Diamond-like carbon (DLC) is deposited using advanced techniques, primarily involving plasma-assisted chemical vapor deposition (PECVD) and physical vapor deposition (PVD). The process typically uses hydrocarbons (hydrogen and carbon) as precursors, which are ionized into plasma and then deposited onto a substrate. The deposition occurs at relatively low temperatures (around 300 °C) and often involves predeposition of silicon-based films to enhance adhesion. The resulting DLC coating is characterized by its high hardness, wear resistance, and durability, making it suitable for applications in automotive, aerospace, and industrial components.
Key Points Explained:
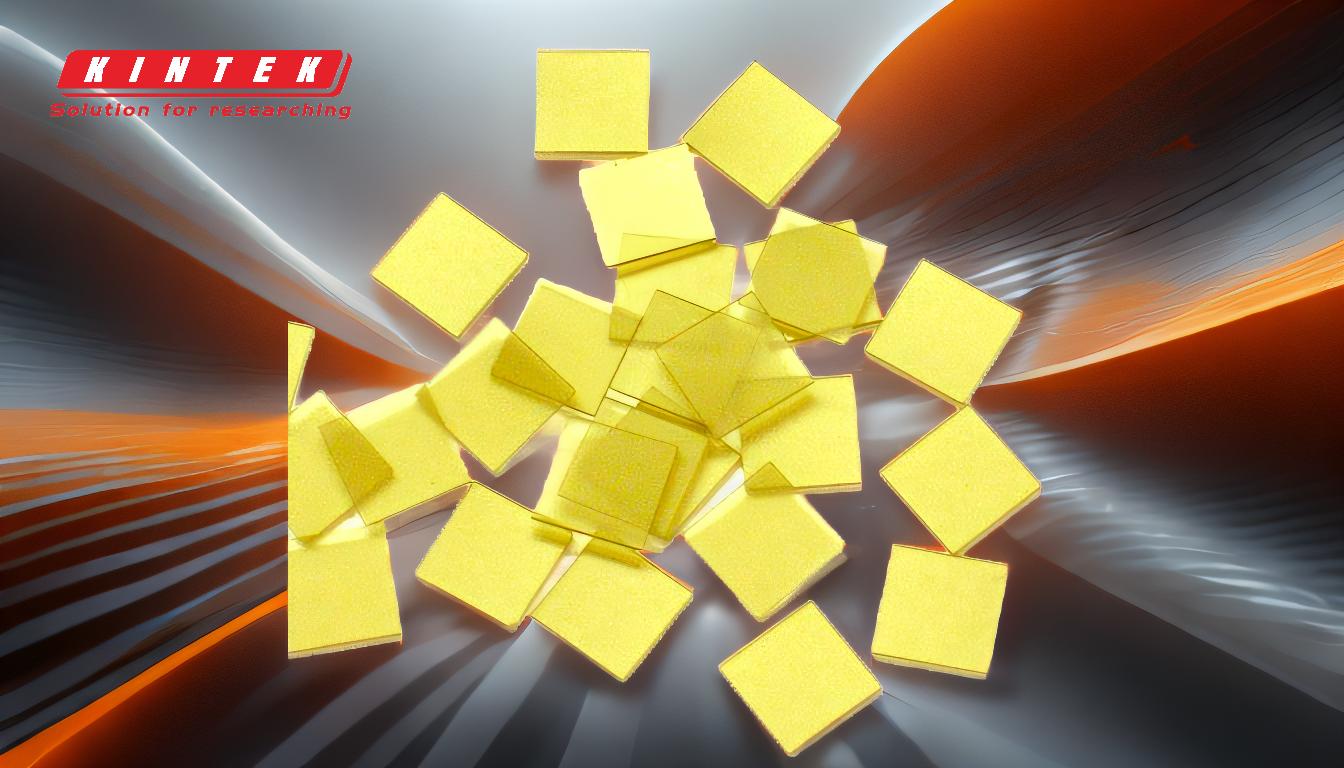
-
Deposition Techniques for DLC:
- Radio Frequency Plasma-Assisted Chemical Vapor Deposition (RF PECVD): This is the most common method for depositing DLC coatings. It involves ionizing hydrocarbon gases (e.g., methane, acetylene) into plasma using radio frequency energy. The plasma breaks down the hydrocarbons into reactive carbon and hydrogen species, which then deposit onto the substrate.
- Physical Vapor Deposition (PVD): While less common for DLC, PVD methods like sputtering can also be used. In sputtering, plasma ions bombard a carbon target, causing carbon atoms to vaporize and deposit onto the substrate.
-
Role of Hydrocarbons in DLC Deposition:
- Hydrocarbons (e.g., methane, acetylene) are the primary precursors for DLC deposition. When introduced into the plasma, they dissociate into carbon and hydrogen ions.
- These ions "rain" onto the substrate surface, where they recombine to form a hard, amorphous carbon structure with a significant fraction of sp3 bonds (similar to diamond).
-
Low-Temperature Deposition:
- DLC can be deposited at relatively low temperatures (around 300 °C), making it suitable for temperature-sensitive substrates like polymers or pre-treated metals.
- Low-temperature deposition also minimizes thermal stress and distortion in the substrate.
-
Adhesion Enhancement:
- To improve the adhesion of DLC coatings, a silicon-based interlayer is often predeposited using plasma-assisted chemical vapor deposition (PACVD).
- This interlayer acts as a bonding layer, particularly for challenging substrates like steel or hard metals, ensuring the DLC coating adheres strongly.
-
Properties of DLC Coatings:
- Hardness: DLC coatings are exceptionally hard due to the high fraction of sp3 carbon bonds, which mimic the structure of diamond.
- Wear Resistance: The hardness and low friction coefficient of DLC make it highly resistant to wear, extending the lifespan of coated components.
- Chemical Inertness: DLC is chemically inert, providing excellent corrosion resistance in harsh environments.
-
Applications of DLC Coatings:
- DLC coatings are widely used in automotive components (e.g., piston rings, fuel injectors), cutting tools, medical devices, and aerospace components.
- Their combination of hardness, wear resistance, and low friction makes them ideal for high-performance applications.
-
Process Control and Optimization:
- The deposition process requires precise control of parameters such as gas flow rates, plasma power, and substrate temperature to achieve the desired coating properties.
- Advanced techniques like pulsed plasma deposition can further enhance the uniformity and quality of DLC coatings.
By understanding these key points, a purchaser of DLC-coated equipment or consumables can make informed decisions about the suitability of DLC for their specific applications, ensuring optimal performance and durability.
Summary Table:
Aspect | Details |
---|---|
Deposition Techniques | RF PECVD (most common), PVD (e.g., sputtering) |
Precursors | Hydrocarbons (e.g., methane, acetylene) |
Deposition Temperature | ~300 °C (low-temperature process) |
Adhesion Enhancement | Silicon-based interlayer predeposited via PACVD |
Key Properties | High hardness, wear resistance, chemical inertness |
Applications | Automotive, aerospace, cutting tools, medical devices |
Process Optimization | Controlled gas flow, plasma power, substrate temperature, pulsed deposition |
Interested in DLC coatings for your applications? Contact us today to learn more!