Sputter deposition is a widely used technique for depositing thin films onto substrates, leveraging high-energy ions to dislodge atoms from a target material, which then condense onto a substrate. This process occurs in a high-vacuum environment to ensure purity and is characterized by its flexibility, reliability, and ability to deposit a wide range of materials, including conductive and dielectric films. Sputter deposition has evolved significantly since its discovery in the 19th century, with advancements in vacuum technology and the introduction of radio frequency (rf) sputtering enabling its modern applications. The process involves momentum exchange between energetic ions and target atoms, often using inert gases like argon, and can be enhanced through reactive deposition to create high-quality oxide or nitride coatings.
Key Points Explained:
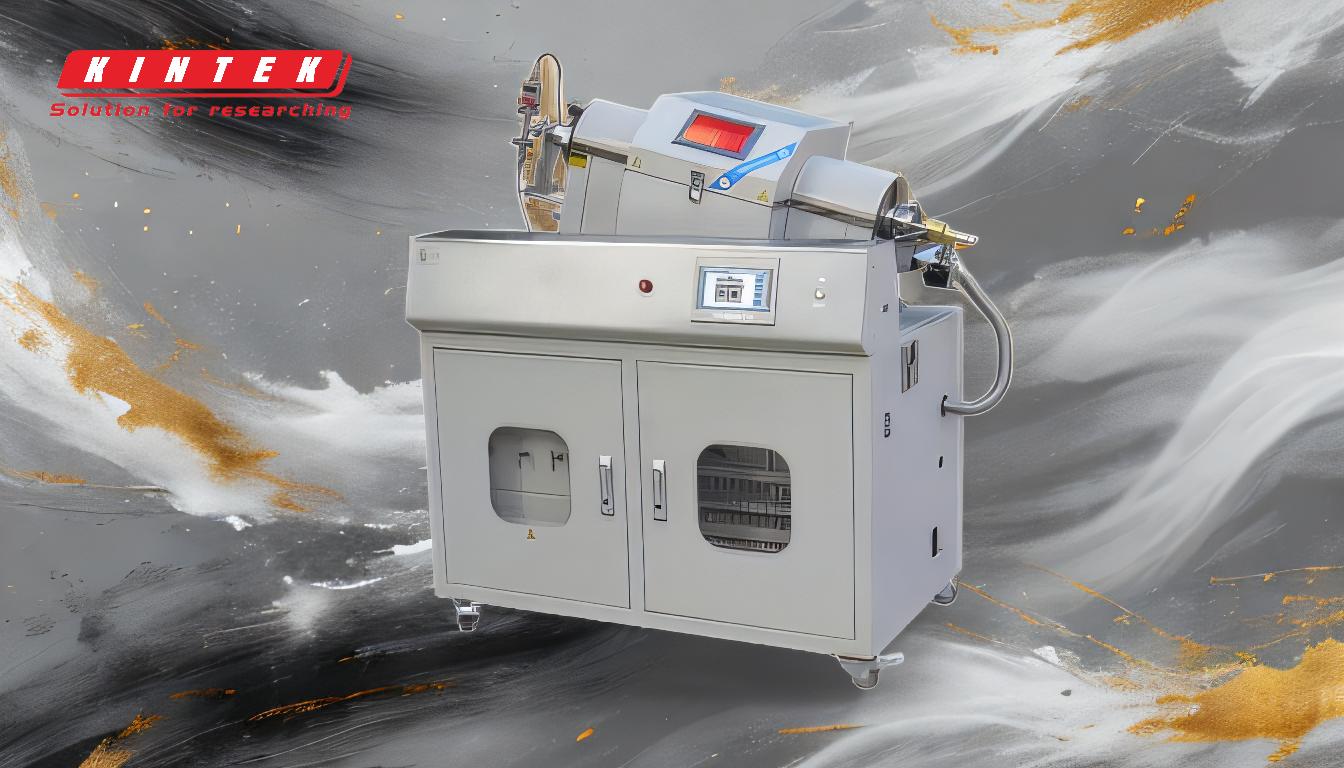
-
Fundamental Mechanism of Sputter Deposition:
- Sputter deposition works by bombarding a target material with high-energy ions, typically from an inert gas like argon. These ions dislodge atoms from the target through momentum transfer, a process known as sputtering.
- The ejected atoms travel through the vacuum chamber and deposit onto a substrate, forming a thin film. This method ensures uniform coating and strong adhesion of the film to the substrate.
-
Historical Development and Modern Applications:
- The phenomenon of sputtering was first observed in the mid-19th century by Grove during experiments with direct current (dc) glow discharges. By the 1930s, it found commercial applications.
- Although thermal evaporation became more popular in the 1950s, sputter deposition regained prominence in the late 1950s and 1960s due to advancements in vacuum technology and the introduction of rf sputtering, which allowed the deposition of dielectric materials.
-
Key Components and Process Conditions:
- Sputter deposition requires a high-vacuum environment to minimize contamination and ensure the purity of the deposited film.
- The process involves a target (source material), a substrate (where the film is deposited), and a plasma or ion beam to energize the inert gas ions. The target can be made of various materials, including metals, alloys, and ceramics.
-
Types of Sputtering Techniques:
- DC Sputtering: Used primarily for conductive materials, where a direct current is applied to create the plasma.
- RF Sputtering: Suitable for insulating materials, as it uses radio frequency to generate the plasma, avoiding charge buildup on the target.
- Reactive Sputtering: Involves introducing reactive gases (e.g., oxygen or nitrogen) into the chamber to form compound films like oxides or nitrides.
-
Advantages of Sputter Deposition:
- Flexibility: Can deposit a wide range of materials, including metals, alloys, and dielectrics.
- Uniformity: Provides even coating over complex geometries and large areas.
- Adhesion: Ensures strong bonding between the film and substrate.
- Purity: High-vacuum conditions minimize contamination, resulting in high-quality films.
-
Reactive Deposition and Material Synthesis:
- Reactive sputtering involves combining a metal target with reactive gases to create compound films, such as oxides or nitrides. This method often yields superior film properties compared to using pre-compounded materials.
- The process allows for the synthesis of new material combinations and tailored film properties, making it valuable for advanced applications in electronics, optics, and coatings.
-
Applications of Sputter Deposition:
- Semiconductor Manufacturing: Used to deposit conductive and insulating layers in integrated circuits.
- Optical Coatings: Applied in the production of anti-reflective and reflective coatings for lenses and mirrors.
- Solar Cells: Deposits thin films for photovoltaic applications.
- Decorative and Protective Coatings: Used in automotive, aerospace, and consumer goods for aesthetic and functional purposes.
Sputter deposition is a versatile and reliable method for thin-film deposition, offering precise control over film properties and compatibility with a wide range of materials. Its ability to produce high-quality, uniform coatings makes it indispensable in industries ranging from electronics to renewable energy.
Summary Table:
Aspect | Details |
---|---|
Mechanism | High-energy ions dislodge atoms from a target, which deposit onto a substrate. |
Environment | High-vacuum to ensure purity and minimize contamination. |
Key Components | Target material, substrate, plasma/ion beam, and inert gas (e.g., argon). |
Techniques | DC Sputtering, RF Sputtering, Reactive Sputtering. |
Advantages | Flexibility, uniformity, strong adhesion, and high purity. |
Applications | Semiconductors, optical coatings, solar cells, and protective coatings. |
Discover how sputter deposition can enhance your projects—contact our experts today!