Plasma creation in sputtering is a fundamental process in thin film deposition, where a high-energy environment is generated to sputter material from a target onto a substrate. The process begins by introducing a noble gas, typically argon, into a vacuum chamber. A high voltage is applied between the cathode (target) and the anode (chamber or substrate), ionizing the gas atoms. Electrons are accelerated away from the cathode, colliding with neutral gas atoms and causing ionization. These collisions create a plasma consisting of ions, electrons, and neutral atoms. The positively charged ions are then accelerated toward the negatively charged cathode, striking the target material and ejecting atoms, which deposit onto the substrate. This dynamic plasma environment is sustained by maintaining the voltage and gas pressure.
Key Points Explained:
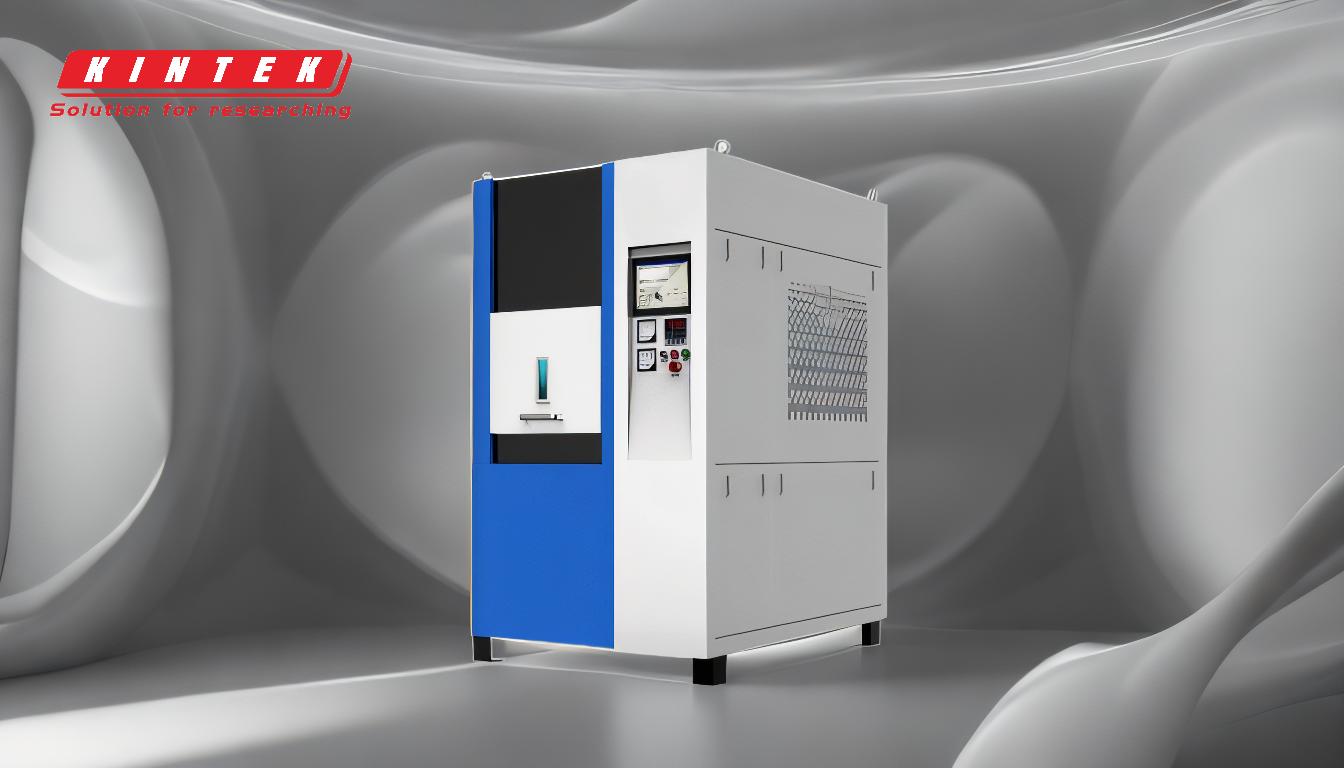
-
Introduction of Sputtering Gas:
- A noble gas, usually argon, is introduced into a vacuum chamber. Argon is preferred due to its inert nature and heavy atomic weight, which enhances sputtering efficiency.
