Particle size significantly affects the efficiency and outcomes of ball milling. Smaller particles generally require smaller grinding balls and longer milling times to achieve the desired fineness. The process is influenced by several factors, including the size and type of grinding medium, the properties of the material being ground, the rotation speed of the mill, and the filling ratio of the mill. Understanding these factors helps optimize the milling process for better productivity and desired particle size distribution.
Key Points Explained:
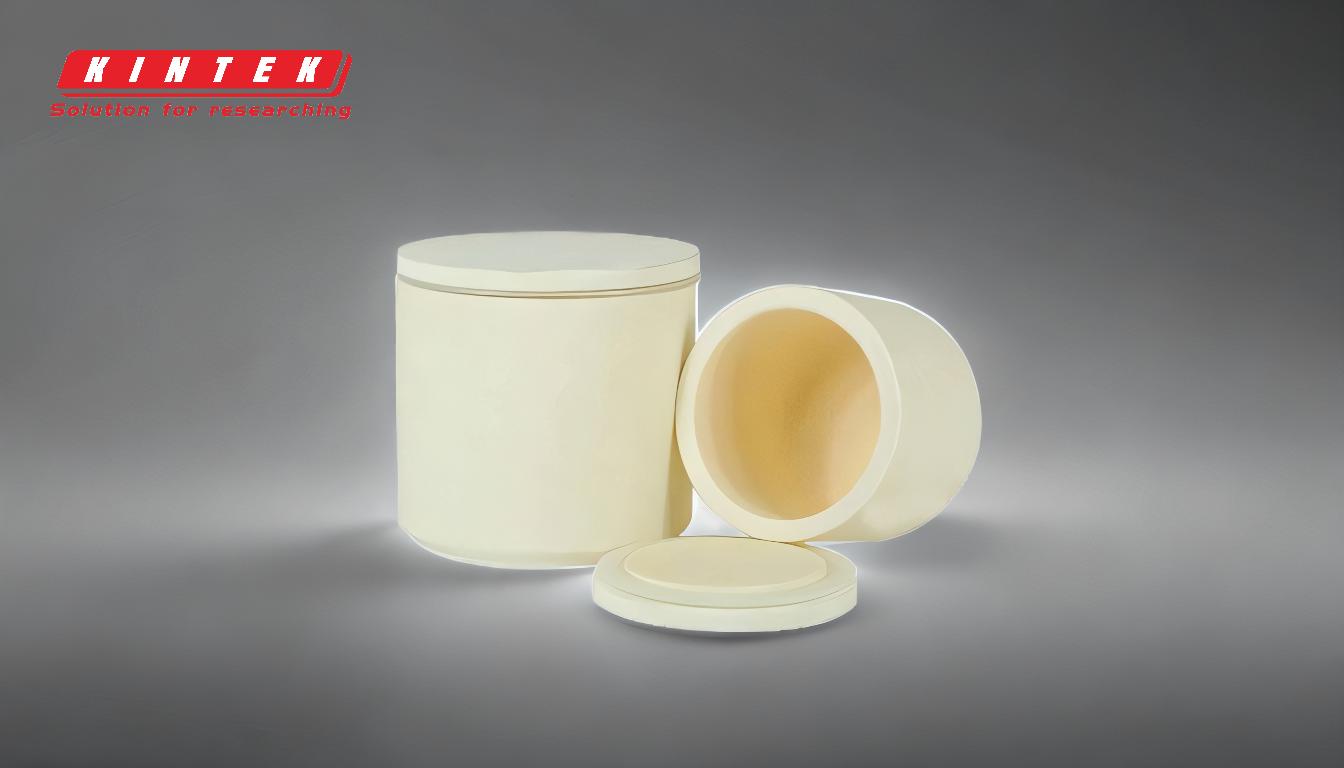
-
Effect of Ball Size on Particle Size Reduction:
- Smaller Balls: Smaller grinding balls are more effective for reducing particle size to finer levels. This is because smaller balls have a higher surface area relative to their volume, allowing for more contact points with the material being ground. This increased contact enhances the grinding efficiency, especially for achieving smaller particle sizes.
