The number of times a crucible can be used depends on several factors, including the material of the crucible, the type of metals or compounds being melted, the operating temperatures, and the maintenance practices. Crucibles made from high-temperature-resistant materials like alumina, silicon carbide, or graphite can often be reused multiple times if properly cared for. However, repeated exposure to extreme heat, chemical reactions, and mechanical stress can degrade the crucible over time, leading to cracks, contamination, or failure. Proper cleaning, avoiding thermal shock, and matching the crucible to the specific application can extend its lifespan. In industrial or laboratory settings, crucibles may be reused dozens or even hundreds of times, but they must be regularly inspected for wear and replaced when necessary to ensure safety and accuracy.
Key Points Explained:
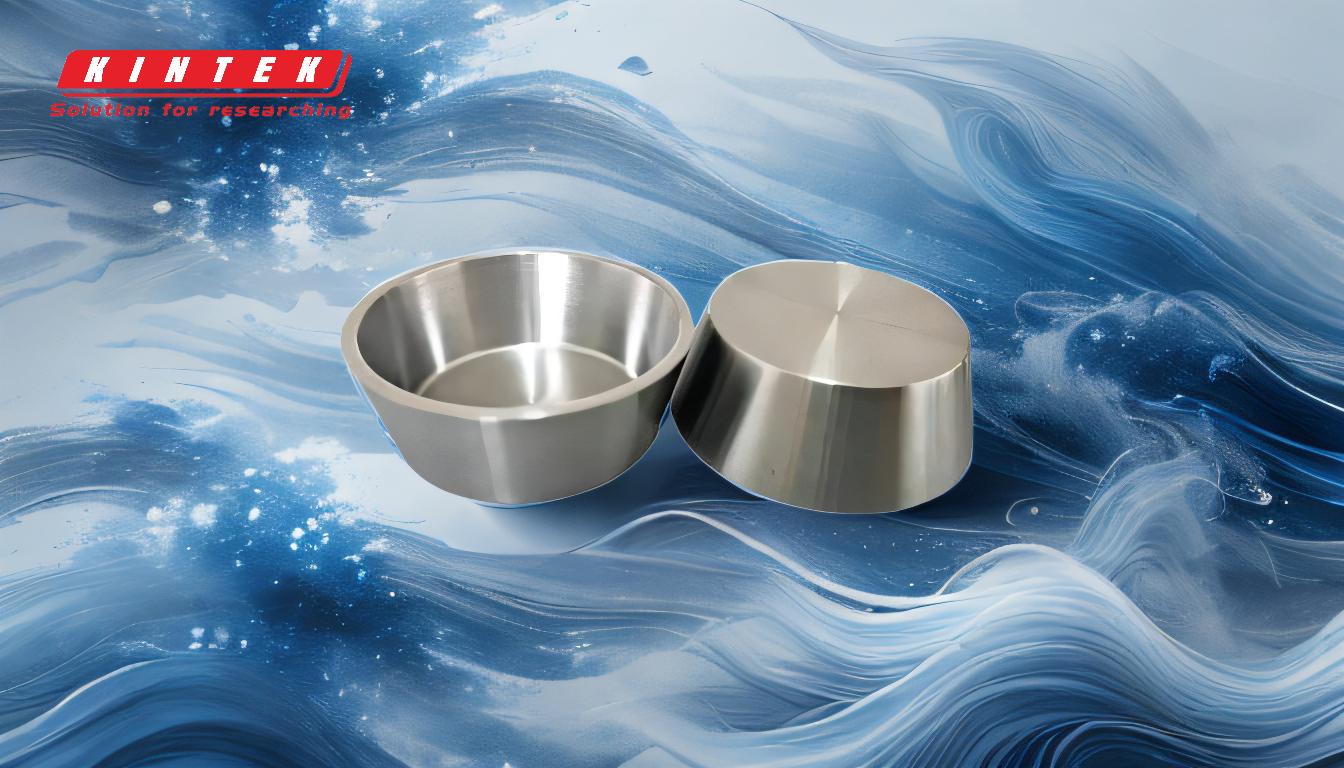
-
Material of the Crucible:
- Crucibles are made from materials like alumina, silicon carbide, porcelain, or graphite, each with different durability and resistance properties.
- High-quality materials can withstand repeated use but are subject to wear and tear over time.
-
Type of Metals or Compounds Melted:
- The chemical composition of the materials being melted can affect the crucible's lifespan. Reactive metals or corrosive compounds may degrade the crucible faster.
- For example, melting aluminum or its alloys can cause erosion of graphite crucibles due to chemical reactions.
-
Operating Temperatures:
- Crucibles are designed to withstand high temperatures, but prolonged exposure to extreme heat can cause thermal fatigue.
- Rapid temperature changes (thermal shock) can lead to cracking or failure, reducing the number of uses.
-
Maintenance and Handling:
- Proper cleaning after each use prevents contamination and extends the crucible's life.
- Avoiding mechanical damage, such as dropping or rough handling, is crucial for maintaining structural integrity.
-
Application-Specific Factors:
- The crucible must be matched to the specific application, including the furnace type, melting process, and operational requirements.
- For example, induction furnaces require crucibles with specific electrical resistivity to prevent overheating.
-
Inspection and Replacement:
- Regular inspection for cracks, erosion, or contamination is essential to determine when a crucible should be replaced.
- Reusing a damaged crucible can lead to safety hazards or inaccurate results in laboratory settings.
-
Expected Lifespan:
- In industrial settings, crucibles may be reused dozens to hundreds of times, depending on the factors mentioned above.
- In laboratory settings, crucibles may have a shorter lifespan due to the need for high accuracy and minimal contamination.
By considering these factors and implementing proper care and maintenance practices, the number of times a crucible can be used can be maximized while ensuring safety and performance.
Summary Table:
Factor | Impact on Crucible Lifespan |
---|---|
Material | High-quality materials like alumina or graphite withstand repeated use but degrade over time. |
Metals/Compounds Melted | Reactive or corrosive materials (e.g., aluminum) can erode crucibles faster. |
Operating Temperatures | Prolonged extreme heat or thermal shock can cause cracks or failure. |
Maintenance | Proper cleaning and handling prevent contamination and extend lifespan. |
Application | Matching crucibles to specific processes (e.g., induction furnaces) ensures optimal performance. |
Inspection | Regular checks for cracks or wear are essential for safety and accuracy. |
Lifespan | Industrial crucibles: dozens to hundreds of uses; lab crucibles: shorter due to precision needs. |
Need help choosing or maintaining crucibles? Contact our experts today for tailored solutions!