A rotary tablet press is a sophisticated piece of pharmaceutical equipment designed to compress powdered or granular materials into tablets of uniform size, shape, and weight. It operates through a series of coordinated mechanical actions, including feeding, compression, and ejection. The process begins with the filling of dies with the material to be compressed. The dies then rotate to the compression zone, where upper and lower punches apply pressure to form the tablet. After compression, the tablets are ejected from the dies and collected. This continuous, high-speed operation makes rotary tablet presses essential for large-scale tablet production in the pharmaceutical industry.
Key Points Explained:
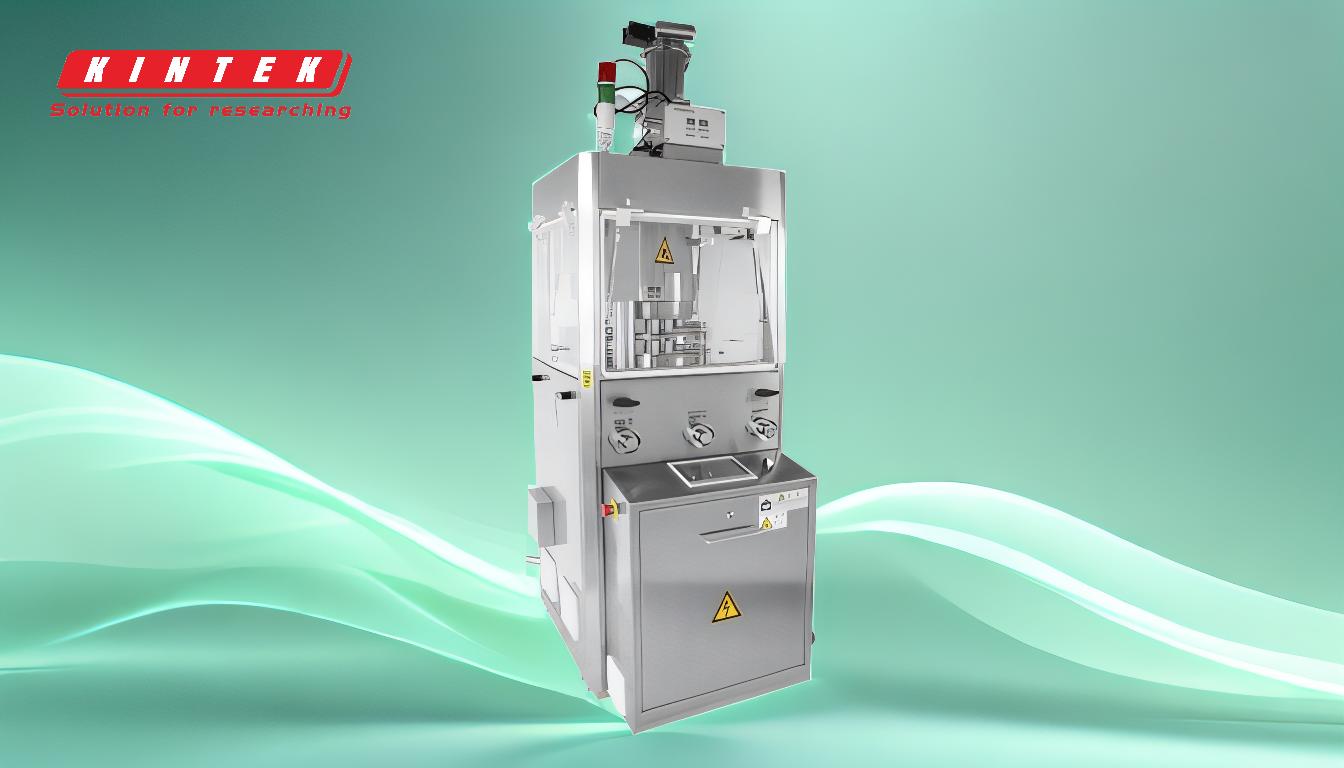
-
Feeding Mechanism:
- The rotary tablet press begins its operation with the feeding of powdered or granular material into the die cavities. This is typically achieved using a feed frame or hopper that ensures a consistent and even distribution of the material into each die. The feed frame oscillates or rotates to facilitate uniform filling, which is crucial for producing tablets of consistent weight and quality.
-
Die Filling:
- Once the material is fed into the die cavities, the dies move into position under the feed frame. The depth of the die cavity determines the volume of material that will be compressed. Adjustments to the die depth can be made to control the tablet weight. Proper die filling is essential to avoid issues such as under-filling or over-filling, which can lead to weight variation in the final tablets.
-
Compression Process:
- The core of the rotary tablet press operation is the compression process. As the dies rotate, they pass between upper and lower punches. The punches apply significant pressure to the material within the dies, compressing it into a solid tablet. The compression force can be adjusted to achieve the desired tablet hardness and density. This step is critical for ensuring the structural integrity and efficacy of the tablets.
-
Ejection of Tablets:
- After compression, the dies continue to rotate to the ejection zone. Here, the lower punches rise to push the formed tablets out of the dies. The ejected tablets are then guided to a collection chute or conveyor belt for further processing or packaging. The ejection process must be smooth and consistent to prevent damage to the tablets and ensure a continuous production flow.
-
Tooling and Maintenance:
- The performance of a rotary tablet press heavily depends on the quality and maintenance of its tooling, including dies and punches. Regular inspection and maintenance of these components are necessary to prevent wear and tear, which can affect tablet quality. Proper lubrication and cleaning of the press are also essential to maintain its efficiency and longevity.
-
Control and Automation:
- Modern rotary tablet presses are equipped with advanced control systems that allow for precise adjustments and monitoring of the compression process. These systems can include features such as weight control, thickness monitoring, and automatic rejection of defective tablets. Automation enhances the consistency and efficiency of tablet production, reducing the likelihood of human error and increasing throughput.
-
Applications and Versatility:
- Rotary tablet presses are versatile machines capable of producing a wide range of tablet shapes and sizes. They are used not only in the pharmaceutical industry but also in the production of nutraceuticals, confectionery, and other compressed products. The ability to customize tooling and adjust operational parameters makes rotary tablet presses suitable for various applications, from small-scale R&D to large-scale manufacturing.
In summary, the rotary tablet press is a critical piece of equipment in tablet manufacturing, combining precision engineering with advanced control systems to produce high-quality tablets efficiently. Its operation involves a series of well-coordinated steps, from feeding and compression to ejection, each of which plays a vital role in ensuring the consistency and quality of the final product.
Summary Table:
Step | Description |
---|---|
Feeding Mechanism | Powdered or granular material is fed into die cavities using a feed frame or hopper. |
Die Filling | Dies are filled uniformly, with adjustments to control tablet weight and volume. |
Compression Process | Upper and lower punches apply pressure to compress material into solid tablets. |
Ejection of Tablets | Tablets are ejected from dies and collected for further processing or packaging. |
Tooling & Maintenance | Regular inspection and maintenance of dies and punches ensure consistent quality. |
Control & Automation | Advanced systems monitor and adjust compression for precision and efficiency. |
Applications | Versatile for pharmaceuticals, nutraceuticals, confectionery, and more. |
Ready to optimize your tablet production? Contact our experts today for tailored solutions!