- Larger Balls: Larger balls are typically used for coarser grinding. They are more effective at breaking down larger particles but may not be as efficient for fine grinding due to fewer contact points and lower surface area.
-
Impact of Milling Time:
- Longer Milling Times: Achieving smaller particle sizes often requires longer milling times. Extended milling allows for more collisions between the grinding balls and the material, leading to finer particle sizes. However, excessively long milling times can lead to over-grinding, which may not be desirable for certain materials.
- Shorter Milling Times: Shorter milling times are generally sufficient for coarser grinding but may not be adequate for achieving very fine particles.
-
Influence of Mill Rotation Speed:
- Optimal Speed: The rotation speed of the mill affects the kinetic energy of the grinding balls. An optimal speed ensures that the balls are lifted to a certain height before falling, creating impact and shear forces that grind the material. Too high a speed can cause the balls to centrifuge, reducing grinding efficiency, while too low a speed may not provide enough energy for effective grinding.
-
Role of Mill Filling Ratio:
- Filling Ratio: The percentage of the mill volume filled with grinding medium (balls) affects the grinding efficiency. An optimal filling ratio ensures that there are enough balls to grind the material effectively without overcrowding, which can reduce the efficiency of the grinding process.
-
Material Properties:
- Hardness and Nature of Material: The hardness and nature of the material being ground play a crucial role in determining the grinding efficiency. Harder materials may require more energy and time to achieve the desired particle size, while softer materials may grind more easily.
-
Residence Time and Feed Rate:
- Residence Time: The time that the material spends in the mill chamber affects the degree of milling. Longer residence times allow for more thorough grinding, leading to finer particles.
- Feed Rate: The rate at which material is fed into the mill also impacts the grinding process. A consistent and appropriate feed rate ensures that the material is ground evenly and efficiently.
-
Mill Design and Dimensions:
- Drum Diameter and Length: The dimensions of the mill, particularly the drum diameter and the ratio of diameter to length, influence the grinding performance. An optimal L:D ratio (typically 1.56–1.64) ensures efficient grinding and productivity.
- Armor Surface Shape: The shape of the mill's interior surface can affect the movement of the grinding balls and the material, influencing the grinding efficiency.
-
Productivity Considerations:
- Milling Fineness: The desired fineness of the ground product affects the overall productivity of the mill. Finer grinding typically requires more time and energy, which can reduce throughput.
- Timely Removal of Ground Product: Efficient removal of the ground product from the mill is crucial to maintain productivity. Delayed removal can lead to over-grinding and reduced efficiency.
In summary, particle size in ball milling is influenced by a combination of factors including ball size, milling time, rotation speed, mill filling ratio, material properties, residence time, feed rate, and mill design. Optimizing these factors can help achieve the desired particle size distribution and improve the overall efficiency of the milling process.
Summary Table:
Factor | Impact on Ball Milling |
---|---|
Ball Size | Smaller balls for fine grinding; larger balls for coarse grinding. |
Milling Time | Longer times for finer particles; shorter times for coarser results. |
Rotation Speed | Optimal speed ensures efficient grinding; too high or low speeds reduce efficiency. |
Mill Filling Ratio | Optimal filling ratio maximizes grinding efficiency without overcrowding. |
Material Properties | Hardness and nature of material affect grinding time and energy requirements. |
Residence Time | Longer residence times lead to finer particles. |
Feed Rate | Consistent feed rate ensures even and efficient grinding. |
Mill Design | Drum diameter, length, and interior shape influence grinding performance. |
Productivity | Finer grinding reduces throughput; timely removal of ground product maintains efficiency. |
Ready to optimize your ball milling process? Contact our experts today for tailored solutions!