Pyrolysis and gasification are both thermal conversion processes used to transform carbonaceous materials into useful products, but they differ significantly in their operating conditions, chemical reactions, and outputs. Pyrolysis occurs in the absence of oxygen or with a limited supply, leading to the production of gases, liquids, and solid char. In contrast, gasification involves partial oxidation, where a controlled amount of oxygen or steam is introduced, resulting in a predominantly gaseous output known as syngas. The key differences lie in the presence of oxygen, the extent of oxidation, and the types of products generated.
Key Points Explained:
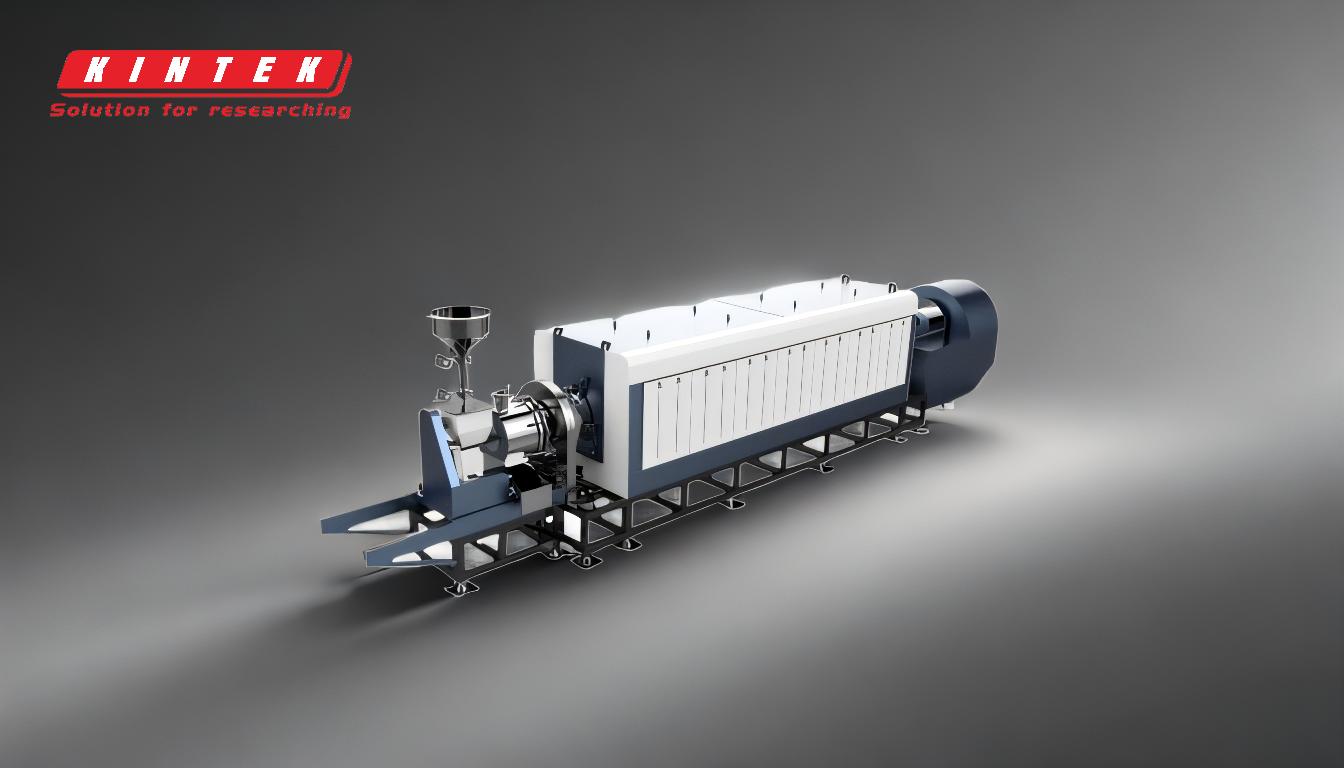
-
Presence of Oxygen:
- Pyrolysis: Operates in an inert atmosphere (absence of oxygen) or with a very limited supply of oxygen. This ensures that oxidation reactions do not occur to any significant extent.
