The lifespan of a steel mold depends on various factors, including the type of steel used, the operating conditions, maintenance practices, and the complexity of the mold design. Generally, a well-maintained steel mold can last anywhere from 100,000 to over 1,000,000 cycles, depending on these factors. High-quality tool steels like H13 or P20, combined with proper heat treatment and surface coatings, can significantly extend the mold's life. Regular maintenance, such as cleaning, lubrication, and timely repairs, also plays a critical role in prolonging the mold's usability. Understanding these factors can help purchasers make informed decisions about mold selection and maintenance strategies.
Key Points Explained:
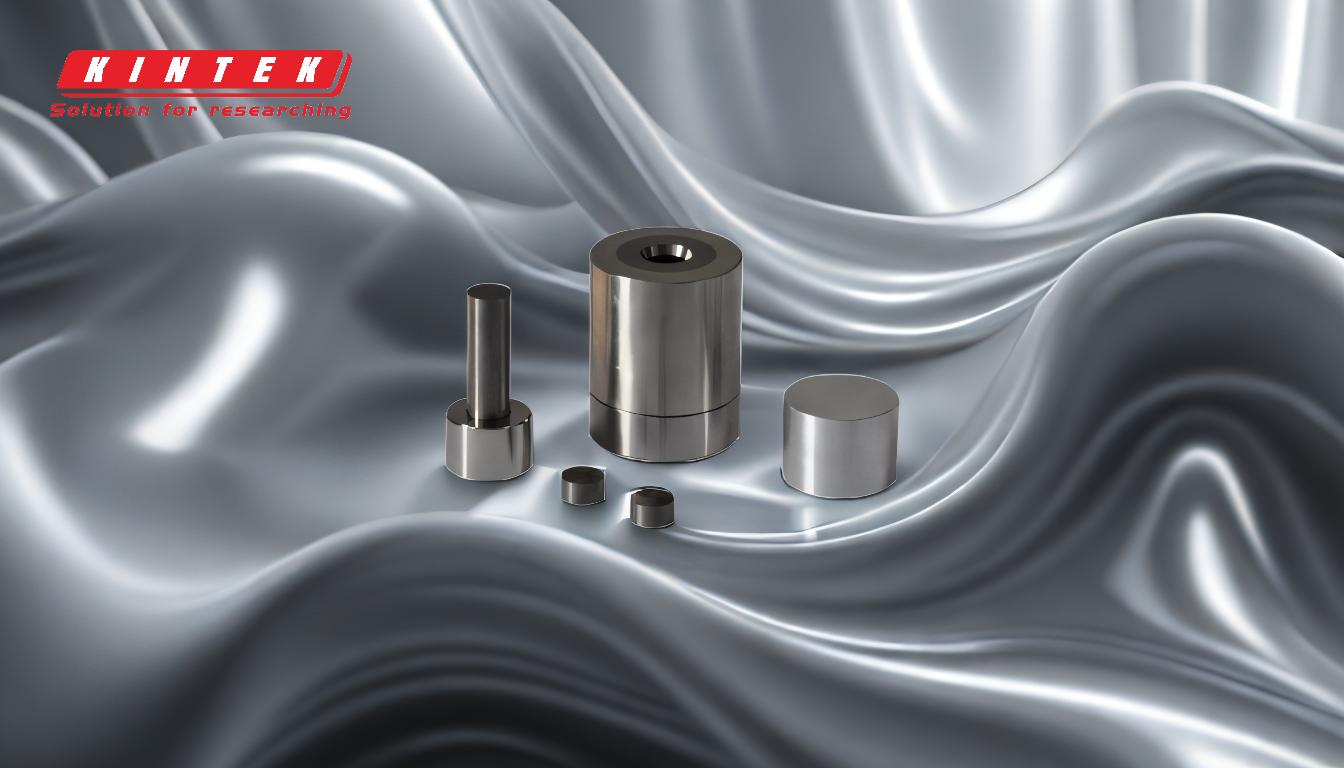
-
Type of Steel Used:
- The material of the mold is a primary determinant of its lifespan. High-quality tool steels, such as H13 or P20, are commonly used for their durability and resistance to wear and tear.
- H13 steel is known for its excellent thermal fatigue resistance, making it ideal for molds subjected to high temperatures and thermal cycling.
- P20 steel is often used for less demanding applications but still offers good wear resistance and machinability.
-
Operating Conditions:
- The environment in which the mold operates significantly impacts its longevity. Factors such as temperature, pressure, and the type of material being molded (e.g., plastic, rubber, or metal) play a crucial role.
- High-temperature applications, such as injection molding of thermoplastics, can cause thermal fatigue, leading to cracks and reduced mold life.
- Abrasive materials or corrosive substances can accelerate wear and require more frequent maintenance or replacement.
-
Maintenance Practices:
- Regular maintenance is essential to extend the life of a steel mold. This includes cleaning, lubrication, and inspection for wear or damage.
- Proper storage when not in use, such as in a controlled environment to prevent rust or contamination, also contributes to longevity.
- Timely repairs, such as fixing minor cracks or replacing worn components, can prevent further damage and extend the mold's usable life.
-
Mold Design Complexity:
- The complexity of the mold design affects its durability. Molds with intricate geometries or thin walls are more prone to stress concentrations and wear.
- Simplifying the design where possible and using robust geometries can reduce the likelihood of failure.
- Proper cooling channels and venting systems can also help manage thermal stress and improve mold life.
-
Surface Treatments and Coatings:
- Applying surface treatments or coatings, such as nitriding, chrome plating, or DLC (diamond-like carbon) coatings, can enhance the mold's resistance to wear, corrosion, and thermal fatigue.
- These treatments create a hardened surface layer that protects the underlying steel, extending the mold's lifespan.
-
Cycle Life Expectations:
- The expected number of cycles a mold can endure depends on the factors mentioned above. For example:
- Molds used in low-stress applications with proper maintenance can last over 1,000,000 cycles.
- High-stress applications, such as molding abrasive materials, may reduce the lifespan to 100,000–500,000 cycles.
- Understanding the specific requirements of your application can help set realistic expectations for mold life.
- The expected number of cycles a mold can endure depends on the factors mentioned above. For example:
By considering these factors, purchasers can make informed decisions about mold selection, maintenance, and replacement strategies, ultimately optimizing their production processes and reducing costs.
Summary Table:
Factor | Impact on Mold Lifespan |
---|---|
Type of Steel Used | High-quality steels like H13 or P20 enhance durability and thermal fatigue resistance. |
Operating Conditions | High temperatures, abrasive materials, or corrosive substances can reduce lifespan. |
Maintenance Practices | Regular cleaning, lubrication, and timely repairs significantly extend mold life. |
Mold Design Complexity | Simpler designs with robust geometries and proper cooling systems improve durability. |
Surface Treatments | Coatings like nitriding or DLC enhance wear and corrosion resistance. |
Cycle Life Expectations | Low-stress applications: 1,000,000+ cycles; high-stress: 100,000–500,000 cycles. |
Optimize your mold lifespan and production efficiency—contact our experts today for tailored solutions!