The time required to run a ball mill depends on several factors, including the desired fineness of the final product, the properties of the feed material, the size and density of the grinding balls, the rotation speed of the mill, and the filling ratio of the mill. Generally, ball milling can take anywhere from a few hours to over 100 hours, with typical processes requiring approximately 100 to 150 hours to produce a uniform fine powder. The specific duration is influenced by the interplay of these factors, and optimizing them can significantly affect the efficiency and productivity of the milling process.
Key Points Explained:
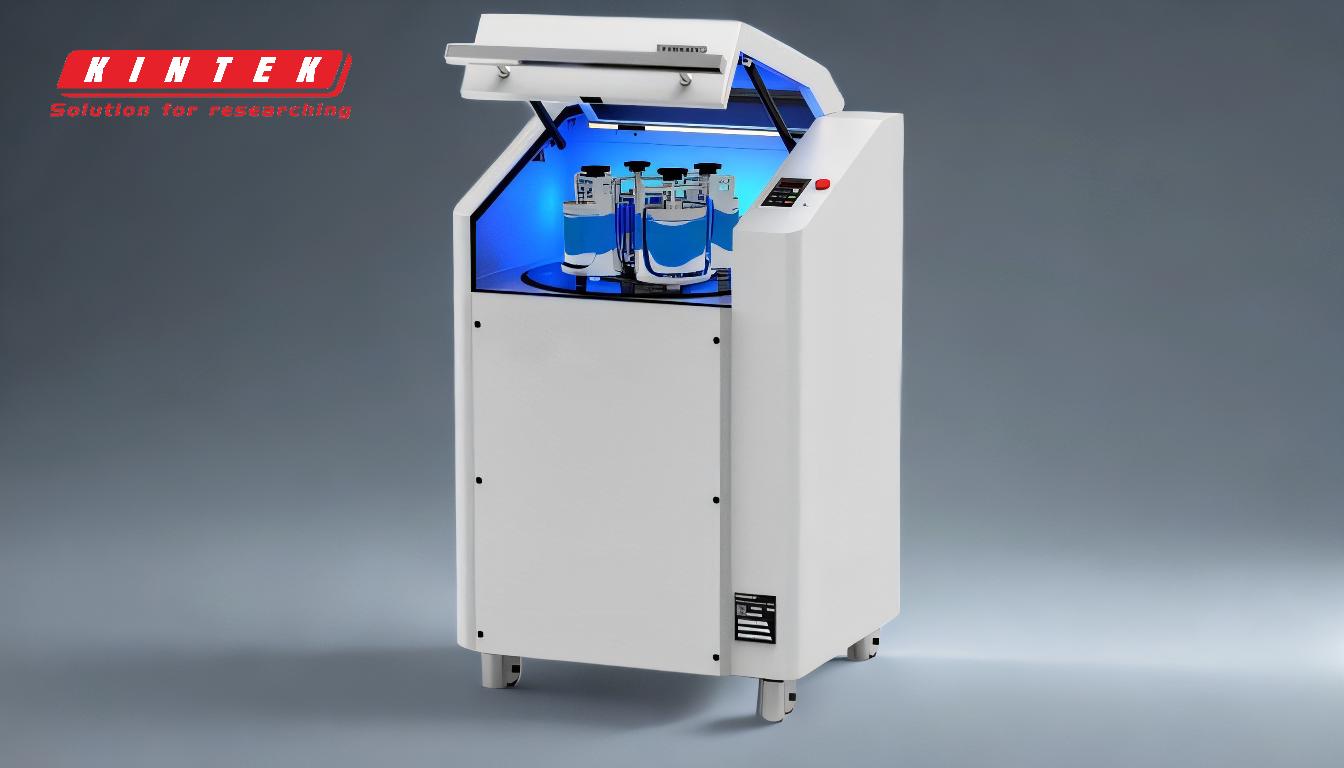
-
Desired Fineness of the Final Product:
- The time required for ball milling is directly related to the desired particle size. Smaller particles require longer grinding times. For example, producing nano-sized particles will take significantly longer than achieving coarser particles.
- Reference: "Generally, smaller balls and longer grinding times are required to produce smaller particles."
-
Properties of the Feed Material:
- The physical and chemical properties of the material being ground, such as hardness, density, and moisture content, influence the milling time. Harder materials require more time to grind to the desired fineness.
- Reference: "The degree of milling in a ball mill can be influenced by... the hardness of the grinding material."
-
Size and Density of Grinding Balls:
- The size, density, and number of grinding balls affect the efficiency of the milling process. Smaller balls are typically used for finer grinding, while larger balls are more effective for coarser grinding. The density of the balls also impacts the energy transferred to the material.
- Reference: "The degree of milling in a ball mill can be influenced by the size, density, and number of balls."
-
Rotation Speed of the Mill:
- The rotation speed of the mill determines the kinetic energy imparted to the grinding balls. Optimal rotation speeds ensure effective grinding without causing excessive wear or overheating. Too high or too low speeds can reduce efficiency.
- Reference: "Factors that affect the grinding performance of a ball mill include the speed of rotation."
-
Filling Ratio of the Mill:
- The filling ratio, or the percentage of the mill volume filled with grinding medium, affects the milling time. An optimal filling ratio ensures efficient grinding by balancing the impact and attrition forces.
- Reference: "Factors that affect the grinding performance of a ball mill include... the filling ratio of the mill."
-
Residence Time of Material in the Mill:
- The residence time, or the time the material spends in the mill chamber, is crucial for achieving the desired fineness. Longer residence times generally result in finer particles but also increase the overall milling time.
- Reference: "The degree of milling in a ball mill can be influenced by the residence time of material in the mill chamber."
-
Typical Milling Duration:
- Ball milling processes typically take between 100 to 150 hours to produce a uniform fine powder. However, this duration can vary based on the factors mentioned above.
- Reference: "The ball milling process typically takes approximately 100 to 150 hours to produce uniform fine powder."
-
Optimization of Milling Parameters:
- Optimizing parameters such as drum diameter, length-to-diameter ratio, and armor surface shape can enhance productivity and reduce milling time. The optimal L:D ratio for ball mills is typically between 1.56 and 1.64.
- Reference: "Productivity of ball mills depends on drum diameter, the ratio of drum diameter to length (optimum L:D ratio is 1.56–1.64)."
By understanding and controlling these factors, the milling time can be optimized to achieve the desired product quality efficiently.
Summary Table:
Factor | Impact on Milling Time |
---|---|
Desired Fineness of Final Product | Smaller particles require longer grinding times (e.g., nano-sized particles take longer). |
Properties of Feed Material | Harder materials increase milling time due to higher resistance. |
Size and Density of Grinding Balls | Smaller balls for fine grinding; larger balls for coarse grinding. |
Rotation Speed of the Mill | Optimal speeds ensure efficient grinding; too high or low reduces efficiency. |
Filling Ratio of the Mill | Optimal filling ratio balances impact and attrition forces for efficient grinding. |
Residence Time of Material | Longer residence times yield finer particles but increase milling time. |
Typical Milling Duration | 100–150 hours for uniform fine powder; varies based on factors. |
Optimization of Milling Parameters | Optimizing L:D ratio, drum diameter, and armor shape enhances productivity. |
Want to optimize your ball milling process? Contact our experts today for tailored solutions!