The duration of plastic pyrolysis depends on several factors, including the type of plastic, the scale of the operation, and the specific process conditions. Generally, the process can take anywhere from a few hours to a full day, depending on whether it is a fast or slow pyrolysis process. For example, in a small pyrolysis machine, a single batch may take around 19 hours, including 10 hours for the reaction, 7 hours for cooling, and 2 hours for discharging. Larger-scale operations or different types of plastic may require adjustments to these timelines. The process involves multiple steps, such as preprocessing, heating, and cooling, which all contribute to the total time required.
Key Points Explained:
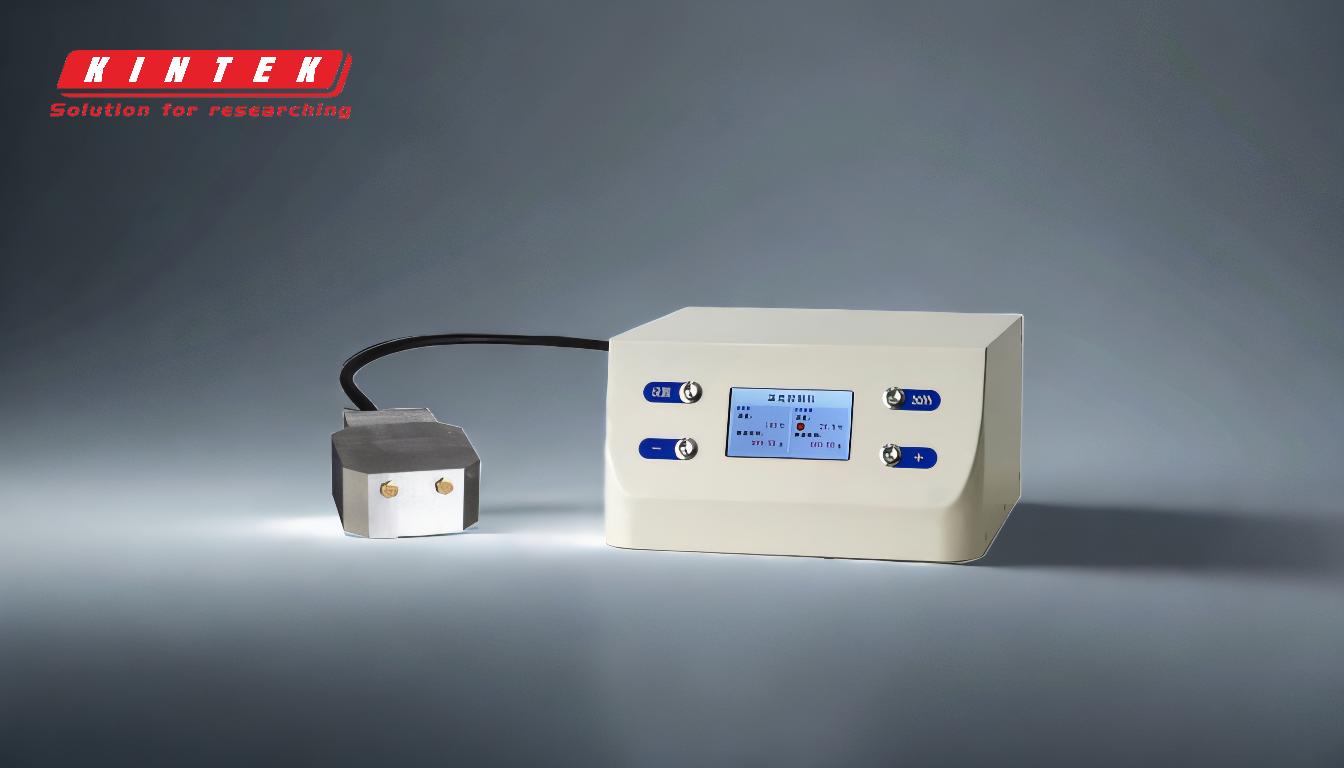
-
Factors Influencing Pyrolysis Duration:
- Type of Plastic: Different plastics have varying molecular structures and thermal properties, which affect how quickly they break down during pyrolysis.
- Scale of Operation: Small-scale machines may take longer per batch compared to industrial-scale operations, which can process larger volumes more efficiently.
- Process Conditions: Temperature, pressure, and the presence of catalysts can significantly influence the speed of the pyrolysis reaction.
-
Steps in the Plastic Pyrolysis Process:
- Preprocessing: This includes shredding and drying the plastic to ensure it meets the size and moisture requirements for efficient pyrolysis. This step can take several hours, depending on the volume and type of plastic.
- Pyrolysis Reaction: The actual pyrolysis process involves heating the plastic to around 280 degrees Celsius in the absence of oxygen. This step typically takes about 10 hours in a small machine but can vary based on the scale and conditions.
- Cooling and Discharging: After the reaction, the products need to cool down, which can take around 7 hours, followed by 2 hours for discharging the final products, such as pyrolysis oil and carbon black.
-
Fast vs. Slow Pyrolysis:
- Fast Pyrolysis: This process is designed to maximize the yield of liquid products (pyrolysis oil) and can be completed in a few seconds to a few minutes. It requires higher temperatures and faster heating rates.
- Slow Pyrolysis: This method takes several hours and is often used to produce more solid products like char or carbon black. It involves slower heating rates and lower temperatures compared to fast pyrolysis.
-
Batch Processing Time:
- In a small pyrolysis machine, a single batch can take approximately 19 hours, broken down into:
- 10 hours for the pyrolysis reaction.
- 7 hours for cooling.
- 2 hours for discharging the products.
- This timeline can vary depending on the specific equipment and the type of plastic being processed.
- In a small pyrolysis machine, a single batch can take approximately 19 hours, broken down into:
-
End Products and Their Impact on Duration:
- Pyrolysis Oil: The primary product, which requires distillation and purification, adding to the overall process time.
- Carbon Black and Syngas: These by-products also need to be collected and processed, which can extend the total duration of the pyrolysis cycle.
-
Optimization for Efficiency:
- Preprocessing Efficiency: Ensuring that the plastic is properly shredded and dried can reduce the time required for the pyrolysis reaction.
- Temperature Control: Maintaining optimal temperatures throughout the process can help speed up the reaction without compromising the quality of the end products.
- Automation: Using automated systems for feeding, heating, and discharging can significantly reduce the total time required for each batch.
In conclusion, the duration of plastic pyrolysis is influenced by a combination of factors, including the type of plastic, the scale of the operation, and the specific process conditions. Understanding these factors can help optimize the process for efficiency and yield, whether in small-scale or industrial applications.
Summary Table:
Factor | Impact on Duration |
---|---|
Type of Plastic | Different plastics break down at varying speeds due to molecular structure. |
Scale of Operation | Small-scale machines take longer per batch; industrial-scale processes are faster. |
Process Conditions | Temperature, pressure, and catalysts influence reaction speed. |
Fast Pyrolysis | Takes seconds to minutes; maximizes liquid product yield. |
Slow Pyrolysis | Takes several hours; produces more solid products like char. |
Batch Processing | Small machine: ~19 hours (10h reaction, 7h cooling, 2h discharging). |
End Products | Pyrolysis oil, carbon black, and syngas require additional processing time. |
Optimization Tips | Preprocessing, temperature control, and automation can reduce overall duration. |
Ready to optimize your plastic pyrolysis process? Contact our experts today for tailored solutions!