- Gasification: Involves the introduction of a controlled amount of oxygen or steam, enabling partial oxidation of the feedstock. This is a fundamental distinction between the two processes.
-
Chemical Reactions:
- Pyrolysis: Primarily involves thermal decomposition (breaking down of chemical bonds due to heat) without significant oxidation. The process produces a mixture of gases, liquid bio-oil, and solid char.
- Gasification: Combines thermal decomposition with partial oxidation. The presence of oxygen or steam leads to additional chemical reactions, such as the conversion of carbon into carbon monoxide and hydrogen, producing syngas.
-
Output Products:
-
Pyrolysis: Yields three main products:
- Gases: Such as methane, hydrogen, and carbon monoxide.
- Liquids: Bio-oil, which can be further refined.
- Solids: Char, a carbon-rich residue.
- Gasification: Primarily produces a gaseous output known as syngas, which consists mainly of carbon monoxide, hydrogen, and some methane. The process minimizes the production of liquids and solids, focusing on maximizing gas yield.
-
Pyrolysis: Yields three main products:
-
Process Extent:
- Pyrolysis: Can be considered the first step in thermal decomposition, where the feedstock is broken down into simpler molecules without complete conversion.
- Gasification: Extends pyrolysis by further reacting the residual solids (char) with oxygen or steam to convert them into gaseous products. This makes gasification a more complete conversion process compared to pyrolysis.
-
Applications:
- Pyrolysis: Commonly used for producing bio-oil, which can be used as a fuel or chemical feedstock. The solid char can be used as a soil amendment or for carbon sequestration.
- Gasification: Primarily used for generating syngas, which can be utilized for electricity generation, as a chemical feedstock, or for producing synthetic fuels.
-
Energy Efficiency:
- Pyrolysis: Typically operates at lower temperatures (400-600°C) compared to gasification, making it less energy-intensive but also less efficient in terms of complete feedstock conversion.
- Gasification: Operates at higher temperatures (700-1200°C) and is more energy-intensive. However, it achieves a higher degree of feedstock conversion and produces a more versatile gaseous product.
-
Environmental Impact:
- Pyrolysis: Produces fewer emissions due to the absence of oxidation reactions. However, the liquid and solid by-products may require further processing or disposal.
- Gasification: While it produces a cleaner gaseous fuel, the process can generate more emissions due to the partial oxidation reactions. However, modern gasification systems are designed to capture and utilize these emissions effectively.
In summary, while both pyrolysis and gasification are thermal conversion processes, they differ fundamentally in the presence of oxygen, the nature of chemical reactions, and the types of products they generate. Pyrolysis is characterized by the absence of oxygen and the production of a mix of gases, liquids, and solids, whereas gasification involves partial oxidation and focuses on producing a gaseous output. These differences make each process suitable for specific applications and industries.
Summary Table:
Aspect | Pyrolysis | Gasification |
---|---|---|
Presence of Oxygen | Absence or limited oxygen supply | Controlled oxygen or steam introduction |
Chemical Reactions | Thermal decomposition without oxidation | Thermal decomposition with partial oxidation |
Output Products | Gases (methane, hydrogen), liquids (bio-oil), solids (char) | Predominantly syngas (carbon monoxide, hydrogen) |
Process Extent | First step in thermal decomposition | Extends pyrolysis by converting residual solids into gases |
Applications | Bio-oil production, soil amendment, carbon sequestration | Electricity generation, chemical feedstock, synthetic fuels |
Energy Efficiency | Lower temperatures (400-600°C), less energy-intensive | Higher temperatures (700-1200°C), more energy-intensive |
Environmental Impact | Fewer emissions, but by-products may require processing | Cleaner gaseous fuel, but partial oxidation may generate more emissions |
Discover the best thermal conversion process for your needs—contact our experts today!