Plasma sputtering is a thin film deposition technique that involves the ejection of atoms from a solid target material through the bombardment of energized ions, typically from a noble gas like argon. These ejected atoms then deposit onto a substrate, forming a thin film. The process occurs in a vacuum chamber where a plasma environment is created by introducing a noble gas and applying a voltage. The plasma consists of ions, electrons, and neutral atoms, which interact to erode the target material and facilitate the deposition of a uniform coating on the substrate. This method is widely used in industries requiring precise and durable thin films, such as semiconductors, optics, and coatings.
Key Points Explained:
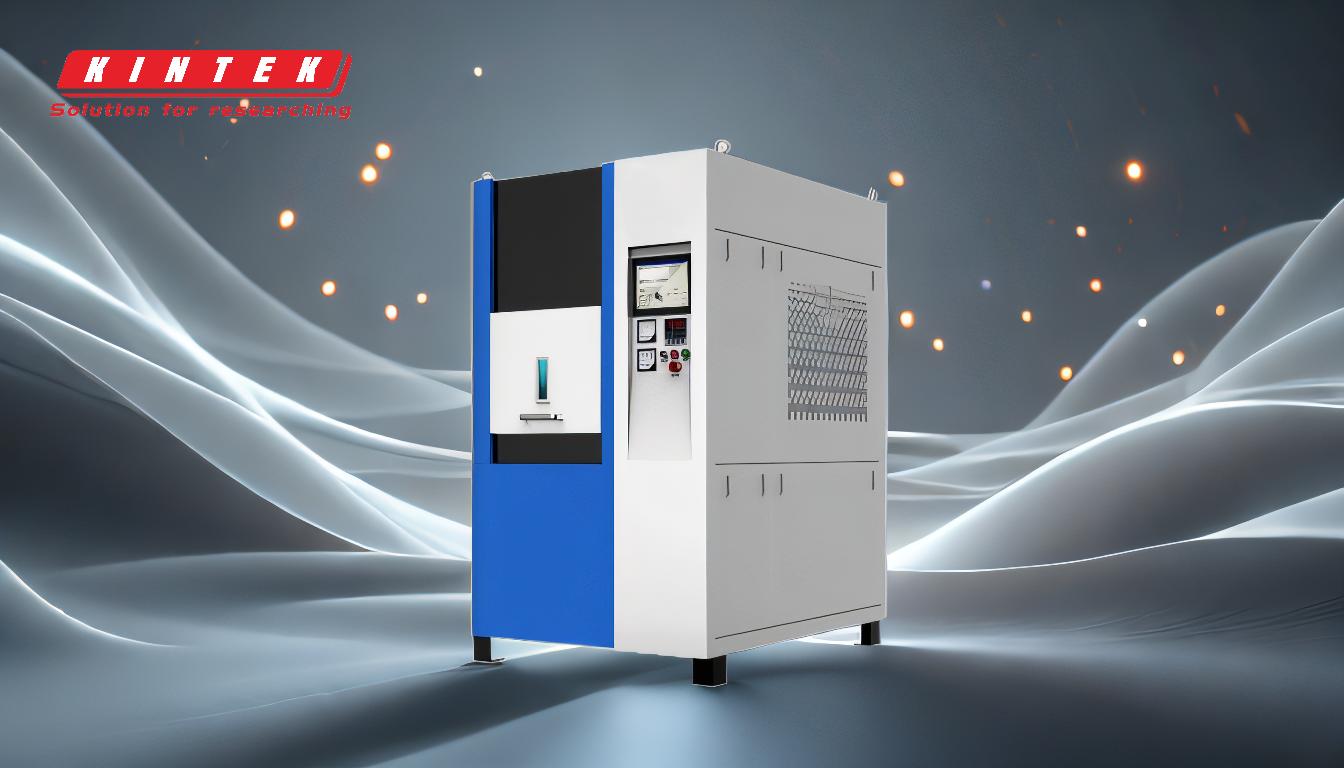
-
Creation of Plasma Environment:
- A vacuum chamber is evacuated to remove air and other contaminants.
- A noble gas, typically argon, is introduced into the chamber at a controlled pressure.
- A DC or RF voltage is applied to ionize the gas, creating a plasma consisting of ions, electrons, and neutral atoms.
-
Ion Bombardment of the Target:
- The target material, which is the source of the coating, is placed on a magnetron within the chamber.
- A negative electrical potential is applied to the target, causing free electrons to accelerate away from it.
- These electrons collide with argon atoms, ionizing them and creating positively charged argon ions.
- The argon ions are accelerated toward the target due to the negative potential, striking it with high energy.
-
Ejection of Target Material:
- The high-energy collisions between the argon ions and the target material transfer momentum, causing atoms from the target to be ejected.
- These ejected atoms are in the form of neutral particles and are released into the chamber.
-
Deposition onto the Substrate:
- The ejected neutral particles traverse the chamber and deposit onto the substrate, forming a thin film.
- The deposition process is highly controlled, ensuring a uniform and adherent coating.
-
Role of Momentum Transfer:
- Momentum transfer between the argon ions and the target atoms is crucial for the sputtering process.
- This transfer ensures efficient ejection of target material and uniform deposition on the substrate.
-
Applications and Advantages:
- Plasma sputtering is used in various industries, including semiconductors, optics, and coatings, due to its ability to produce precise and durable thin films.
- The process allows for the deposition of a wide range of materials, including metals, alloys, and compounds, with excellent adhesion and uniformity.
-
Re-sputtering and Atomic Bombardment:
- In some cases, re-sputtering is used, where deposited material is bombarded with atoms to refine the film's properties.
- This step can improve the film's density, adhesion, and overall quality.
By understanding these key points, one can appreciate the complexity and precision involved in plasma sputtering, making it a valuable technique for thin film deposition in various high-tech applications.
Summary Table:
Key Aspect | Description |
---|---|
Plasma Environment | Created by introducing argon gas and applying voltage in a vacuum chamber. |
Ion Bombardment | Argon ions strike the target material, ejecting atoms for deposition. |
Deposition Process | Ejected atoms form a uniform, adherent thin film on the substrate. |
Momentum Transfer | Crucial for efficient ejection and uniform deposition of target material. |
Applications | Widely used in semiconductors, optics, and coatings for precise thin films. |
Re-sputtering | Improves film density, adhesion, and quality through atomic bombardment. |
Discover how plasma sputtering can enhance your thin film processes—contact our experts today!