- The chamber is evacuated to create a low-pressure environment, allowing the gas to ionize more easily when a voltage is applied.
-
Application of High Voltage:
- A high voltage is applied between the cathode (target material) and the anode (chamber wall or substrate). This creates an electric field within the chamber.
- The cathode is negatively charged, while the anode is grounded or positively charged, depending on the setup.
-
Ionization of Gas Atoms:
- Electrons are accelerated away from the cathode due to the electric field. These high-energy electrons collide with neutral argon atoms in the gas.
- Collisions between electrons and argon atoms cause ionization, stripping electrons from the argon atoms and creating positively charged argon ions and free electrons.
-
Formation of Plasma:
- The ionized gas forms a plasma, a state of matter consisting of positively charged ions, free electrons, and neutral atoms.
- The plasma is a dynamic environment where these particles are in near equilibrium, sustained by continuous ionization and recombination processes.
-
Acceleration of Ions Toward the Target:
- Positively charged argon ions are accelerated toward the negatively charged cathode (target material) due to the electric field.
- These high-energy ions collide with the target surface, transferring their kinetic energy to the target atoms.
-
Sputtering of Target Material:
- The energy transfer from the ions to the target atoms causes the target material to be ejected (sputtered) from the surface.
- The sputtered atoms travel through the vacuum chamber and deposit onto the substrate, forming a thin film.
-
Sustaining the Plasma:
- The plasma is sustained by maintaining the voltage and gas pressure within the chamber.
- Continuous ionization of gas atoms and recombination of ions and electrons ensure a stable plasma environment.
-
Plasma Glow:
- The plasma emits a characteristic glow due to the recombination of ions and electrons. When a free electron recombines with a positively charged ion, excess energy is released as light, creating the visible plasma glow.
-
DC and RF Sputtering:
- In DC sputtering, a direct current voltage is applied, and electrons are attracted to the anode, while positive ions are drawn to the cathode.
- In RF (radio frequency) sputtering, an alternating current is used, which allows the process to work with insulating materials by preventing charge buildup on the target.
-
Role of Noble Gases:
- Noble gases like argon are used because they are chemically inert and do not react with the target material or the substrate, ensuring a clean deposition process.
- The heavy atomic weight of argon increases the momentum transfer during collisions, enhancing sputtering efficiency.
By understanding these key points, one can appreciate the intricate process of plasma creation in sputtering and its critical role in thin film deposition technologies.
Summary Table:
Key Step | Description |
---|---|
Introduction of Sputtering Gas | Noble gas (argon) is introduced into a vacuum chamber for ionization. |
Application of High Voltage | High voltage creates an electric field, ionizing gas atoms. |
Ionization of Gas Atoms | Electrons collide with argon atoms, creating ions and free electrons. |
Formation of Plasma | Ionized gas forms a plasma of ions, electrons, and neutral atoms. |
Acceleration of Ions | Positively charged ions are accelerated toward the cathode (target material). |
Sputtering of Target Material | Ions strike the target, ejecting atoms that deposit onto the substrate. |
Sustaining the Plasma | Voltage and gas pressure are maintained to sustain the plasma environment. |
Plasma Glow | Recombination of ions and electrons emits light, creating the plasma glow. |
DC and RF Sputtering | DC uses direct current; RF uses alternating current for insulating materials. |
Role of Noble Gases | Argon's inert nature and heavy atomic weight enhance sputtering efficiency. |
Ready to optimize your thin film deposition process? Contact our experts today for tailored solutions!