyrolysis reactors are used to process waste materials like plastics, rubber, tires, and sludge, converting them into fuel oil and other valuable products.
- They contribute to solving environmental pollution by reducing landfill waste and generating renewable energy sources.
- The process is eco-friendly, as it minimizes emissions and maximizes resource recovery.
-
Design and Operation:
- The reactor system comprises four main parts: the driving device, base, main furnace, and casing.
- The driving device ensures continuous rotation or movement of the reactor components.
- The base provides structural support, while the main furnace houses the pyrolysis process.
- The casing encloses the system, ensuring safety and heat retention.
-
Environmental and Economic Impact:
- Pyrolysis reactors support a circular economy by recycling waste into usable products, reducing reliance on fossil fuels.
- They help achieve pollution-free waste management, aligning with global sustainability goals.
- The production of syngas and biochar offers economic benefits, as these byproducts can be used for energy generation and soil enrichment.
By understanding these key points, equipment and consumable purchasers can evaluate the suitability of pyrolysis reactors for their specific needs, ensuring efficient and sustainable waste management solutions.
Summary Table:
Key Aspect | Details |
---|---|
Principle | Operates in a closed, oxygen-free system using external heat (400–800°C). |
Types | Fluidized bed reactors, rotating drum reactors. |
Components | Feeding system, pyrolysis reactor, discharging system, gas recycling, de-dusting. |
Applications | Processes plastics, rubber, tires, and biomass into fuel oil and syngas. |
Benefits | Reduces landfill waste, generates renewable energy, and minimizes emissions. |
Environmental Impact | Supports circular economy and pollution-free waste management. |
Discover how pyrolysis reactors can transform your waste management—contact us today for expert guidance!